OWATONNA, Minn. — A water tower emblazoned with the name of this southern Minnesota town soars above the Viracon campus that stretches 1.2 million square feet.
The headquarters, factory and warehouse spaces sprawl horizontally, but inside, glass is fabricated and dispatched for structures that will alter skylines across the globe, including the bold, iconic new Vikings stadium that is rising in Minneapolis.
Insulated glass is fabricated in this factory and shipped to approximately 35 countries each year, but there is particular pride in working on units whose destination is just 65 miles north.
The first units of about 8,500 total that will be used for the stadium were installed Wednesday by workers from Twin Cities-based specialty contractor, Egan Company/InterClad. Installation is scheduled to continue for roughly six months, providing enclosure of the stadium in November. The venue remains on schedule to be completed in July 2016.
Viracon VP of Sales and Marketing Garret Henson said the stadium project is only the second he can recall in his 22 years with the company during which a special T-shirt was created. Designed through a campaign, the shirt has been distributed to 1,500 employees, a substantial increase from the 20 employees on site when the company launched in 1970.
For all of the latest information on the new stadium, check out **newminnesotastadium.com*. For future notifications, join the *new stadium waiting list*.*
The shirt features the Viracon and Norseman Vikings logos, along with the phase, "A Winning Combination." Several workers were wearing their shirts underneath their gear Tuesday during production of some of the units that will be used for the stadium.
"I can only remember a couple of times when we created a campaign and did something with a T-shirt," Henson said. "The other building we did that on was for the Freedom Tower in New York City, so that will tell you the emotional draw that we have to the proximity of the stadium."
Henson said he's explained to his sons, ages 12 and 9, that Viracon has produced glass used in several of the tallest buildings in the world — the Freedom Tower, Willis (formerly Sears) Tower in Chicago, Taipei 101 in Taiwan and the Petronas Towers in Kuala Lumpur, Malaysia — but the stadium is of particular interest.
"We'll get to go up there and to have your children say my dad built this or was part of a company that did something special for this stadium is going to be great," Henson said. "That's going to be fantastic for us, and I hope all of our employees get that opportunity to walk on the outside of the stadium and look at what we accomplished or get in and witness a game."
Greg Sanborn, a product supervisor who will celebrate his 25th anniversary with Viracon in April, said most of the workers in Owatonna never get a chance to see in-person how what they've done adds to a construction project, but that won't be the case with the Vikings stadium.
Sanborn, a native of Medford, just 6 miles or so from Viracon's home base, spoke to members of the media Tuesday as workers ran plates of glass through the lamination process. He said workers have been asking when units used for the stadium will be run through the line, which shows their particular interest and desire to participate first-hand in the project.
TEAMWORK ON THE LINE
When sheets arrive from a supplier, the external side is treated with a "high-performance coating" on the exterior side that will allow light to transmit while limiting solar heat from passing through. There are 40 different coatings Viracon, a subsidiary of Minneapolis-based Apogee Enterprises, Inc., can use on about 25 different colors of glass.
The clear glass selected for the stadium is one of the signature design elements to aesthetically offer views of the Minneapolis skyline, particularly through the west end of the stadium that features five of the world's largest pivoting glass doors. It will offer a feeling of the outdoors while providing protection from elements that can turn brutal by a season's end and allow views into the stadium for passersby.
Earlier this week the glass framing began on the east side of the new Vikings stadium, with the glass itself slated to be installed next week.
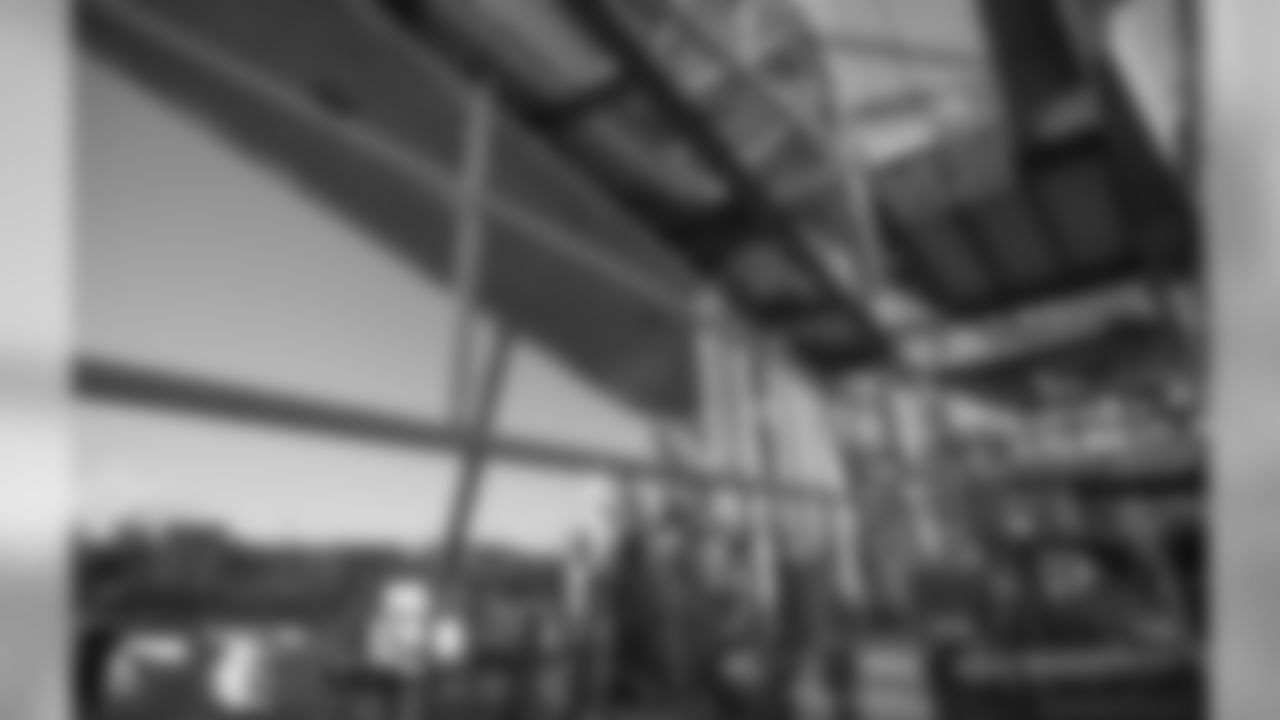
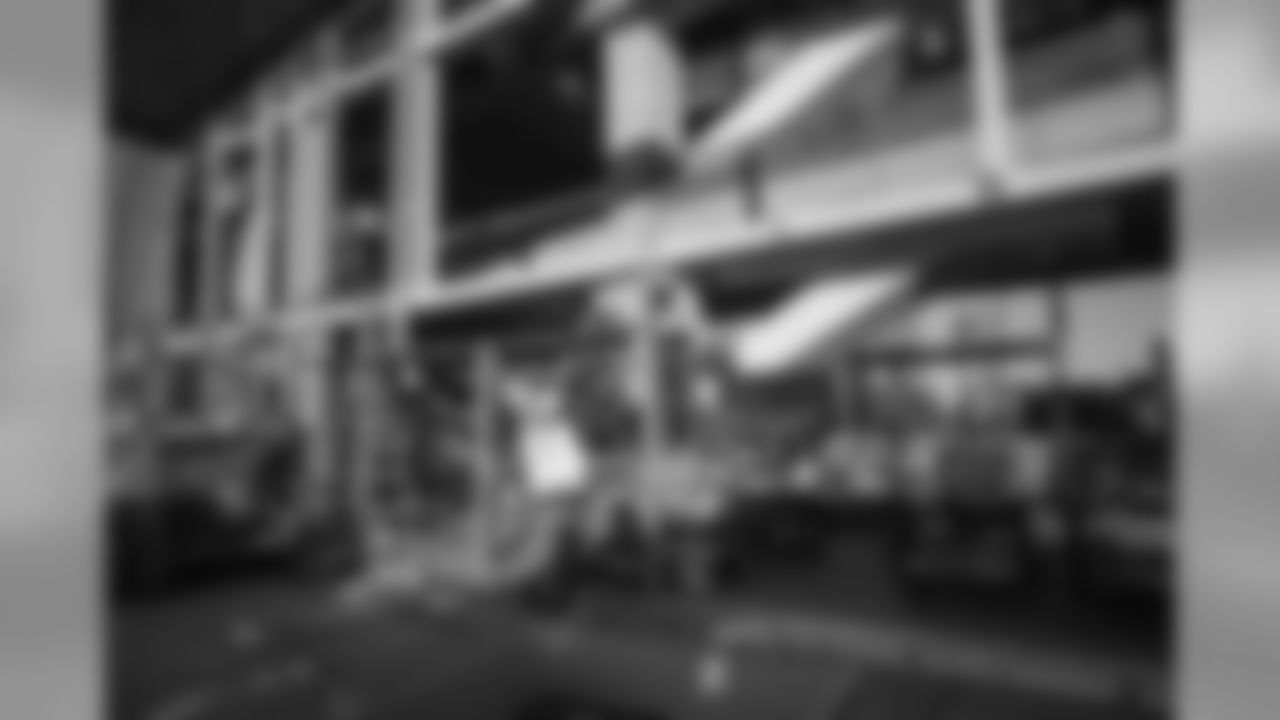
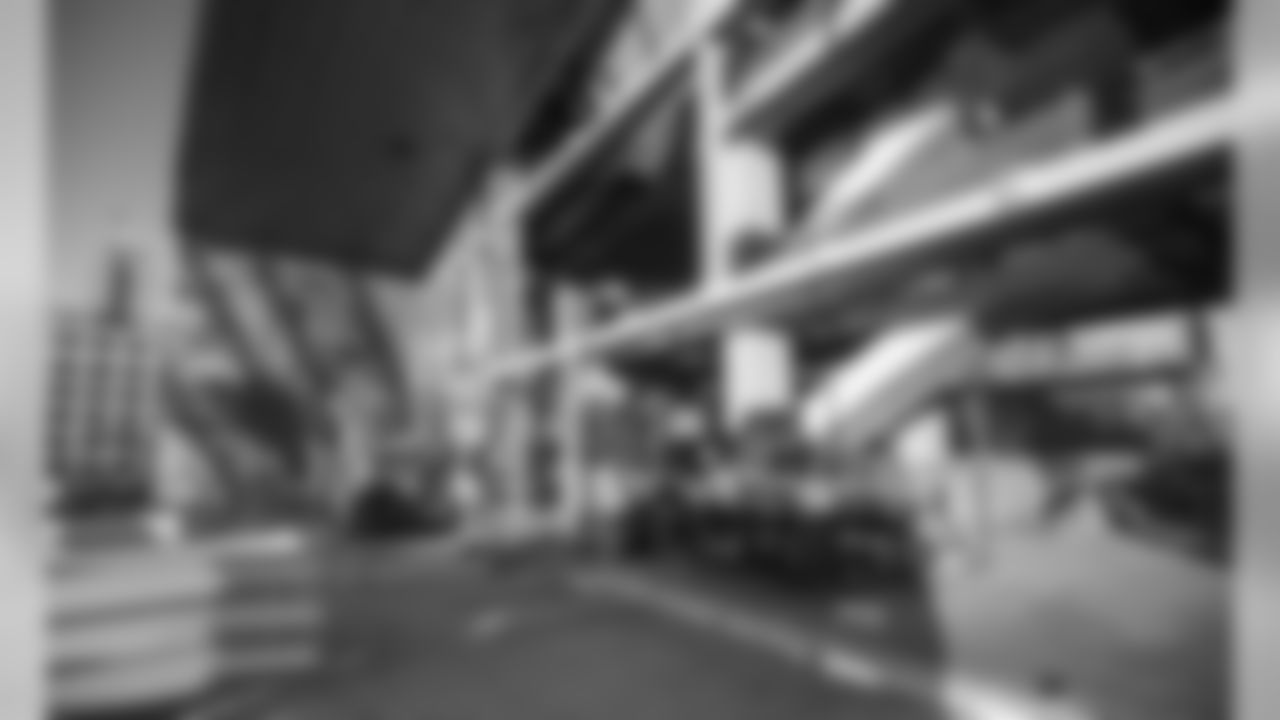
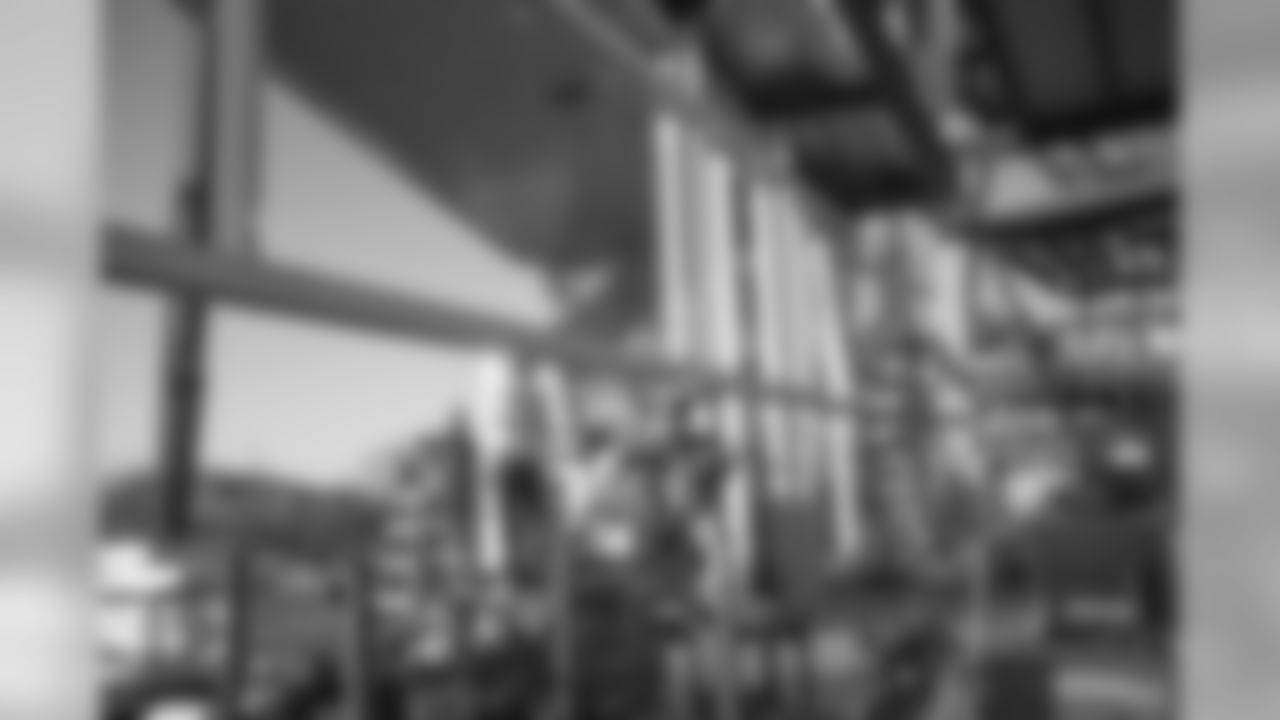
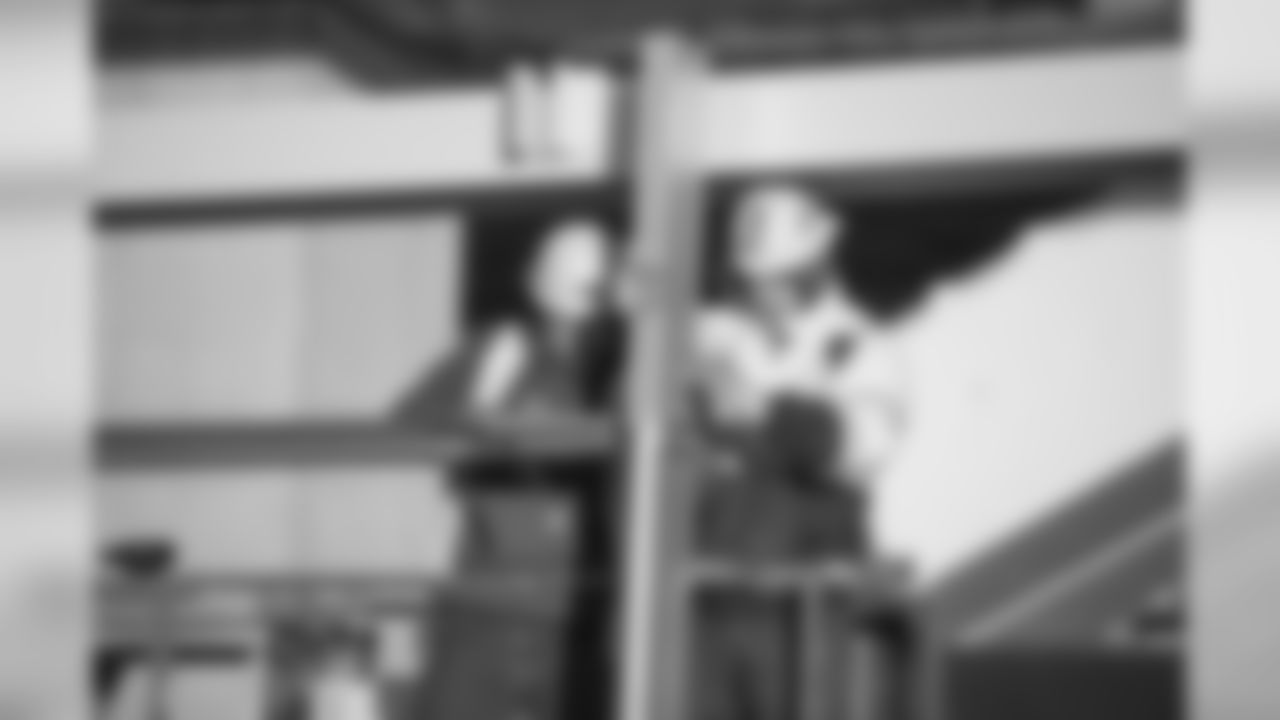
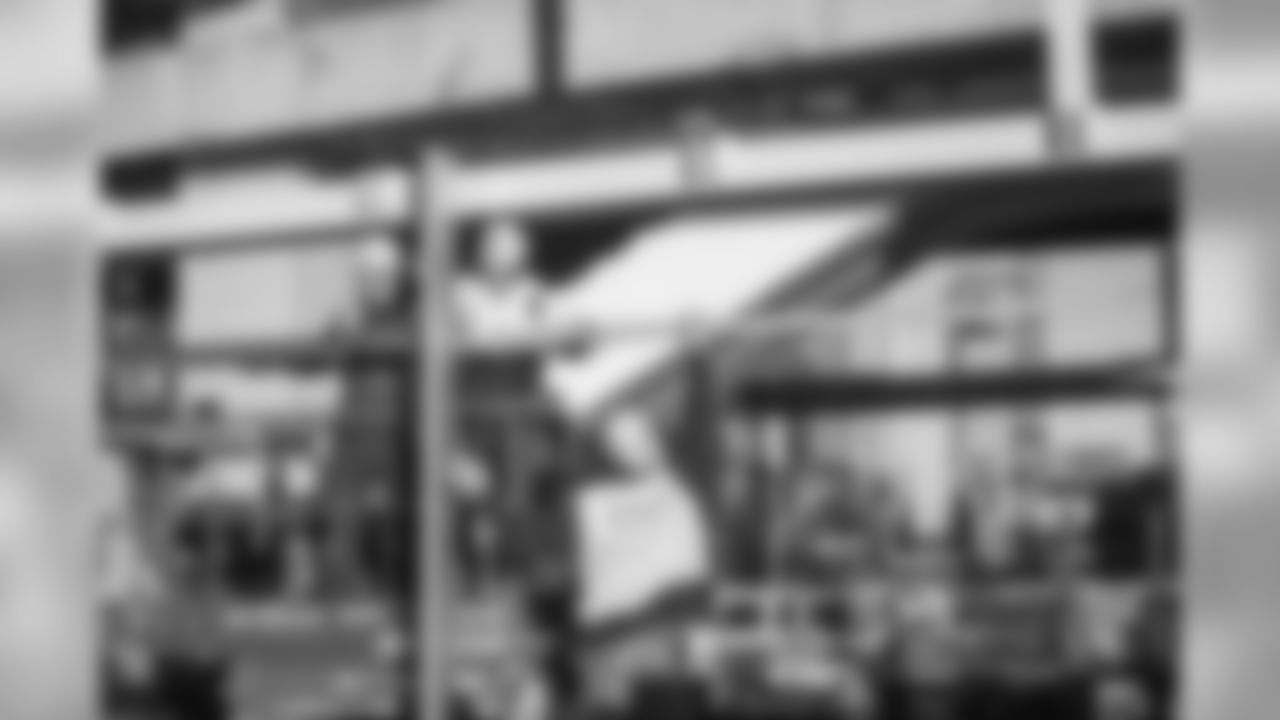
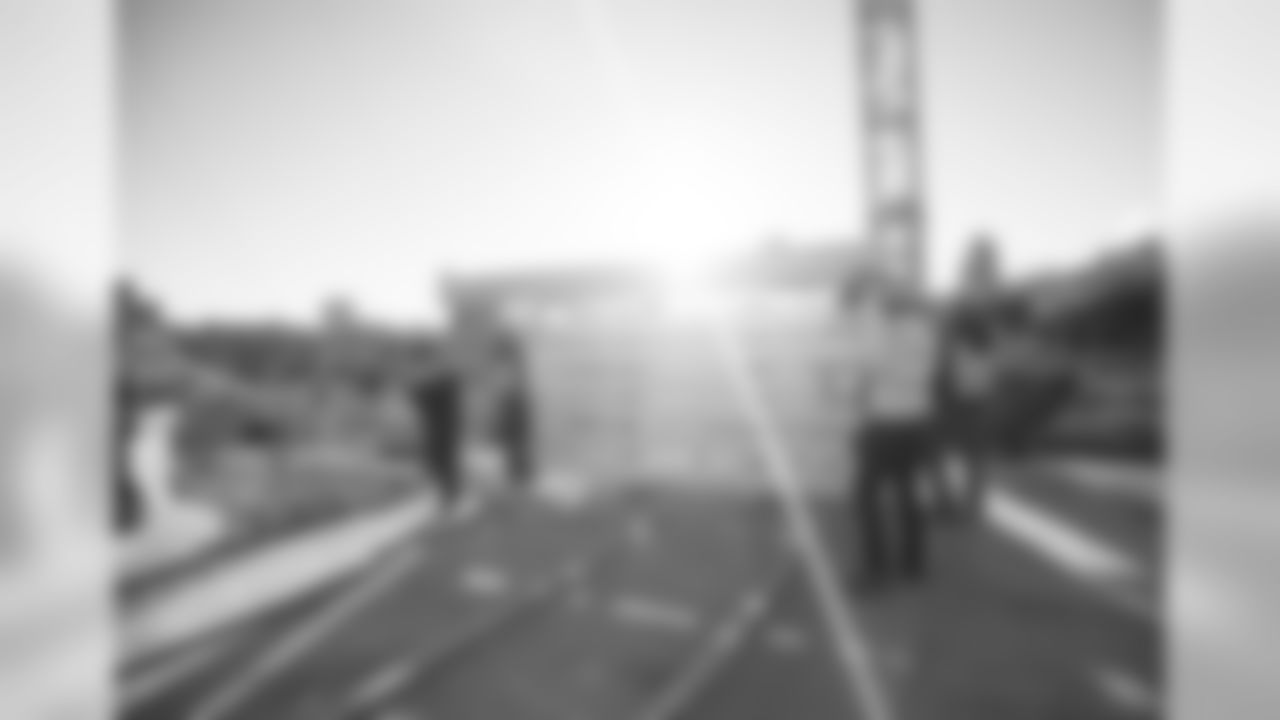
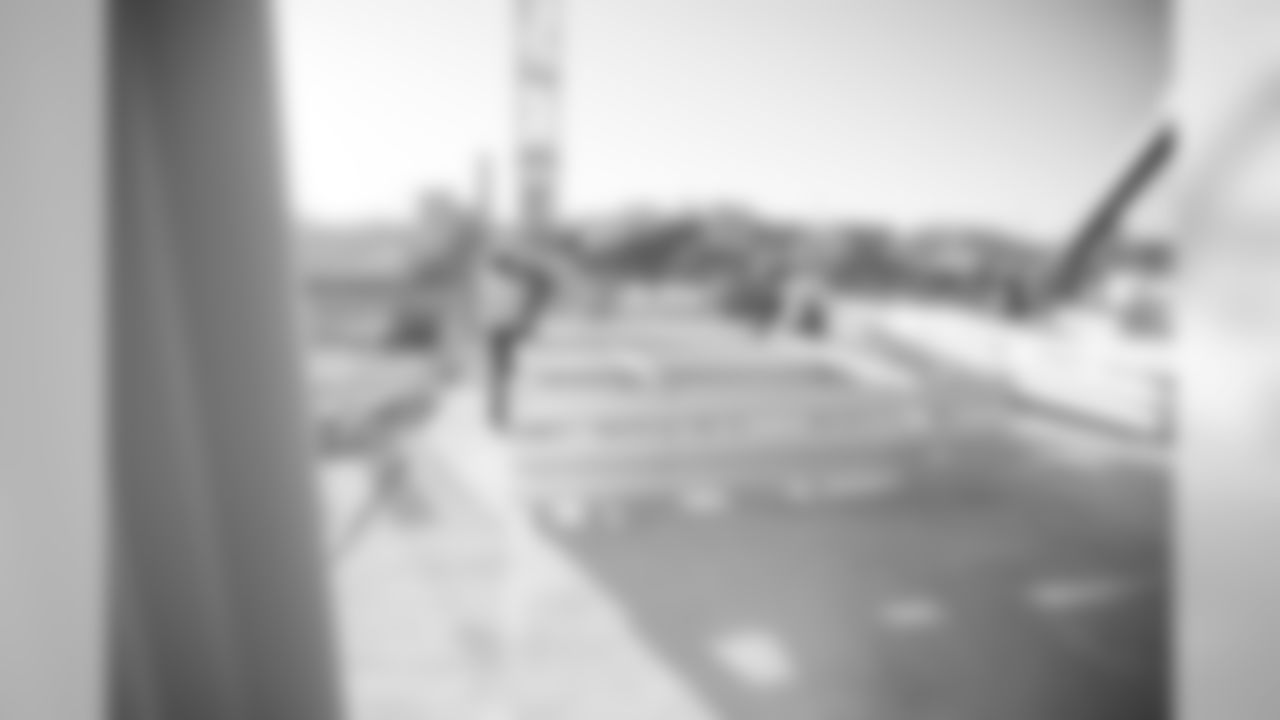
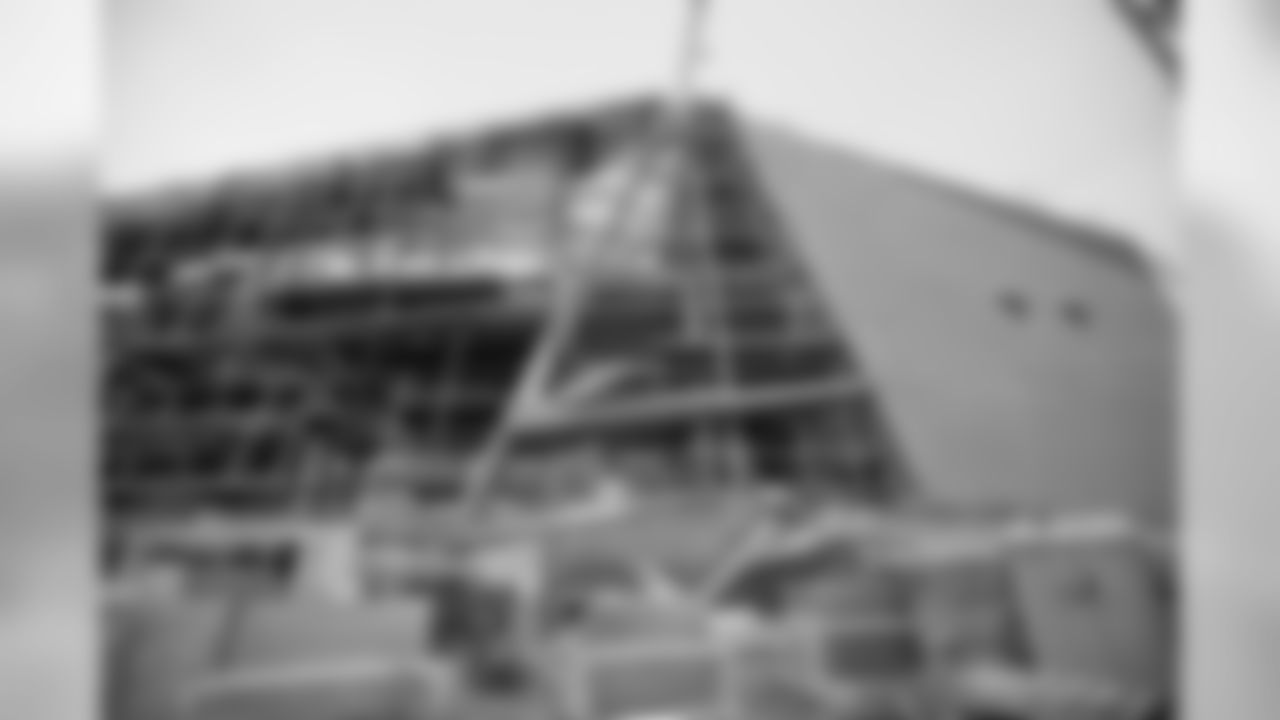
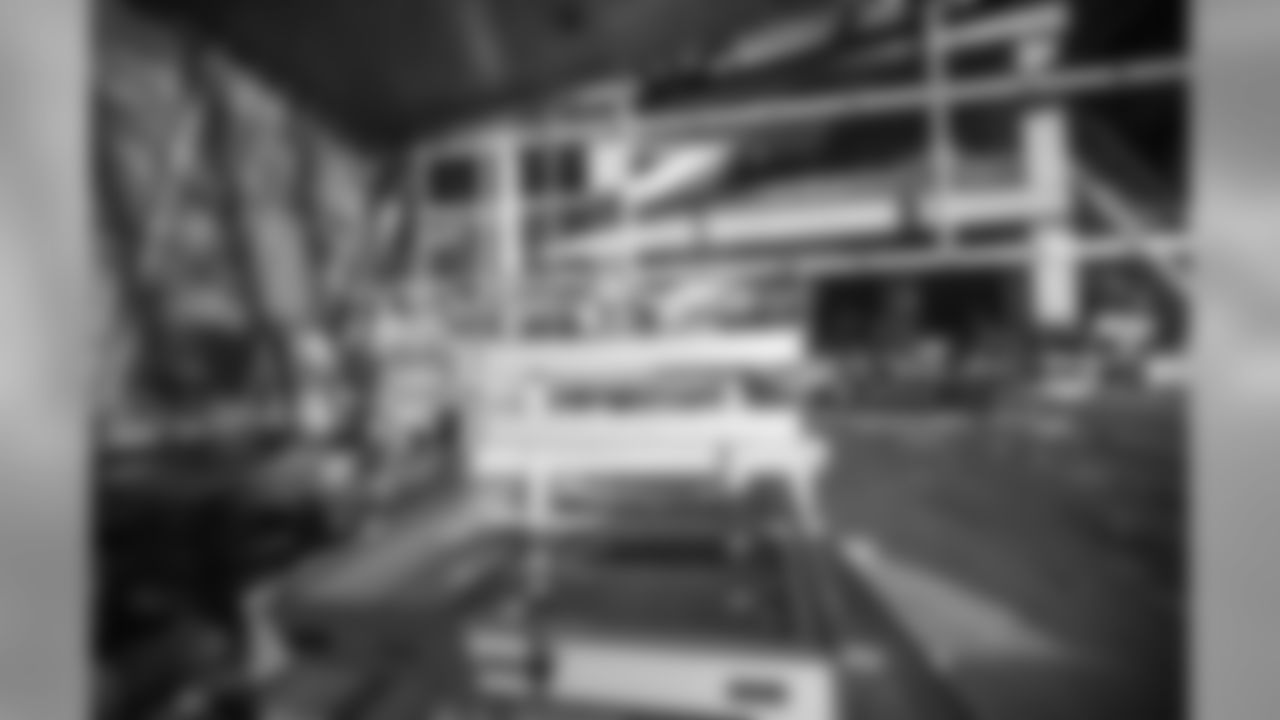

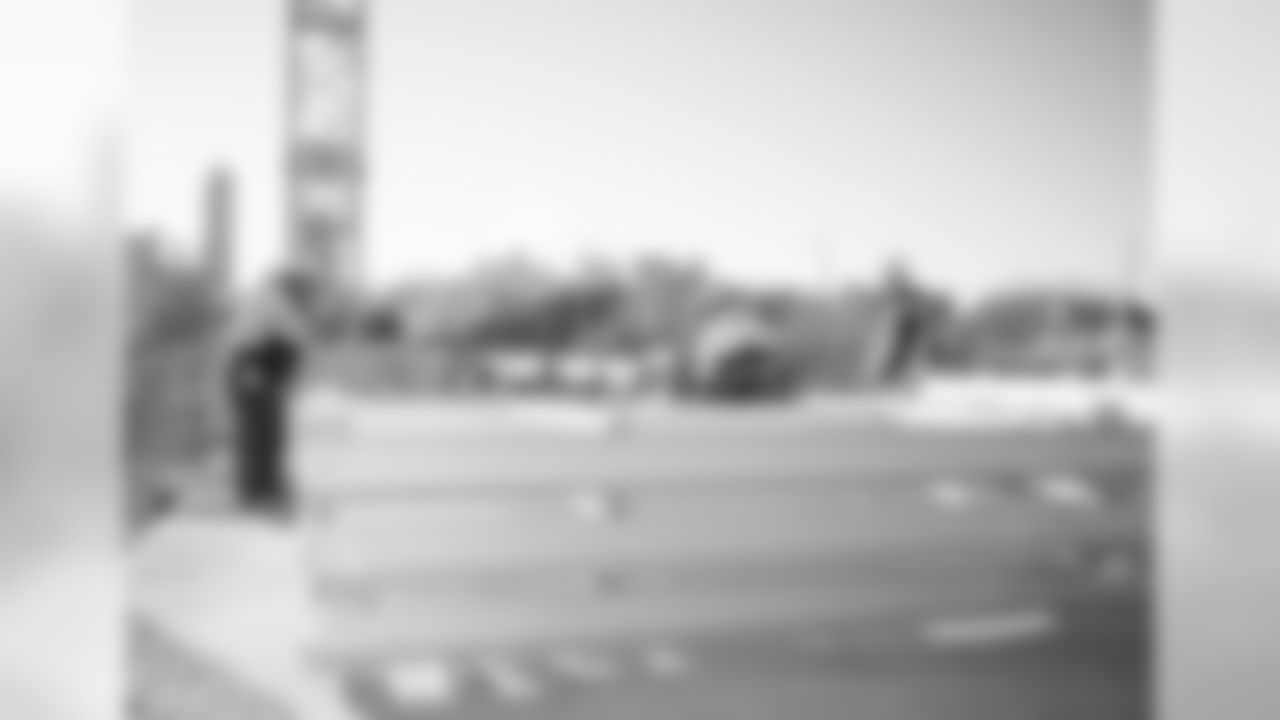
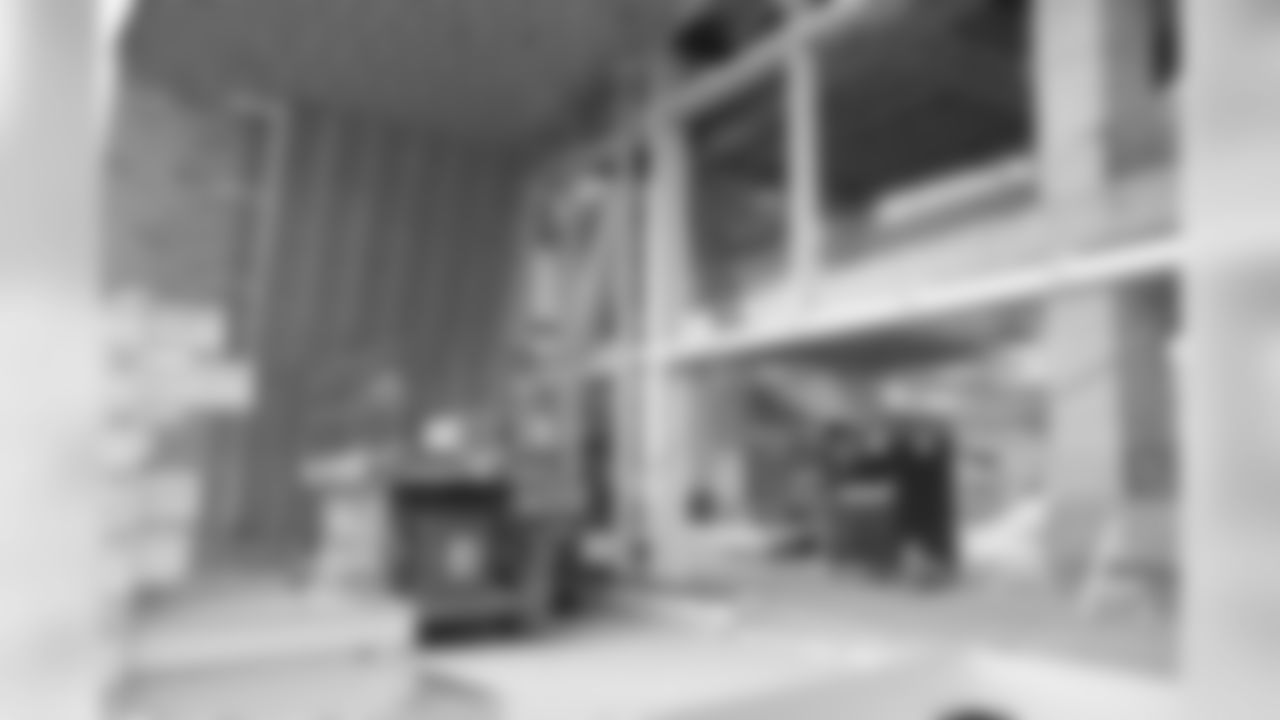
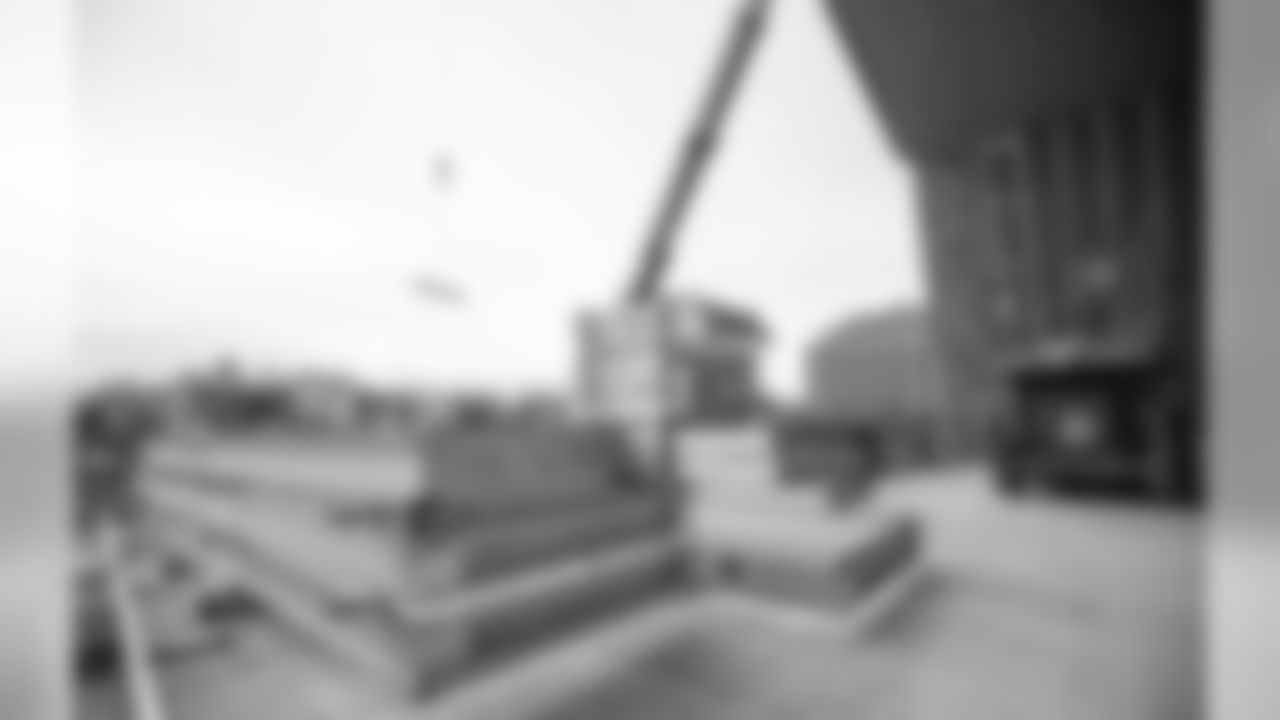
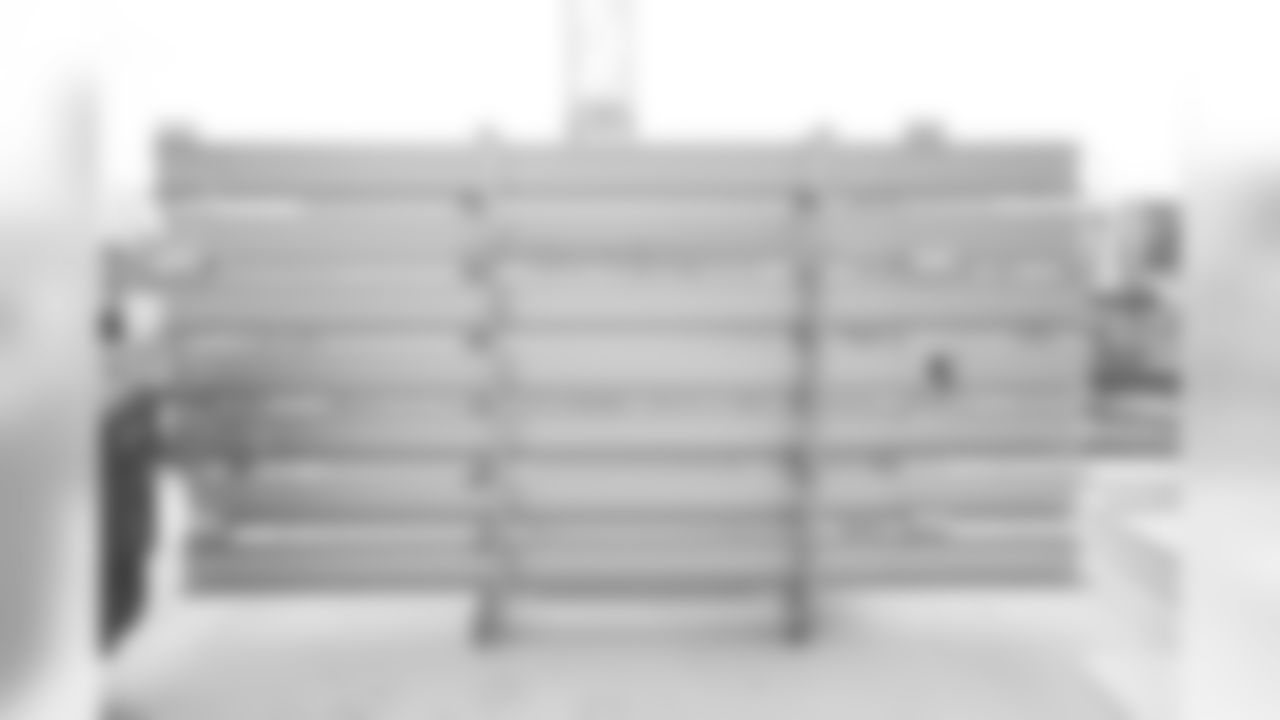
On the factory line, workers use robotic devices with giant suction cups to grab the glass and start a quick marriage between the two plates into a unit. Cari Simonson, an Owatonna native who works as a robot operator and backup lead, said there are usually nine workers on the line that assembles the units.
The exterior piece led the interior piece through a washing machine and inspection area before a metallic frame was placed between the sheets for the primary seal. A machine then injected silicon around the edges between the plates of glass. Workers at the other end of the line used another robot with suction cups to hoist the unit and inspect the matrimony with a flashlight and putty knives to fill any gaps and smooth any excesses. They then smoothly guided the unit into a wooden crate (also made at the campus) for shipping.
Viracon Director of Customer Service Seth Madole said the line can produce about 25-30 units an hour. He said most of the units used in the new stadium will be 15 to 25 square feet, and each one will weigh about 6.6 pounds per square foot. The line is capable of handling units as large as 96 by 165 inches, and some units used in the Freedom Tower measured 60 by 160 inches.
The factory is capable of fabricating 500,000 square feet of glass each week, meaning it could manufacture all 180,000 square feet of the new stadium's glass in two days, but will operate on a schedule that's paced in accordance with the installation plan developed by project leader Mortenson Construction and InterClad, which is fabricating the frame for the curtain wall system at its Plymouth location and installing the glass with a crew of about 30 workers on site at the stadium.
CHECK OUT THE GEOMETRY
Viracon has supplied glass to the Xcel Energy Center in St. Paul and TCF Bank Stadium at the University of Minnesota, as well as NFL venues in Dallas, Indianapolis, Miami and Tampa, but the expansive use of the material for the new Vikings stadium and its application in complex geometric patterns make this project especially unique, Henson said.
"In many, many cases, it's a rectangle or a square, and in this case, there's been geometry, where we have shapes of glass with patterns, whether they are trapezoids or triangles," Henson said. "Now, you get a lot of engineers involved, get a lot of draftsmen and people involved. Cutting glass and fabricating it to a specific dimension just multiplies in complexity because you've added the shapes and geometry to it, so while it would be exciting, it's also a bit nerve-racking.
"It's one thing to cut a rectangle or square, and if you're a handyman or do things at home, now suddenly take that and go create a parallelogram," Henson continued. "It compounds the complexity that much more, but when it's finished, you can look at it and see, a historical building to us is multiple stories, every piece of glass is about the same size, in this case, not so much, there's so many different sizes that are being designed and probably the end user or consumer will never really be able to comprehend all that engineering and complexity that went into that."
InterClad Senior Project Manager Deb Linquist said while the complexity of the new stadium's geometry is challenging, it is also exciting. The Minnesota native has 10 years of experience with InterClad and 30 years of experience in the industry.
InterClad has been providing design assistance on the curtain wall system for Mortenson for more than a year. The curtain wall is the skin of the stadium that uses the frames that are fabricated in Plymouth for the Viracon glass units.
The aluminum and glass wall system is designed to keep the elements out, let in beneficial light and control solar energy and temperature. Linquist said a mock-up was shipped to a special facility in Pennsylvania to test the design and construction against elements like wind and water.
Other marquee projects InterClad worked on include the Target Field and Target's Northern Campus corporate facilities in Brooklyn Park.
Linquist said the new Vikings stadium is one of the largest in terms of the contract value and one of historical significance to the region in which she and InterClad are proud to participate.
Henson concurred, saying the construction of the new Vikings stadium is a "really special occasion." Viracon has completed about 50 percent of the units for the stadium, which is about 45 percent complete.
"Emotionally speaking, for our community to be a part of a job that's going to forever change the skyline of Minneapolis is fantastic," Henson said. "The efforts and work of employees that will touch this glass that will then be placed in a truck and delivered up to Minneapolis and placed on a stadium that they can say 'I was a part of that,' is really important for us and our community."