The ribbon board install began recently at U.S. Bank Stadium.
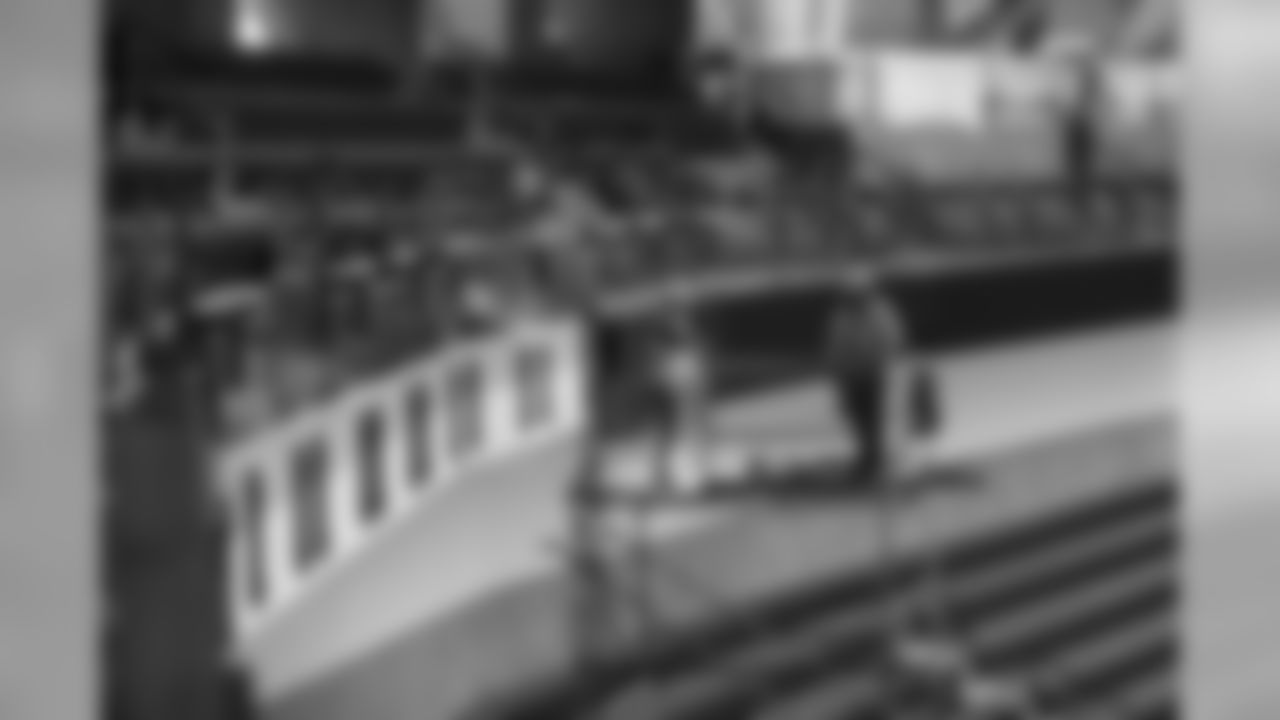
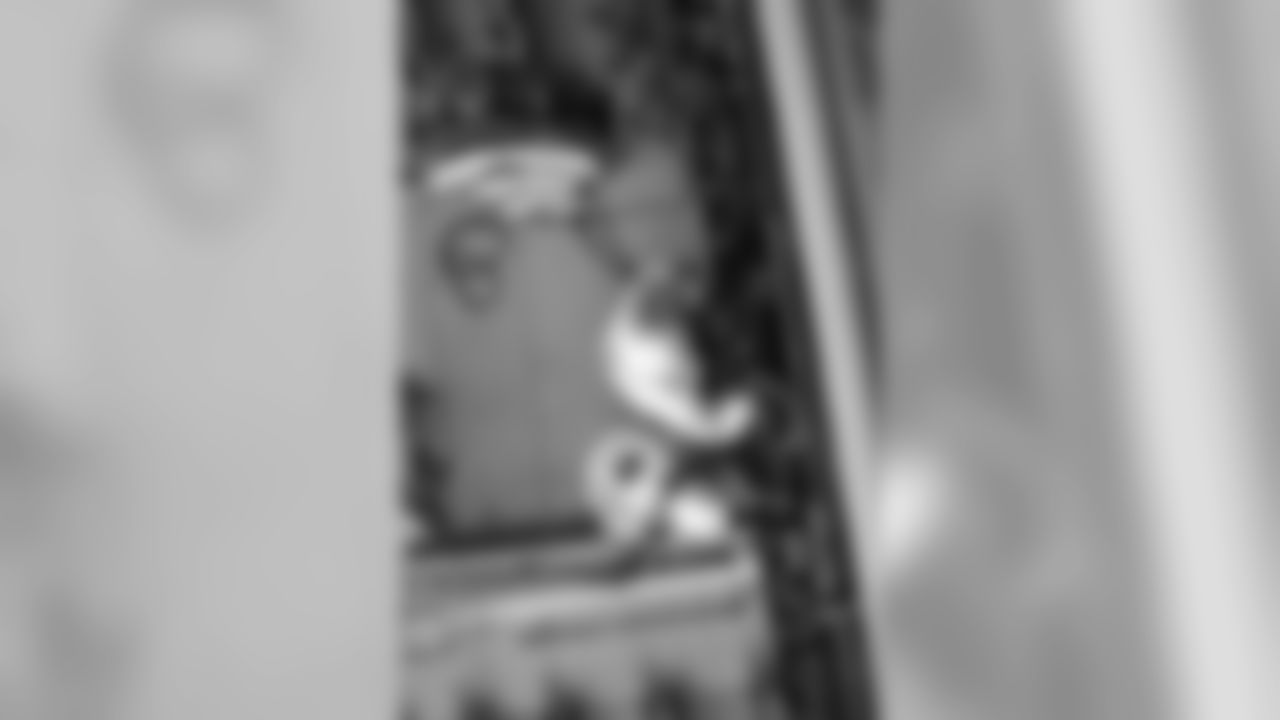

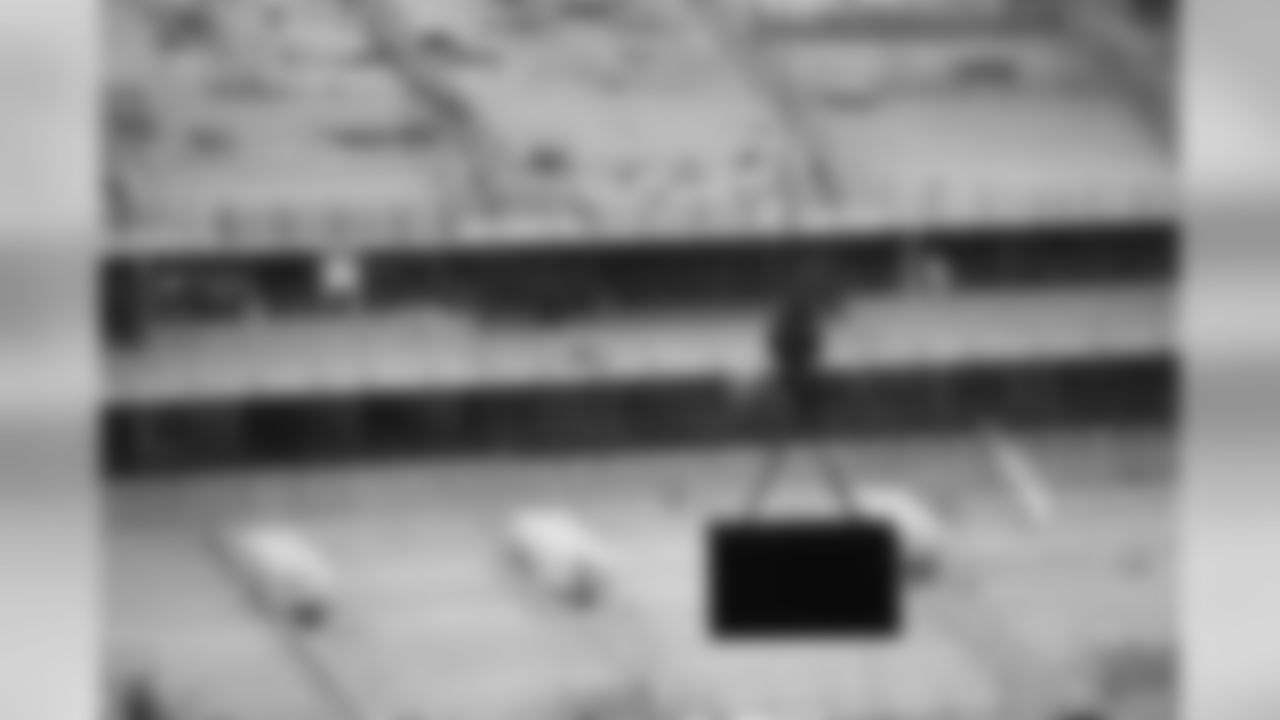
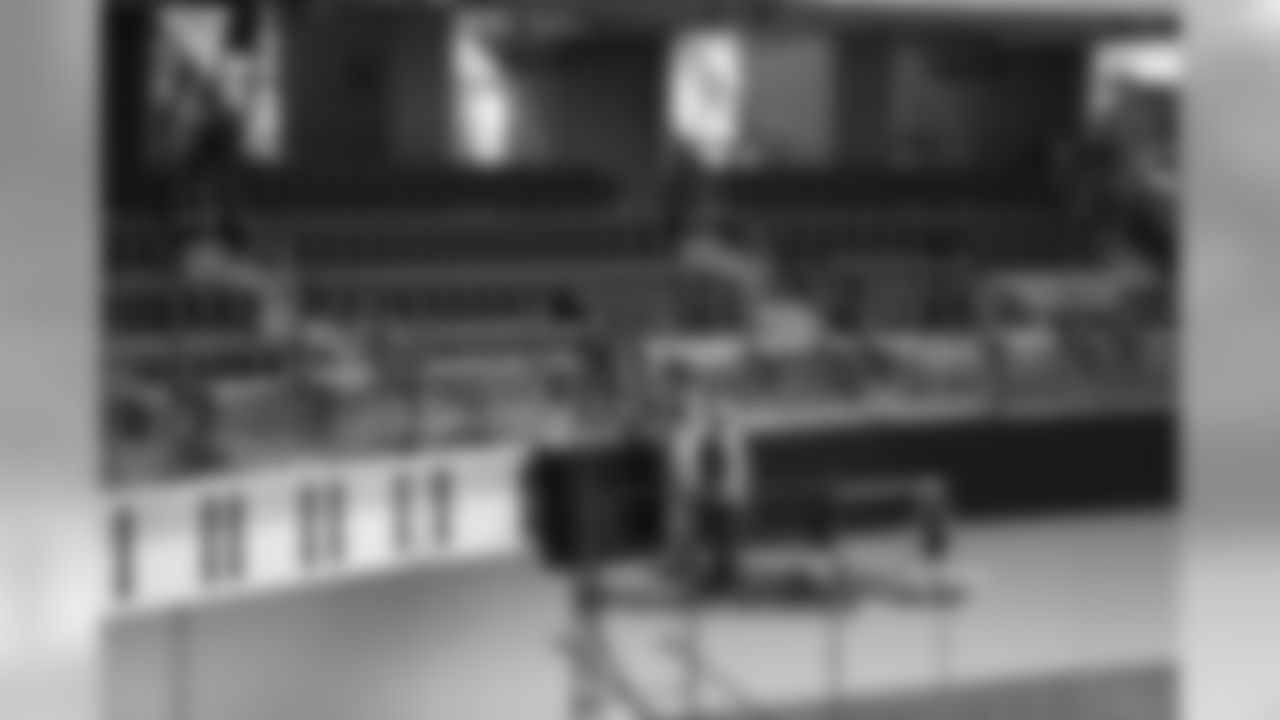
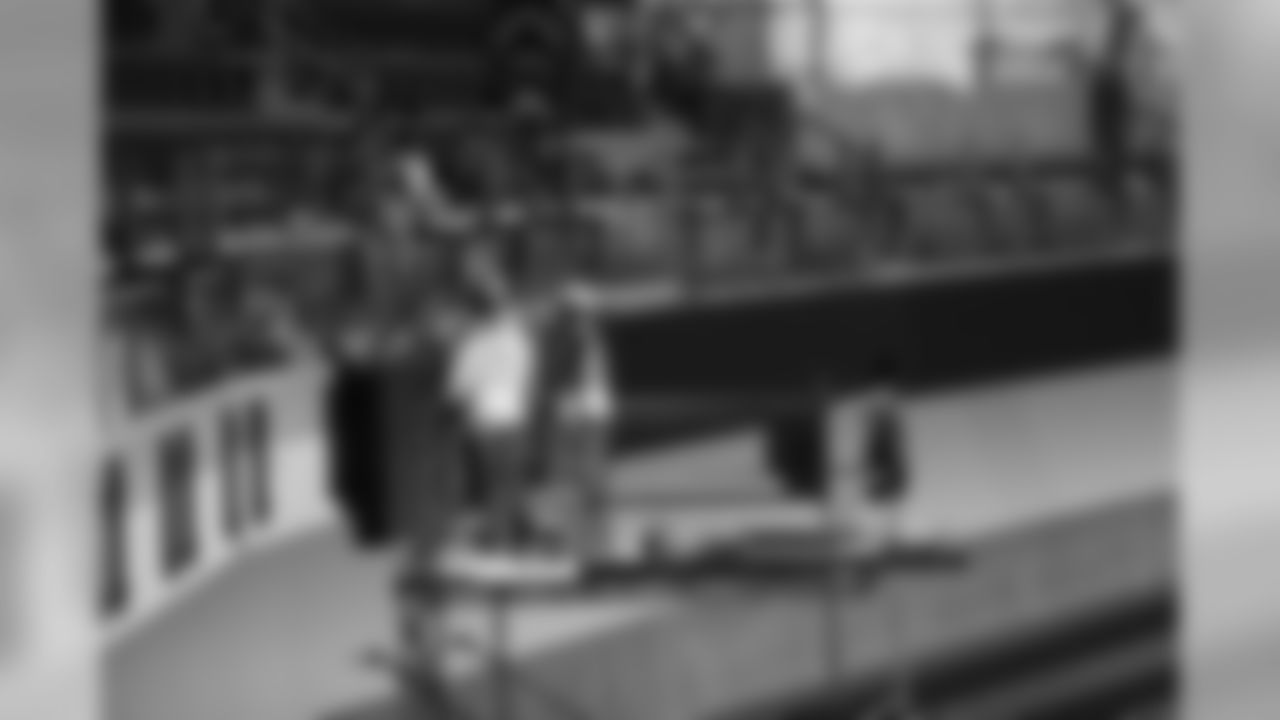

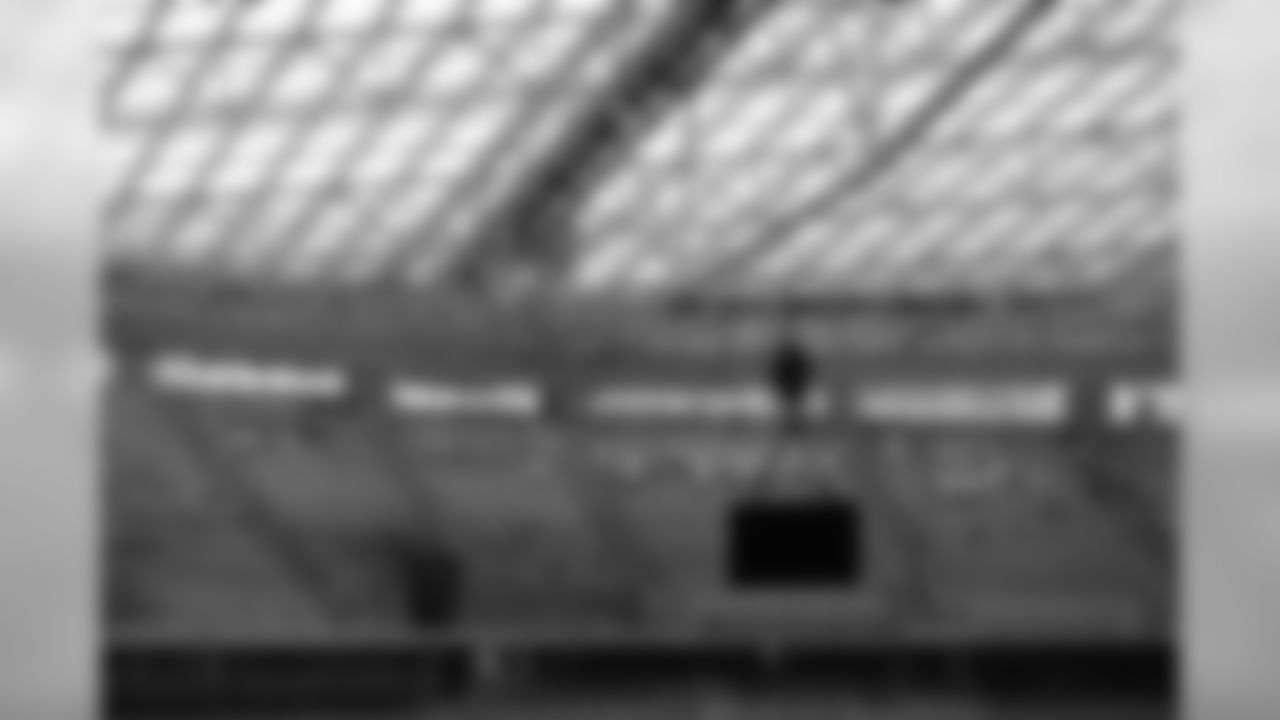
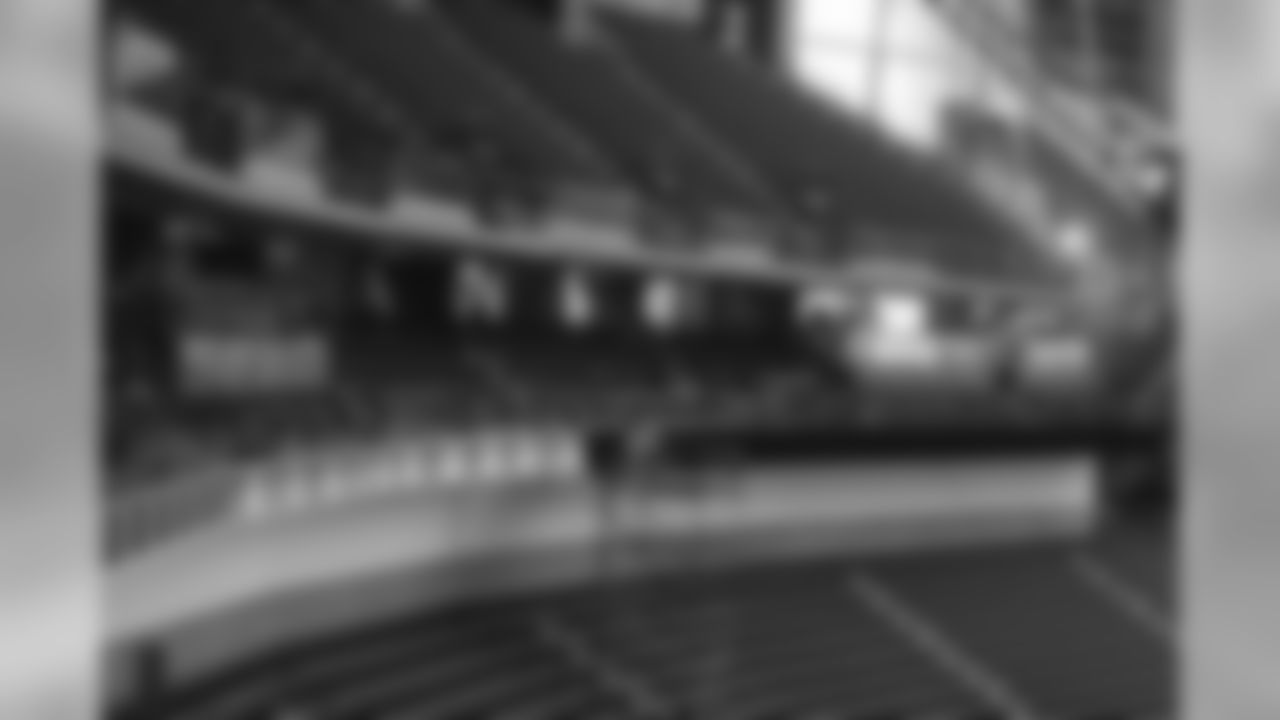
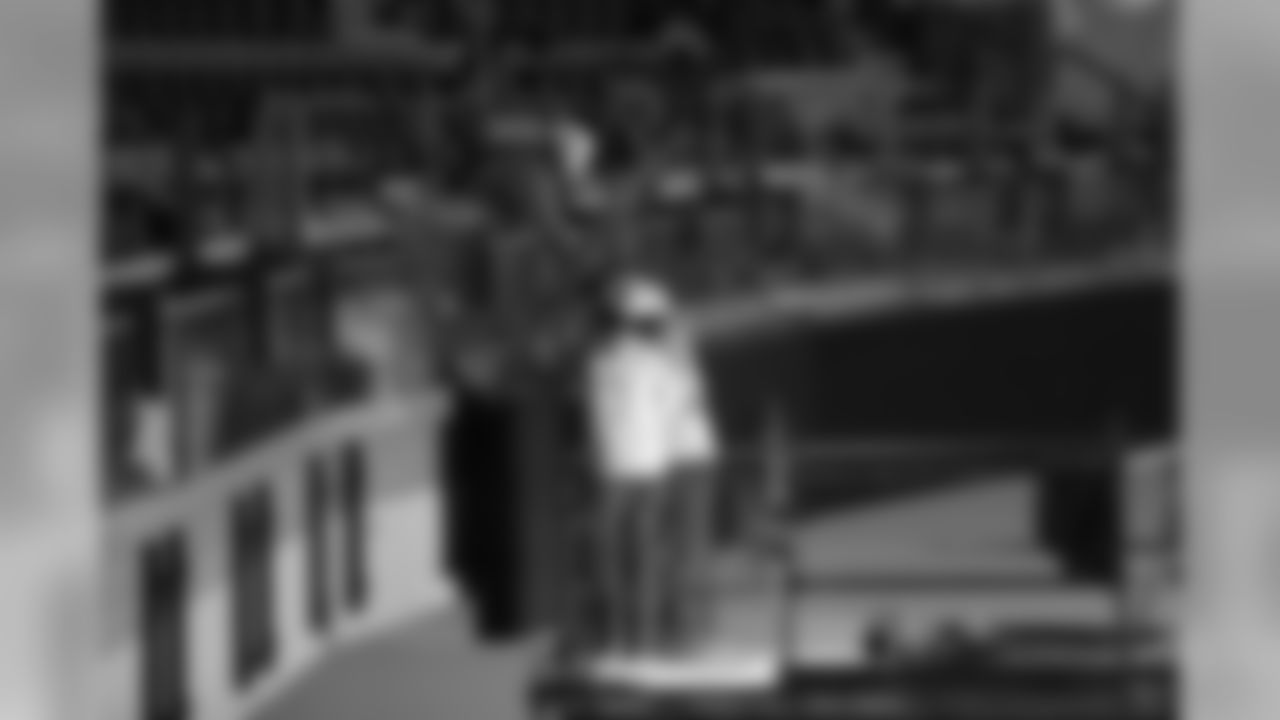
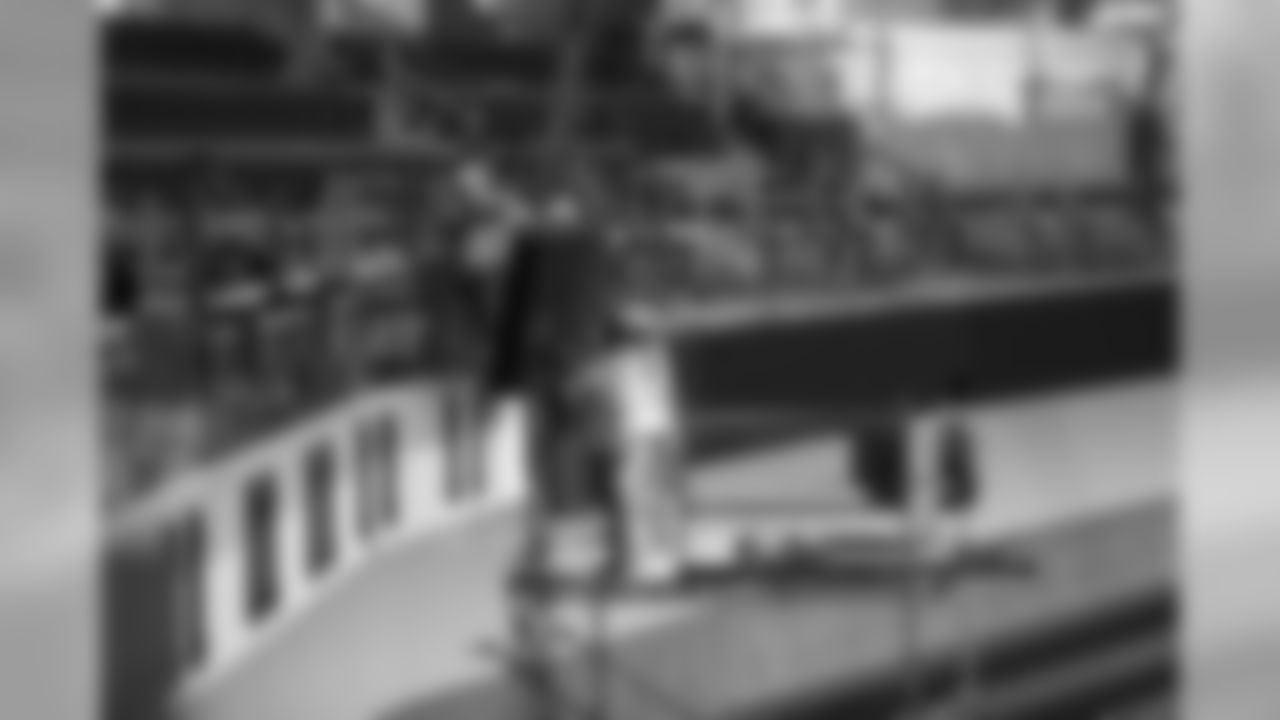
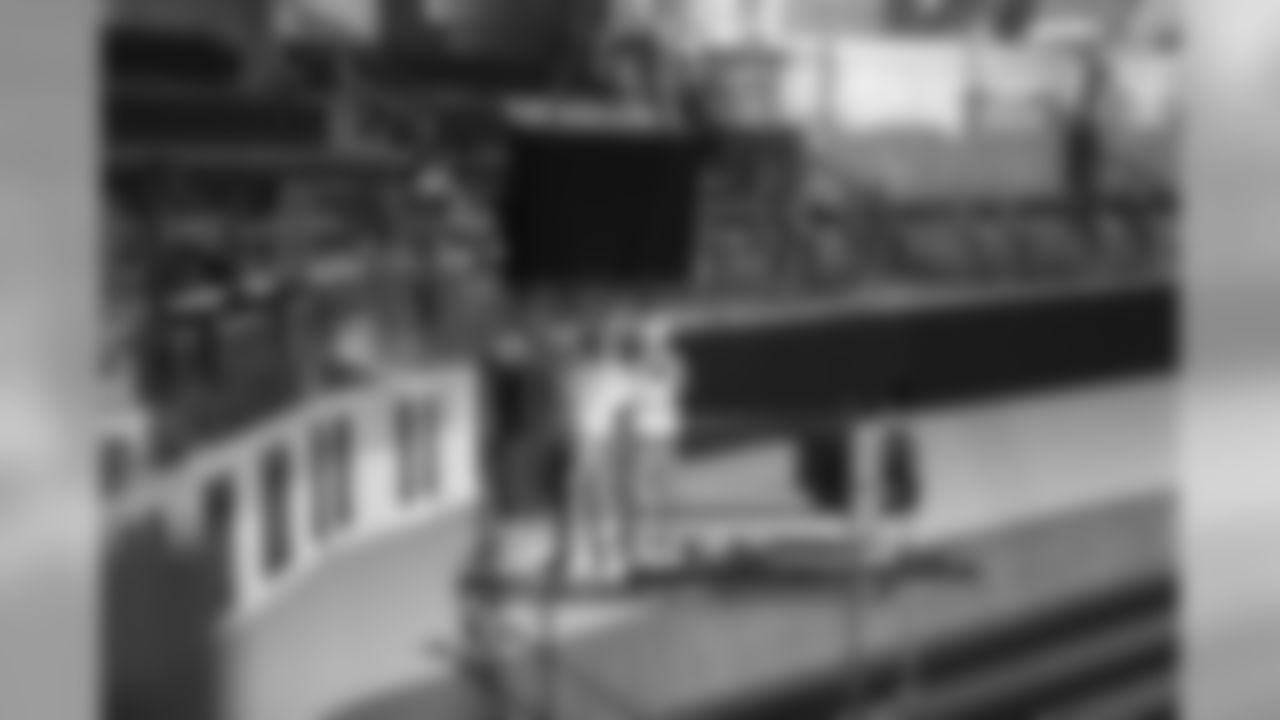
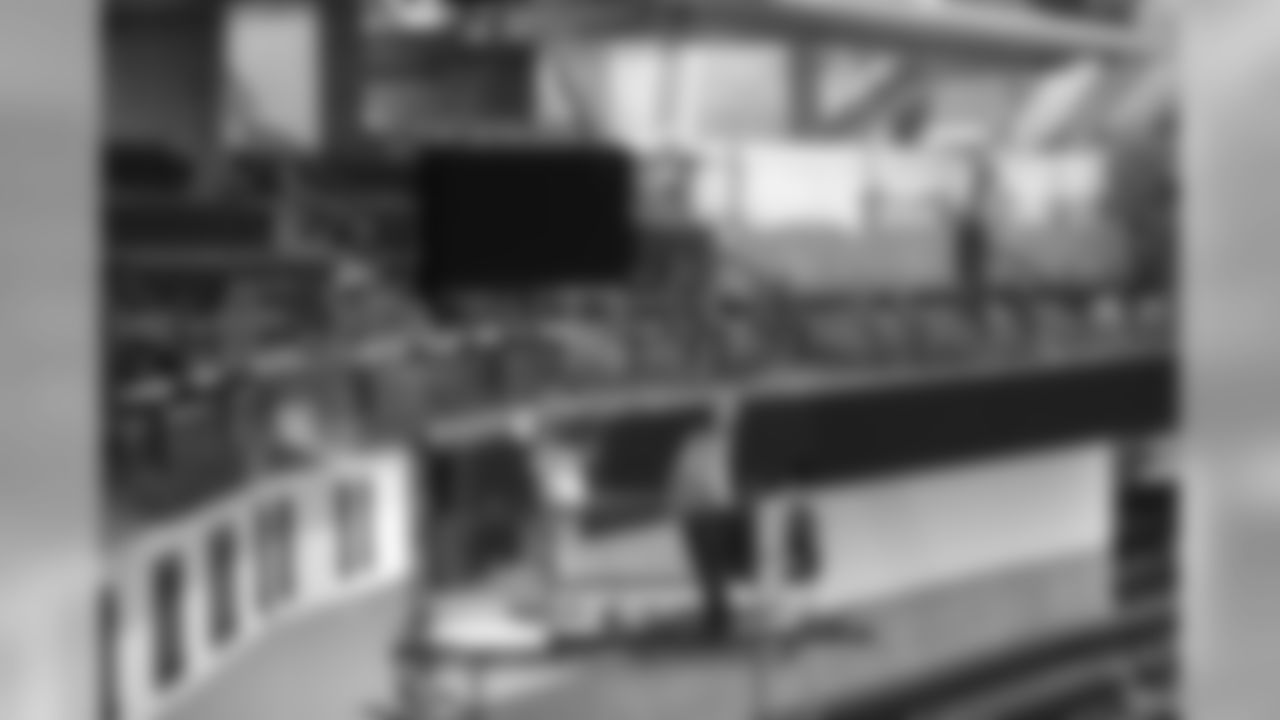
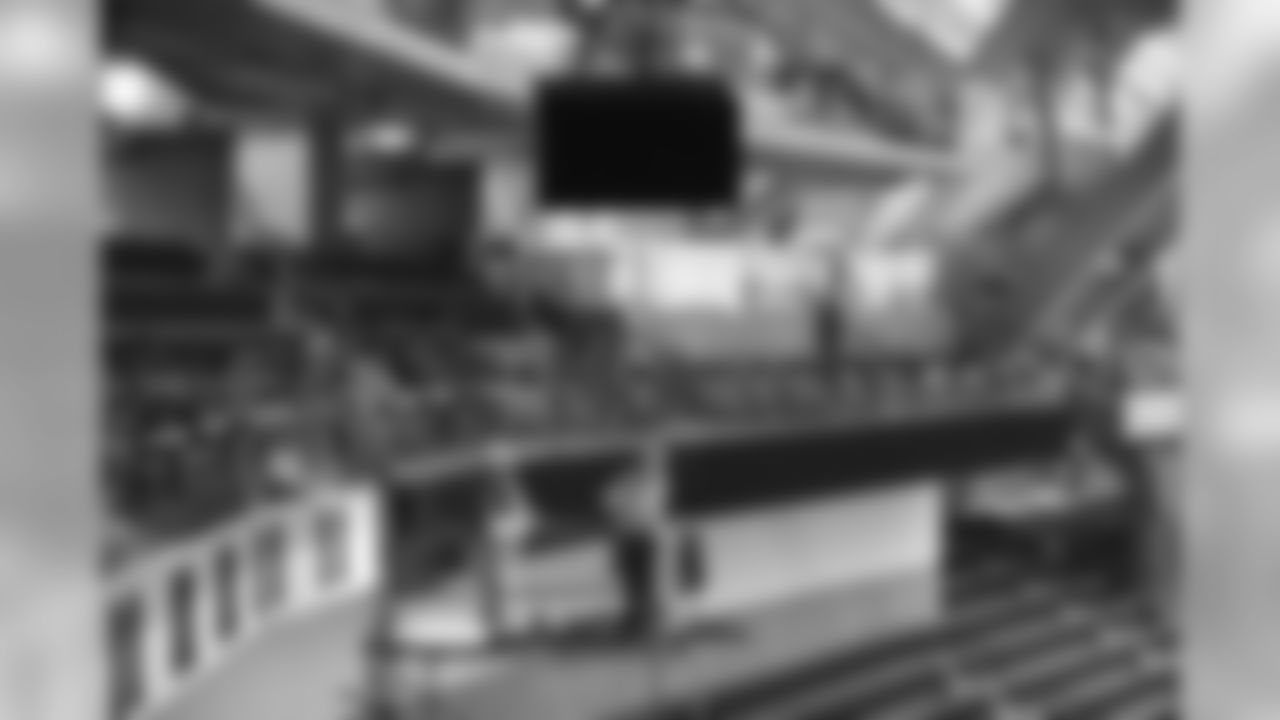
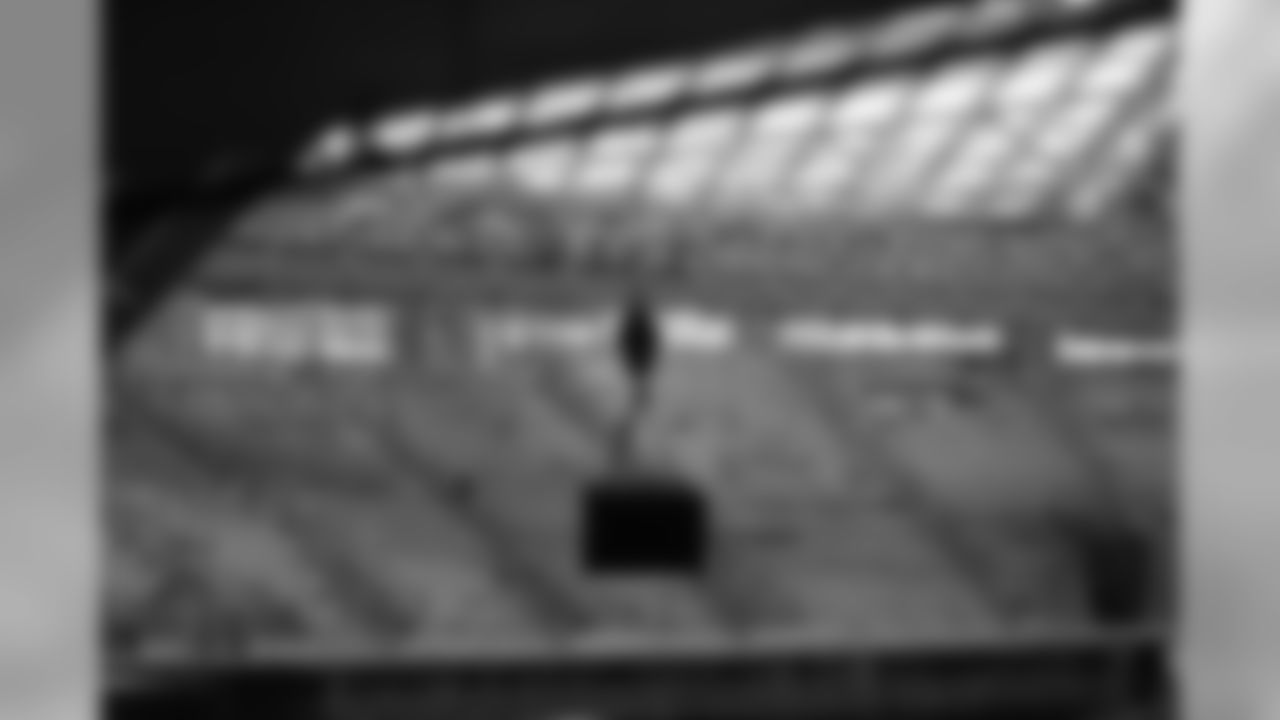
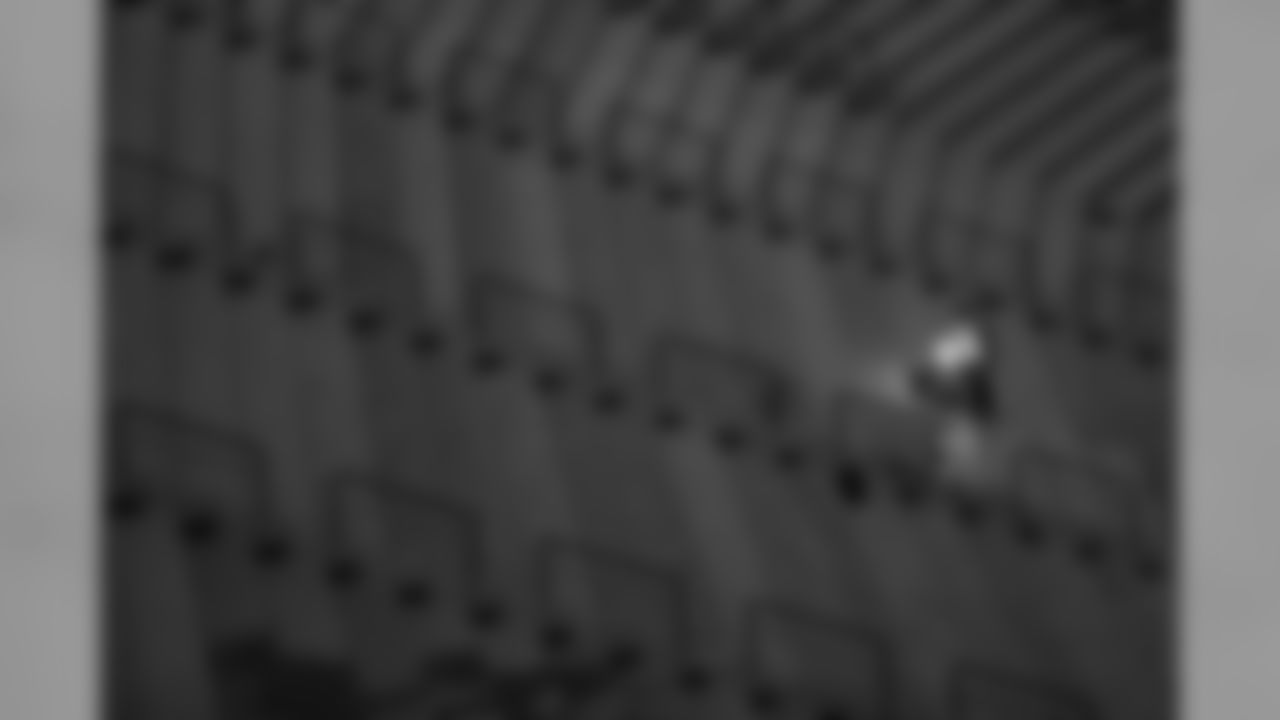
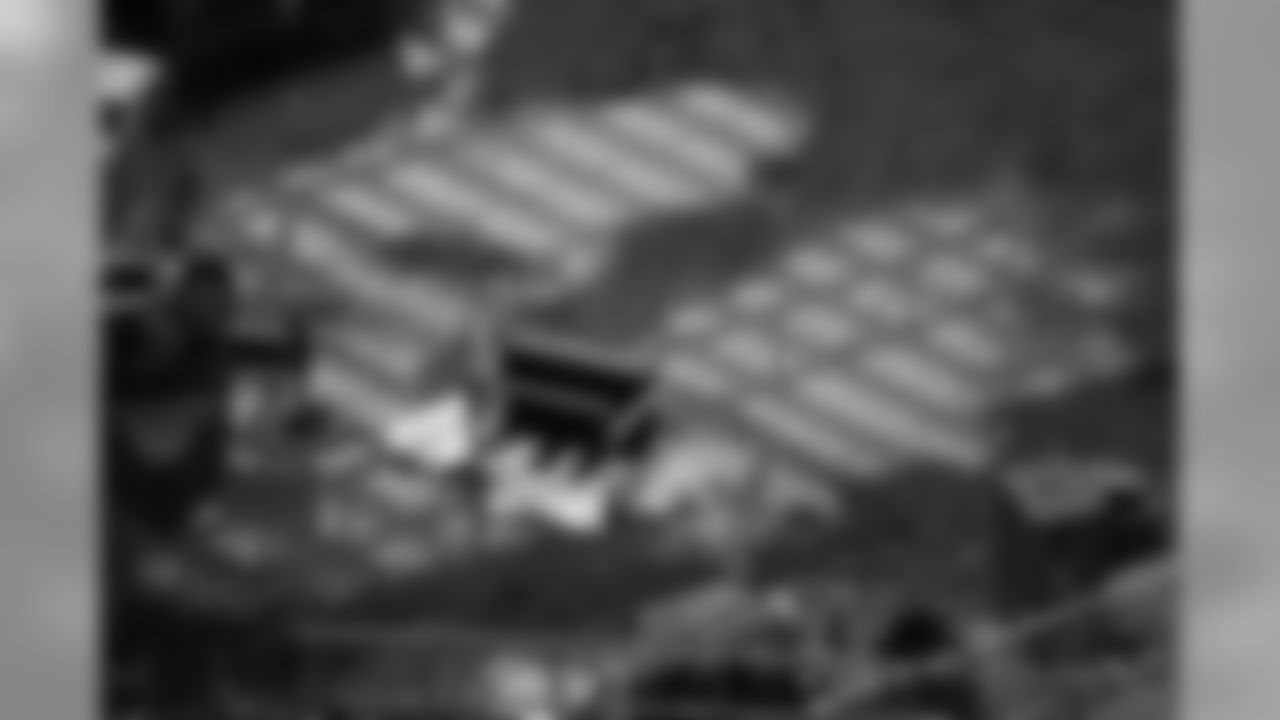
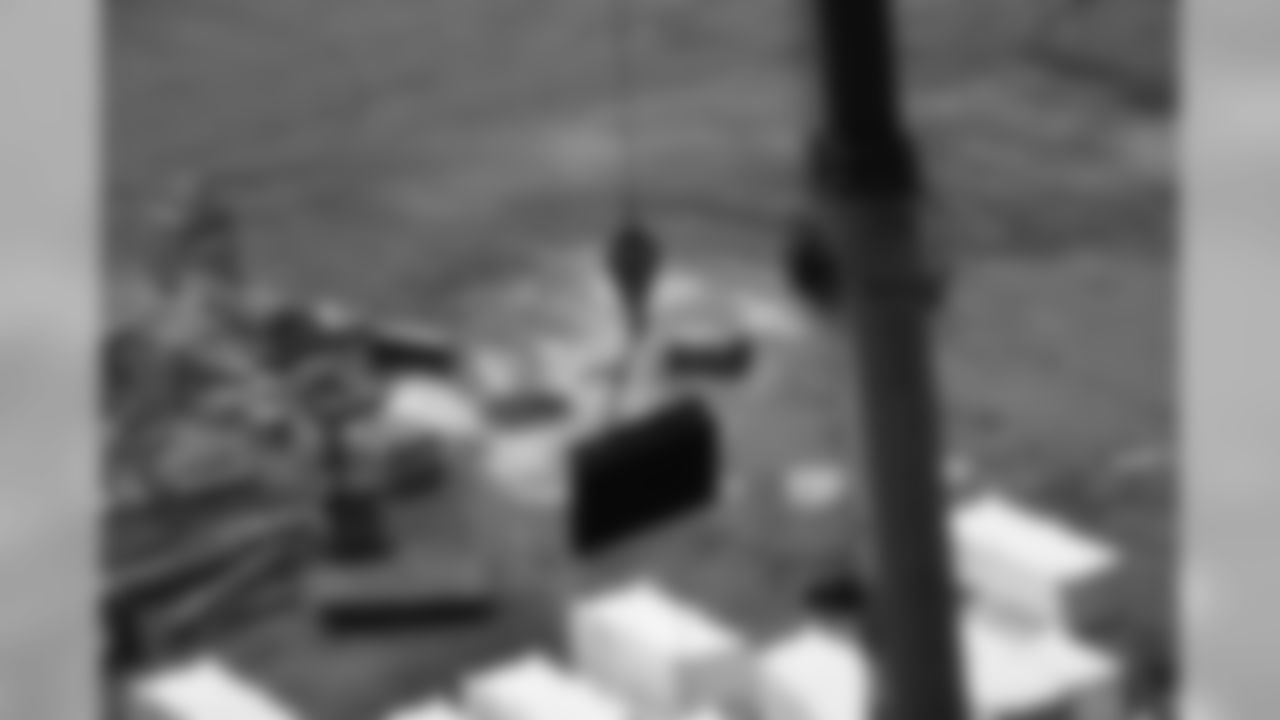
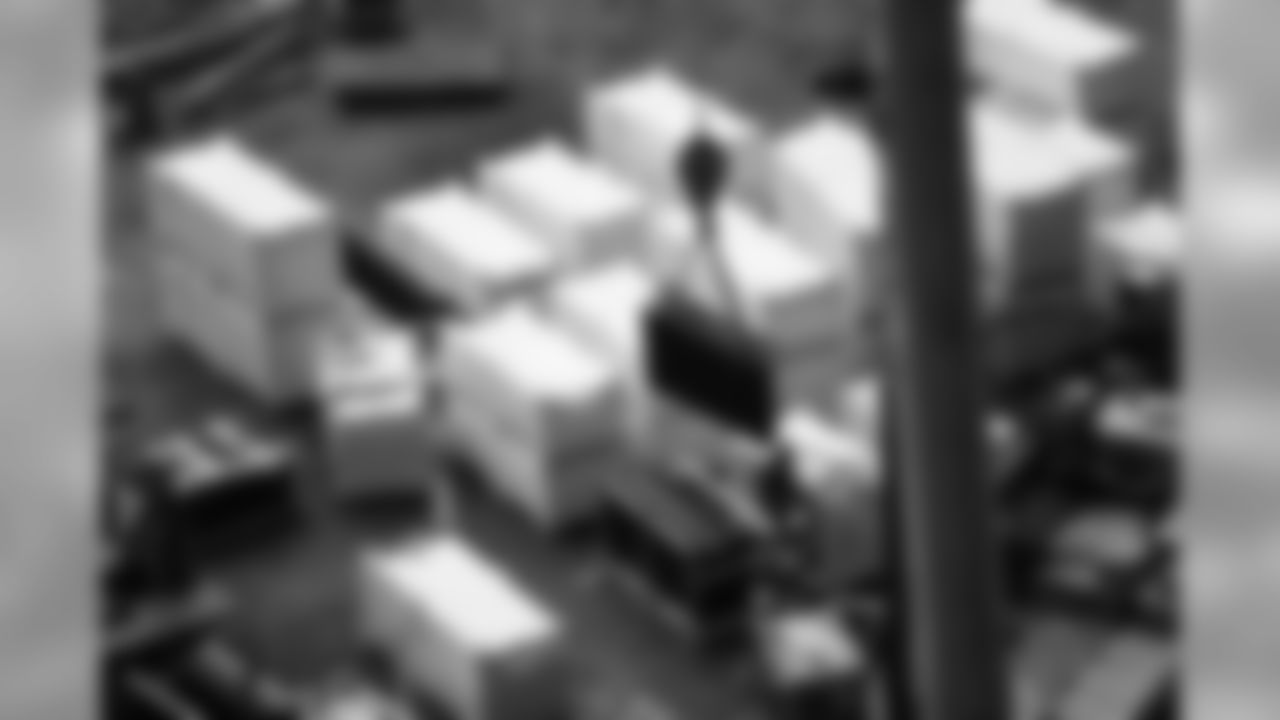
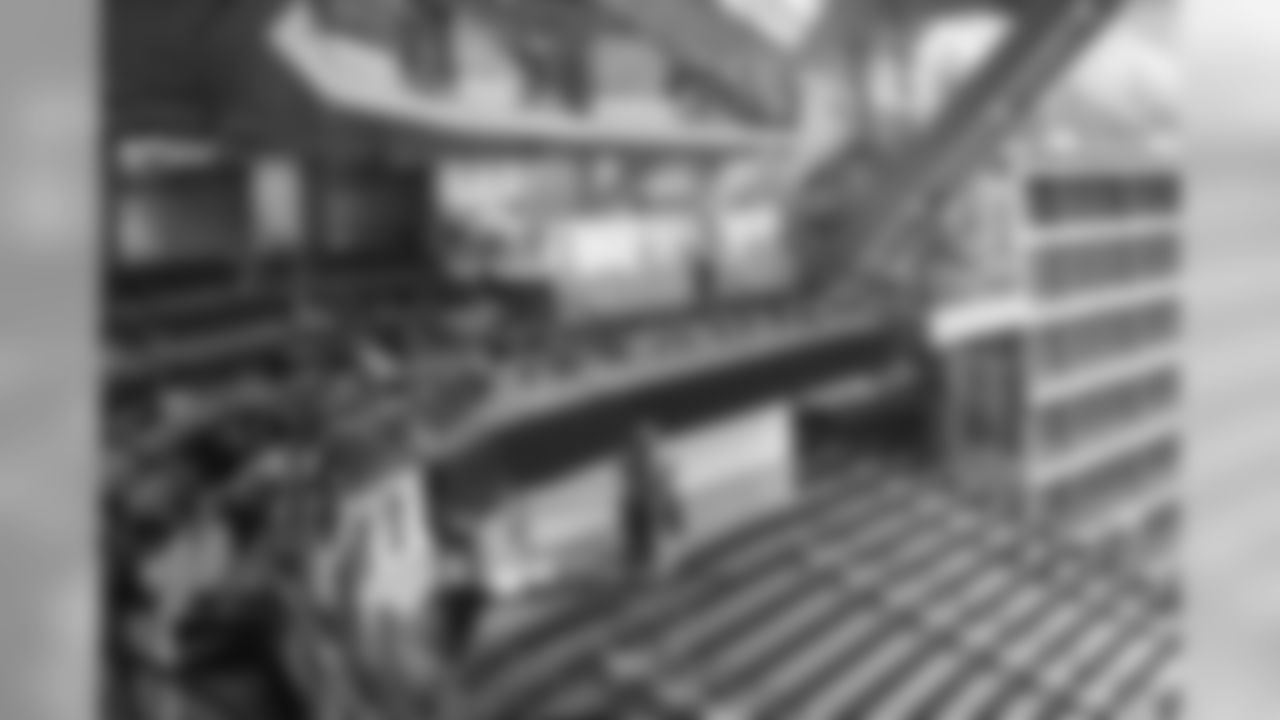
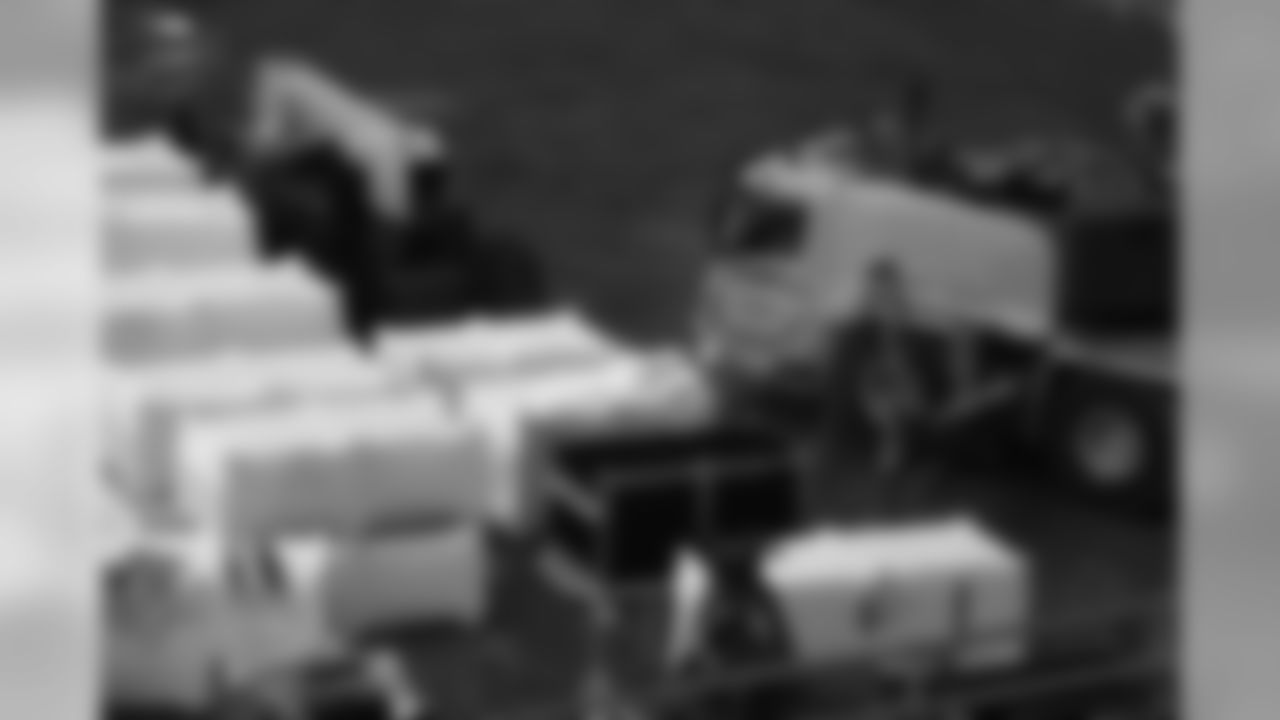
REDWOOD FALLS, Minn. — Alex Ohm has outgrown his Vikings Warren Moon jersey.
The youth medium No. 1 still hangs above his desk, a reminder of a time when the Vikings put quite a few points on the scoreboard and captured the attention of the lifelong fan.
The east endzone scoreboard for U.S. Bank Stadium was delivered on Wednesday, Nov. 25 in advance of the upcoming install.
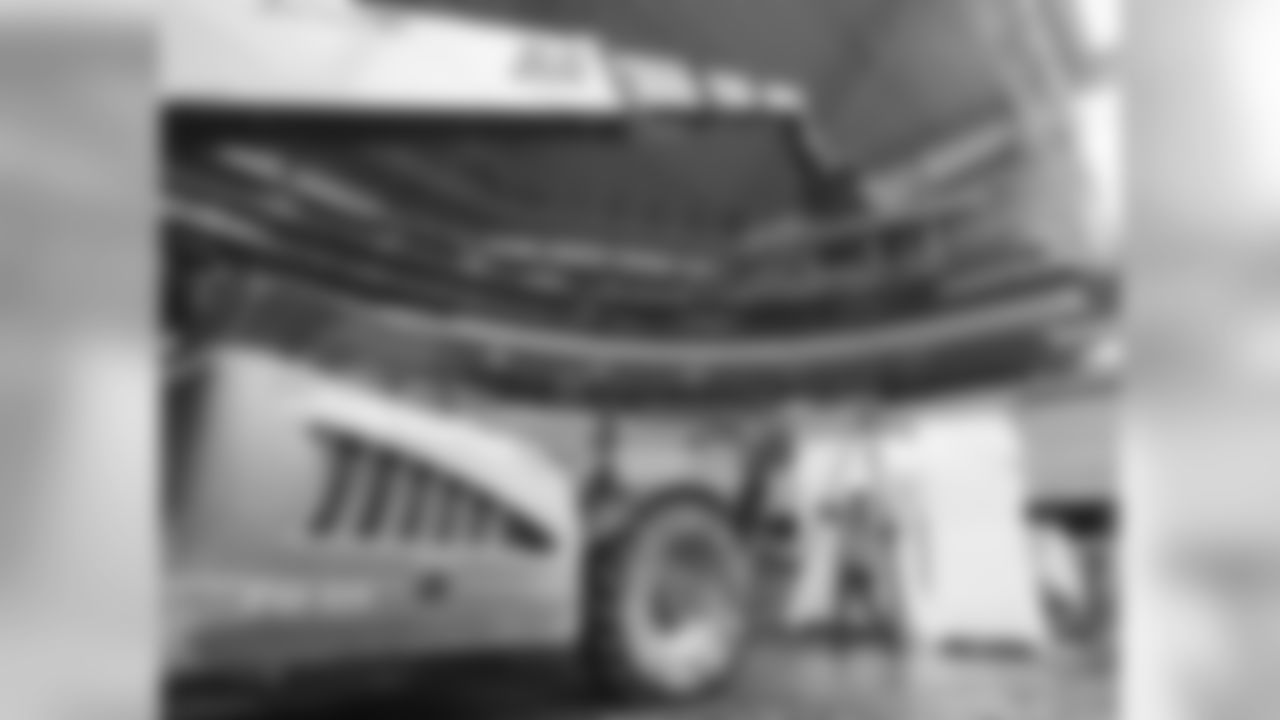
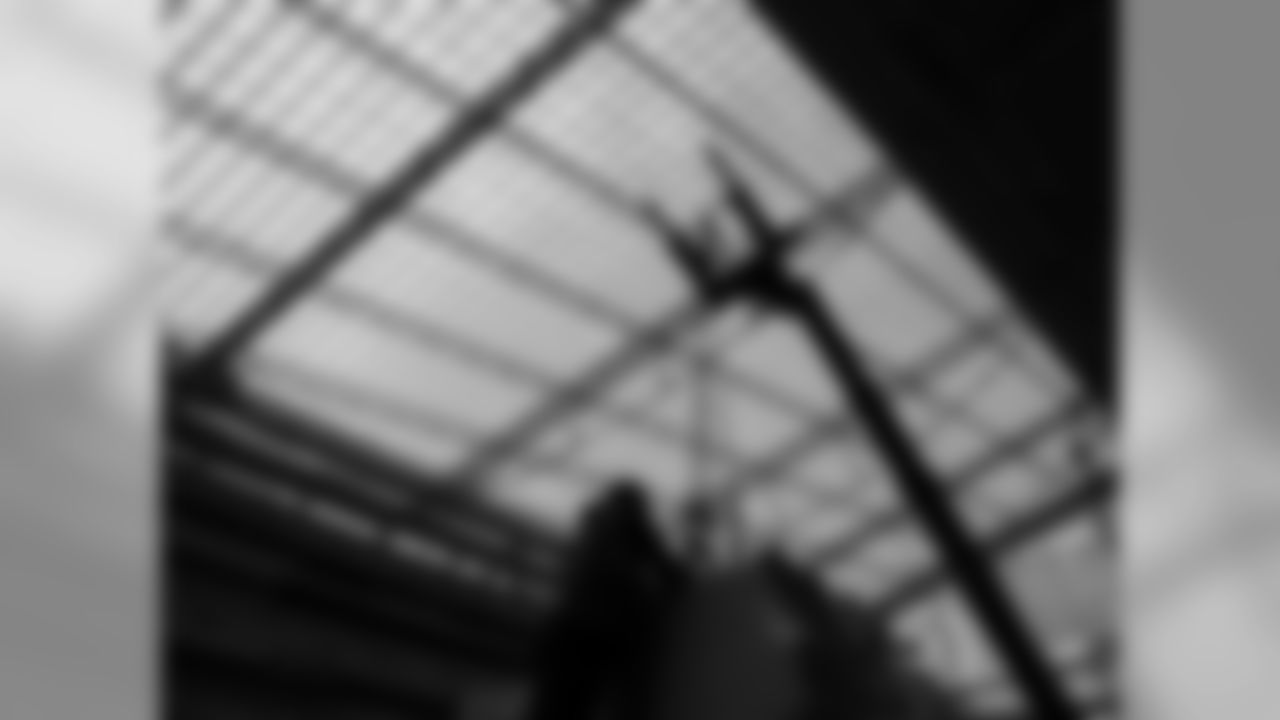
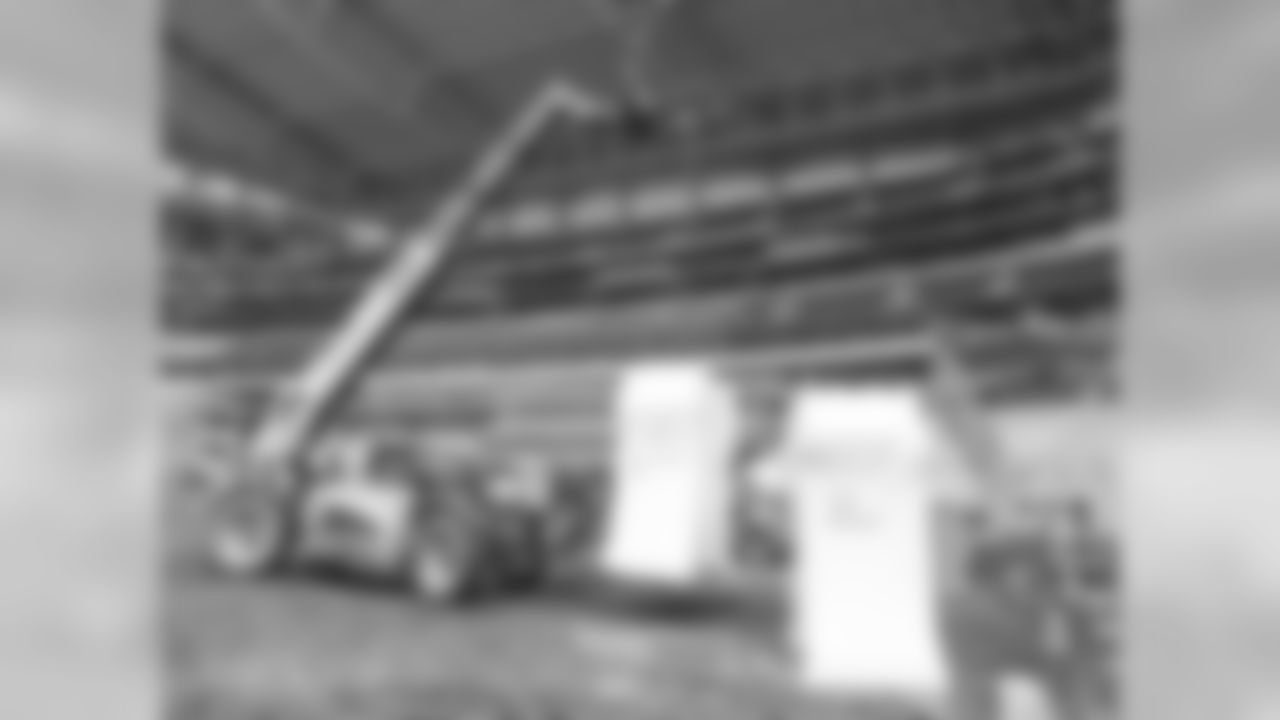
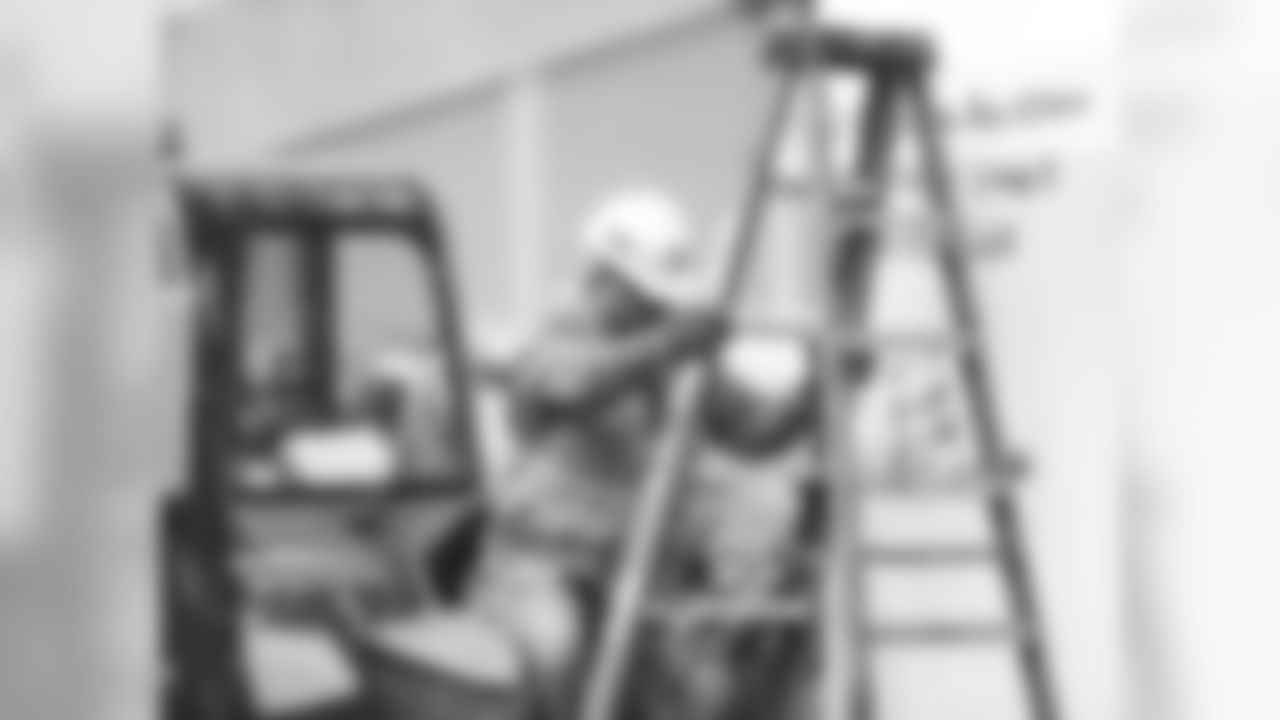
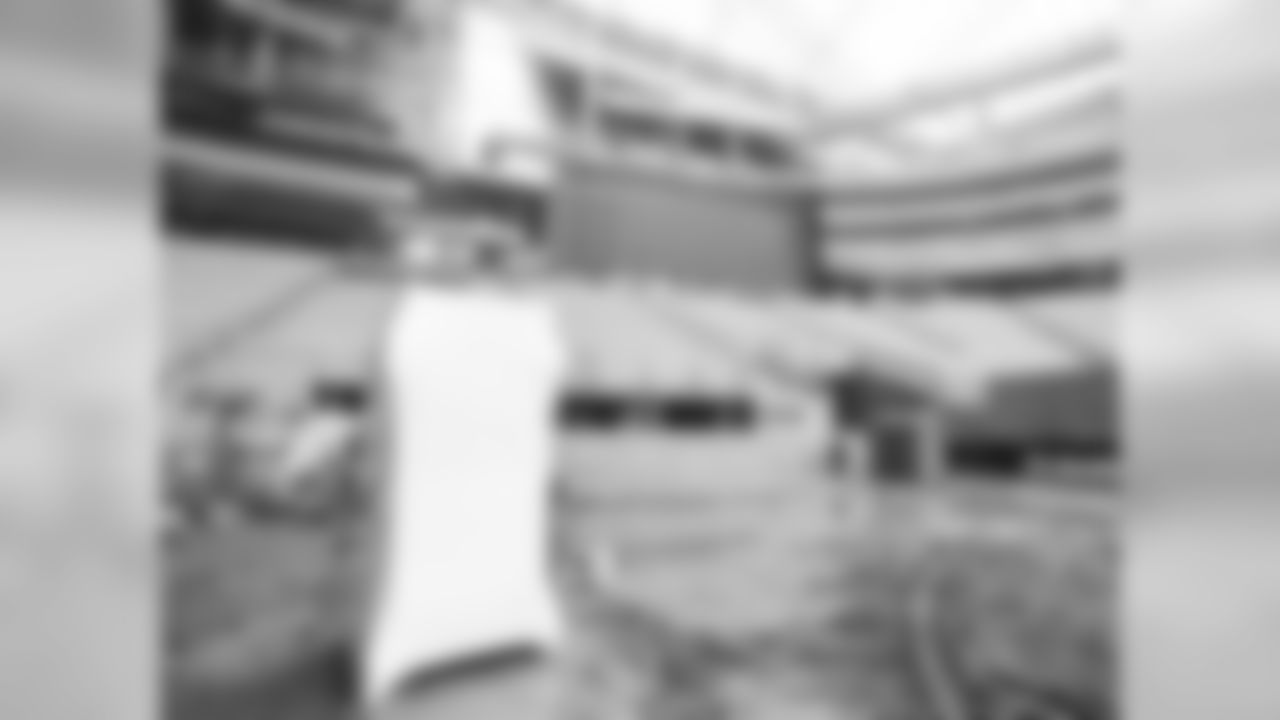
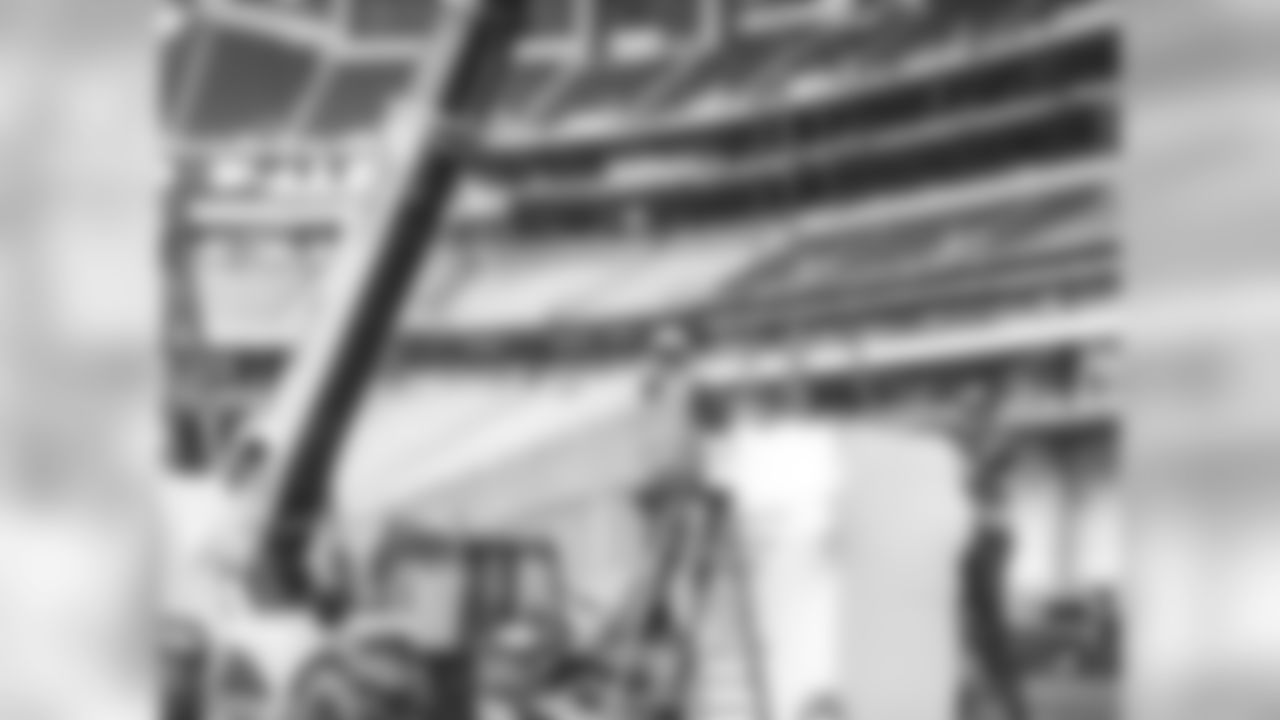
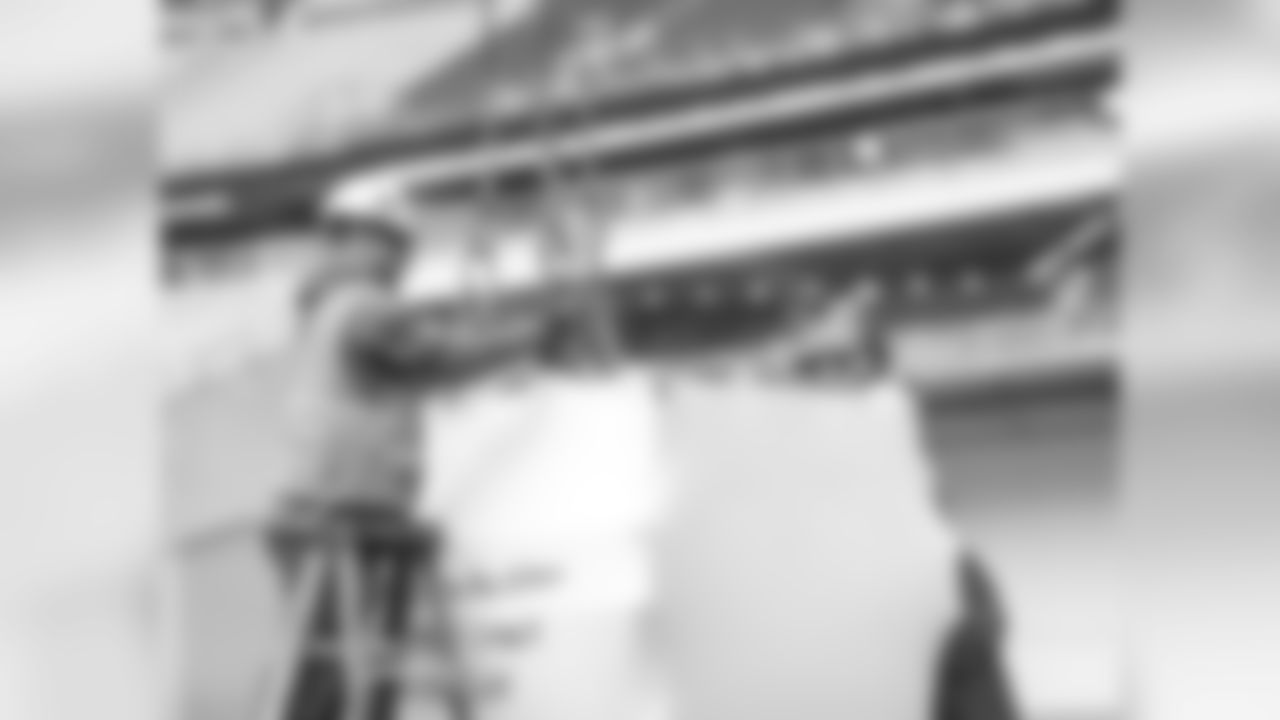
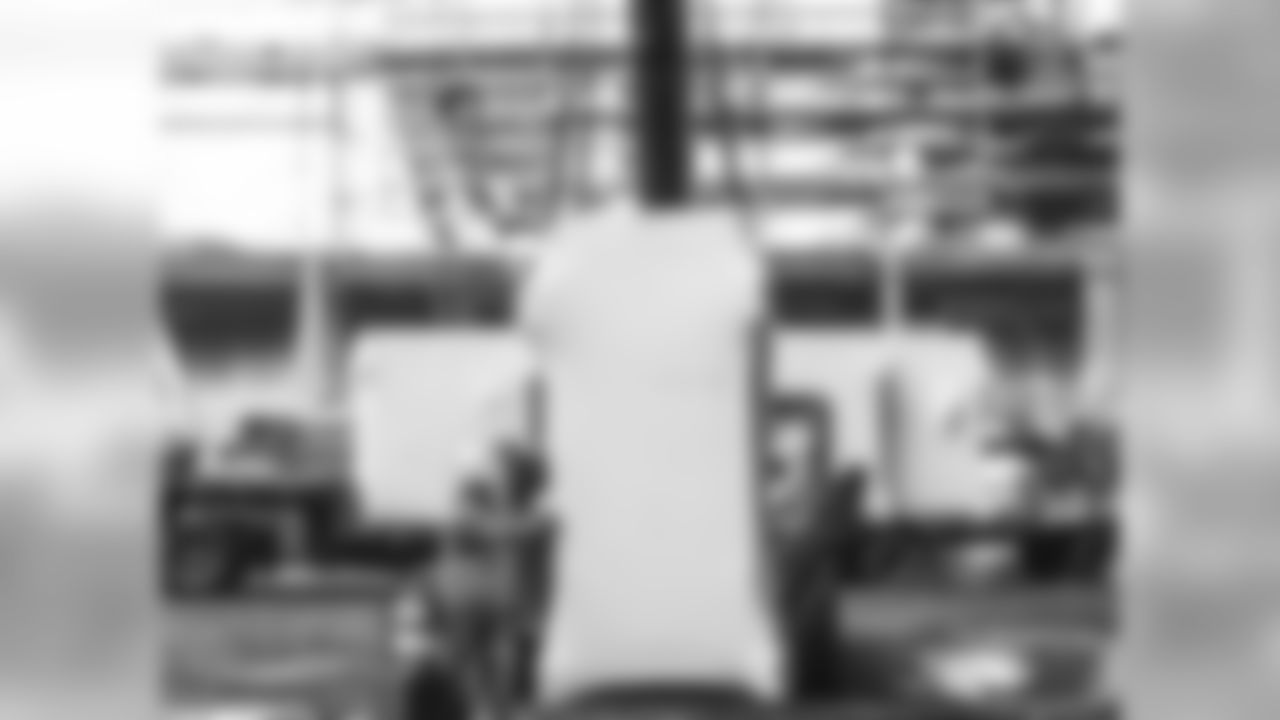
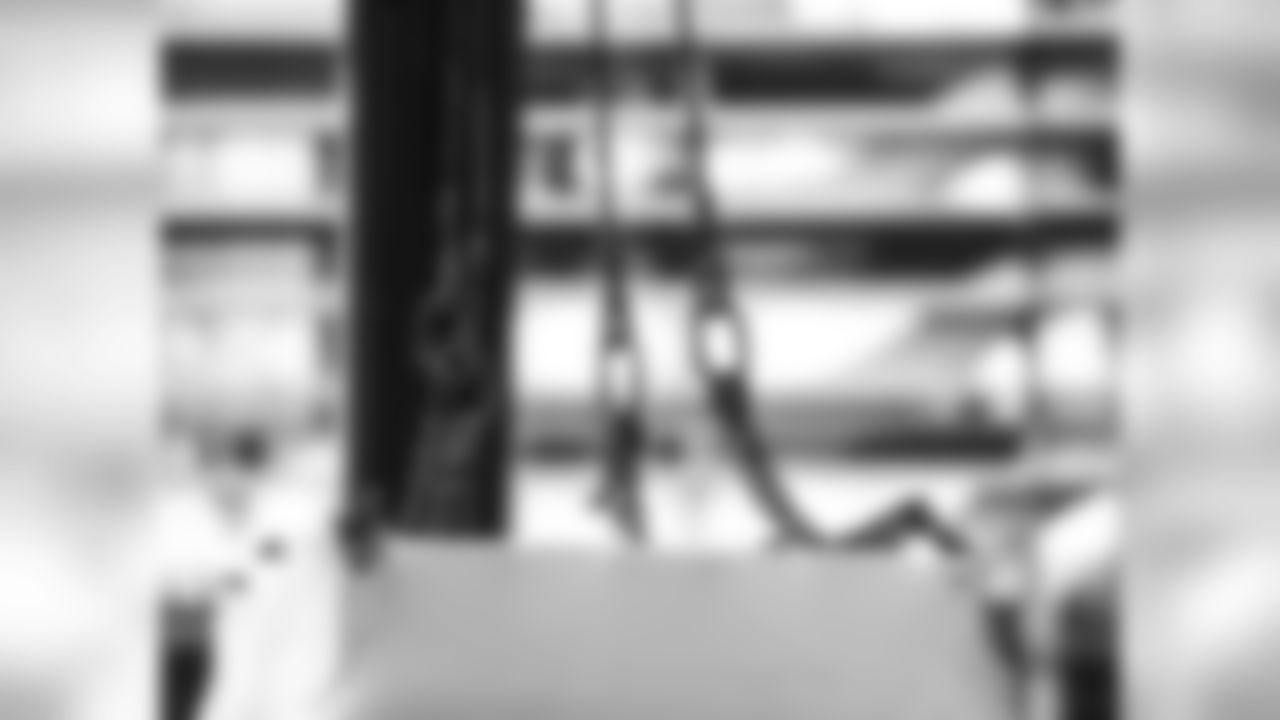
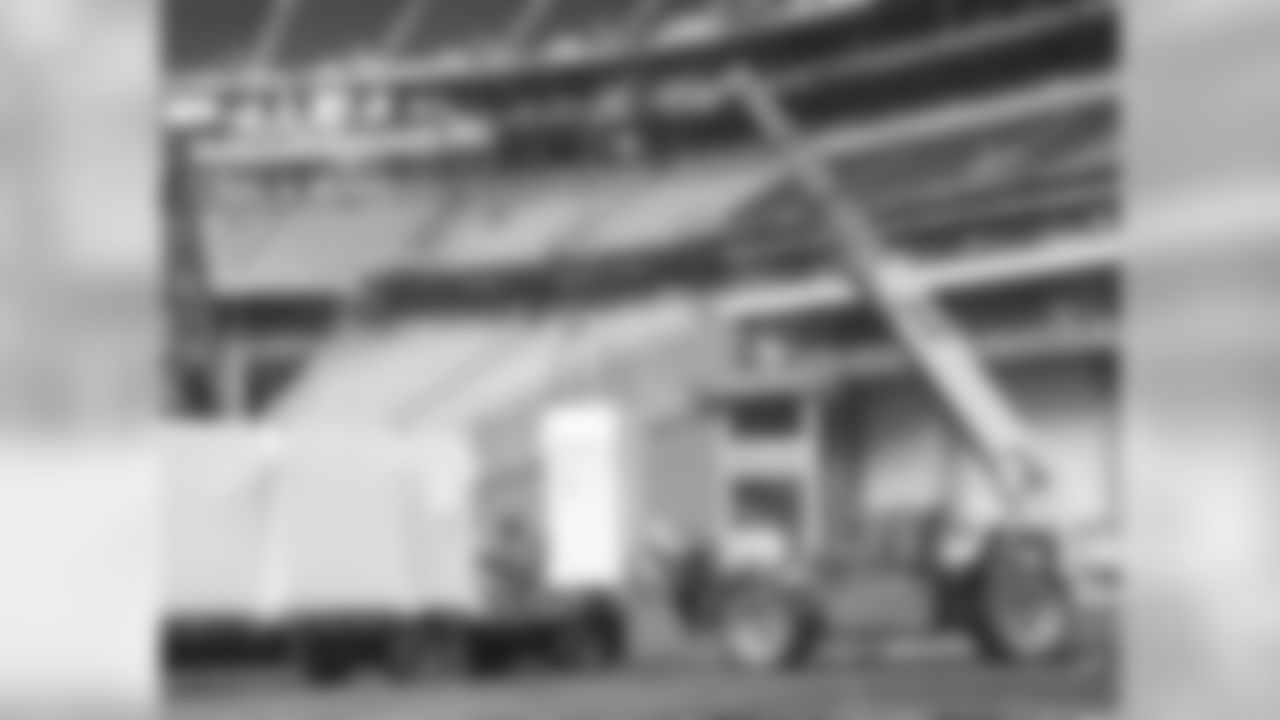
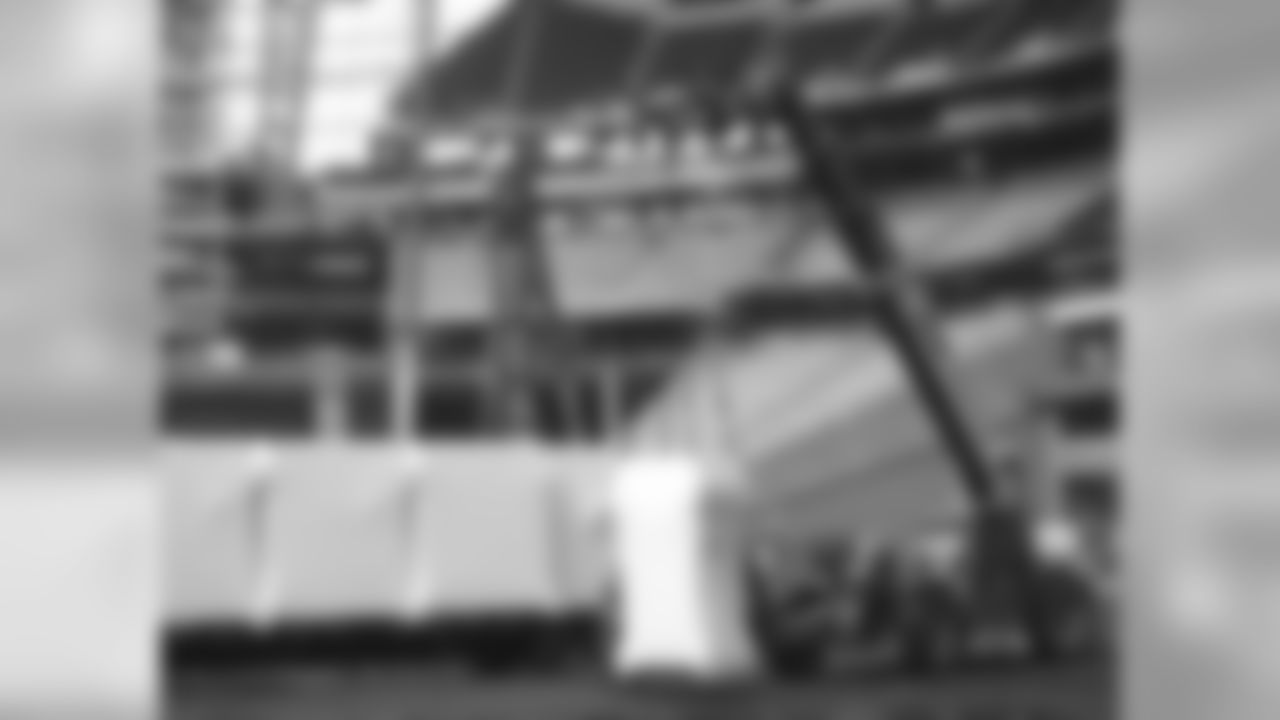
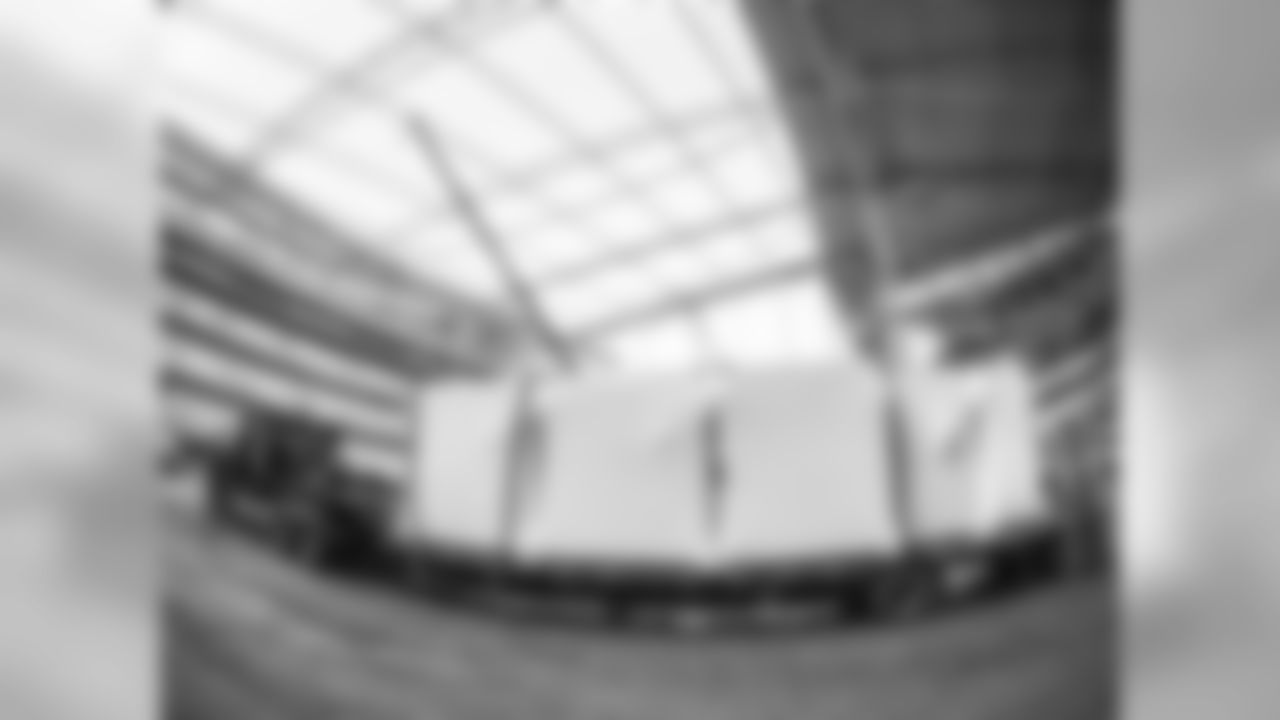

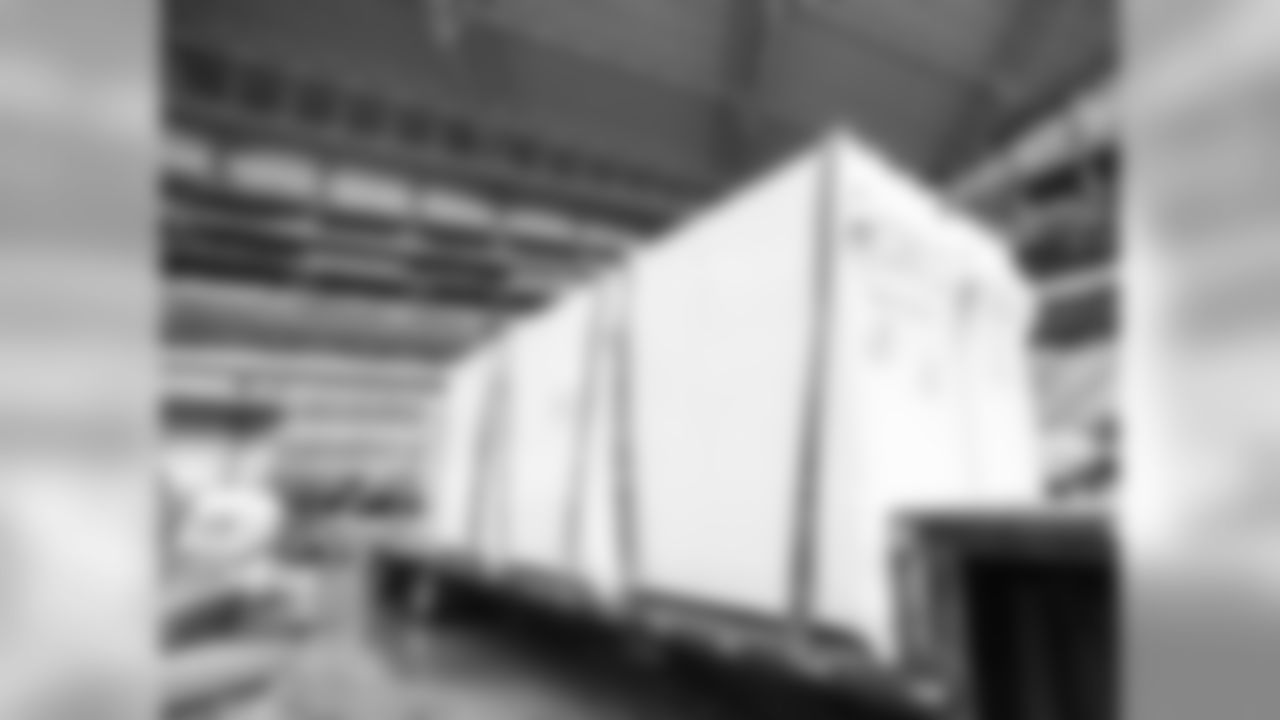

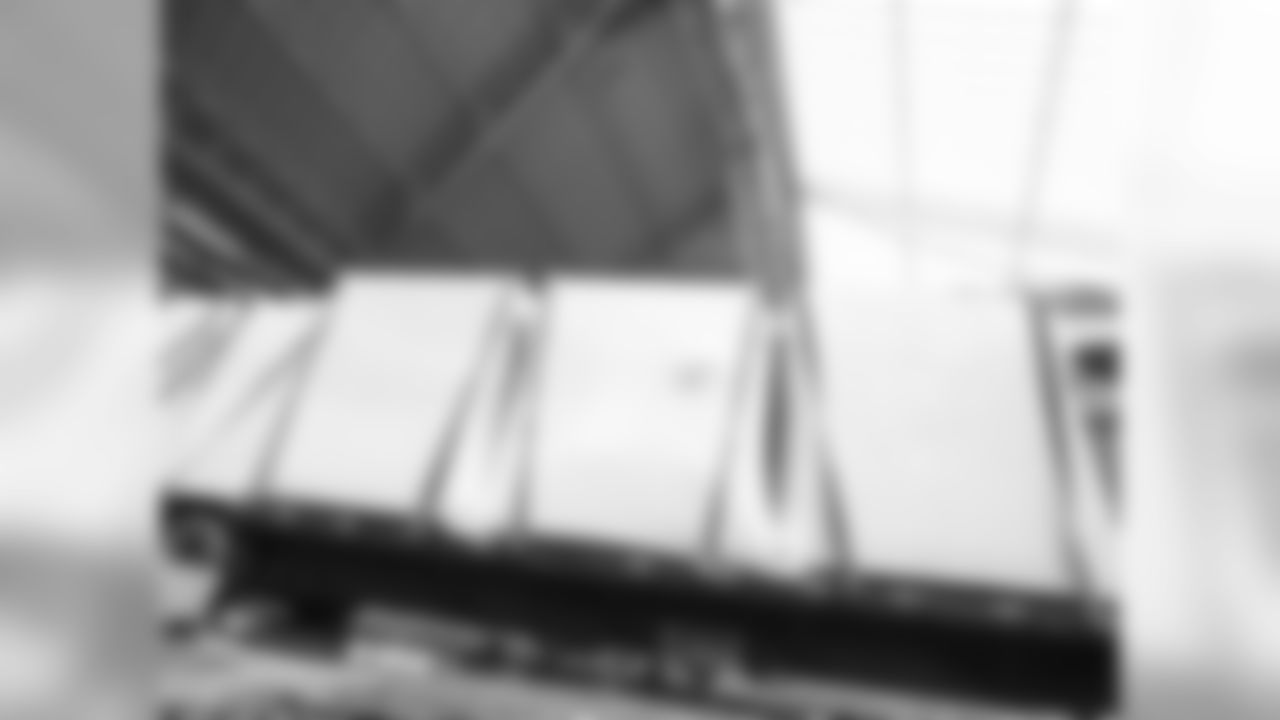
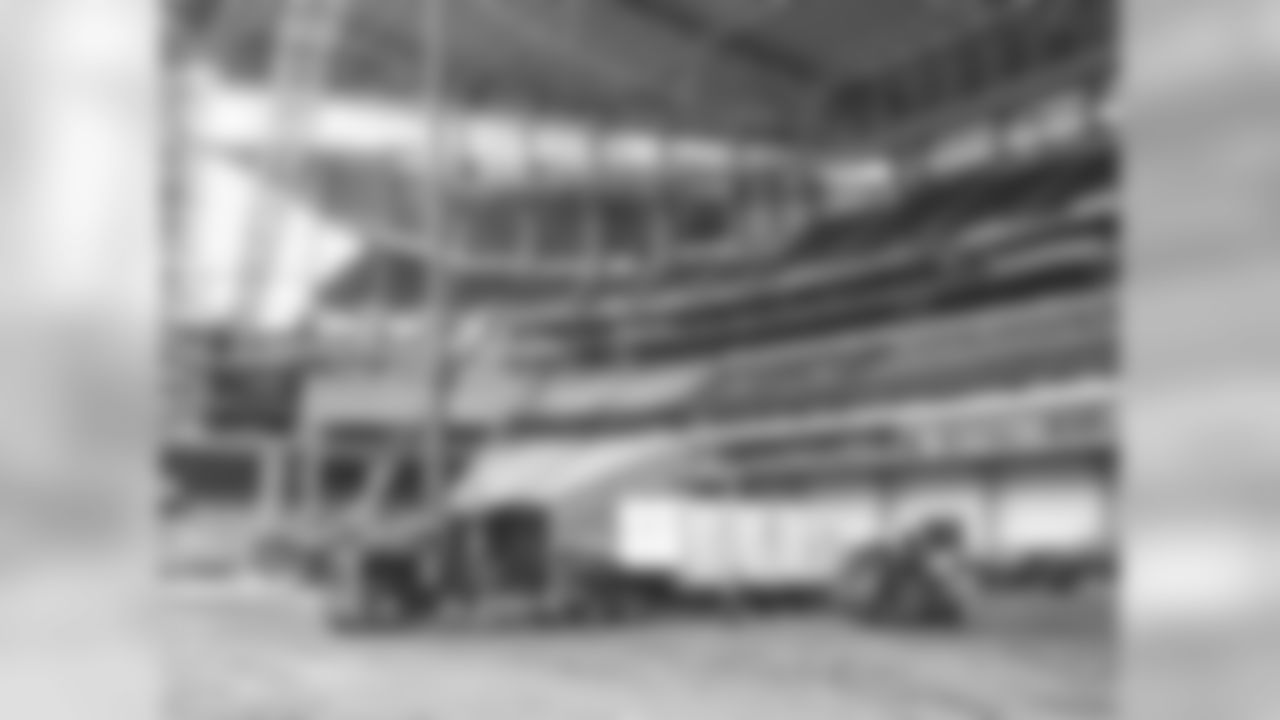
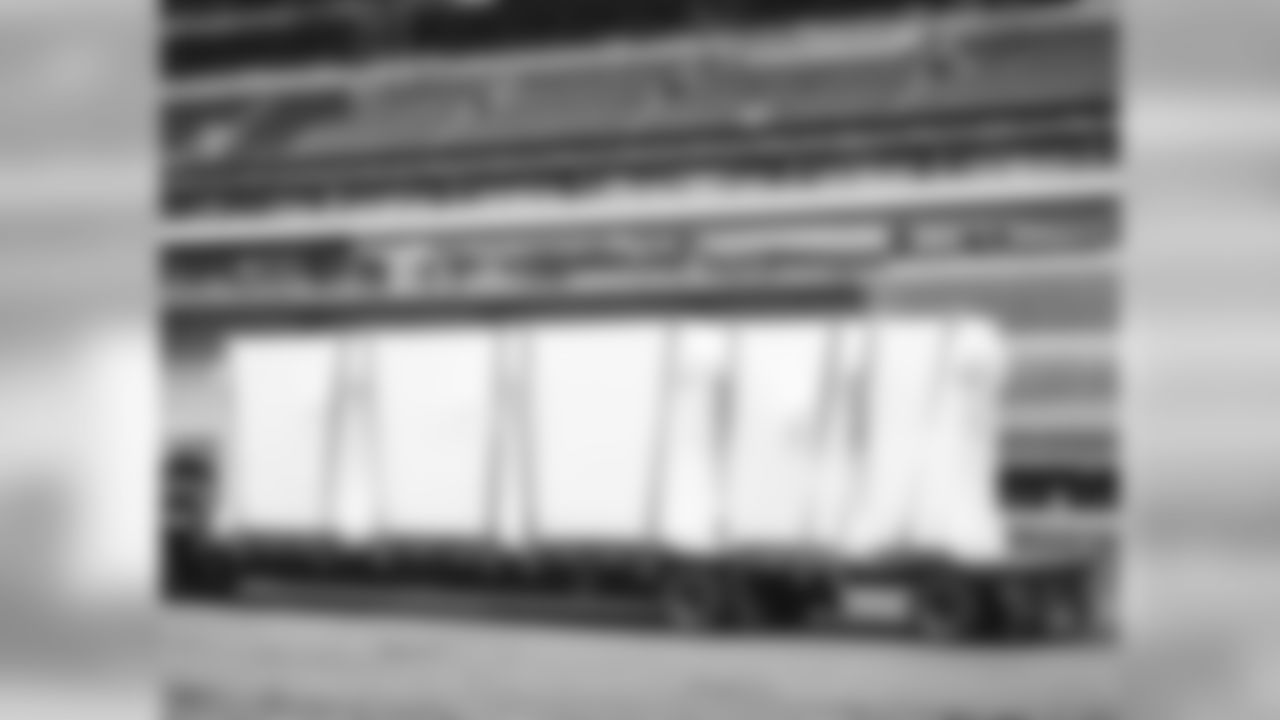
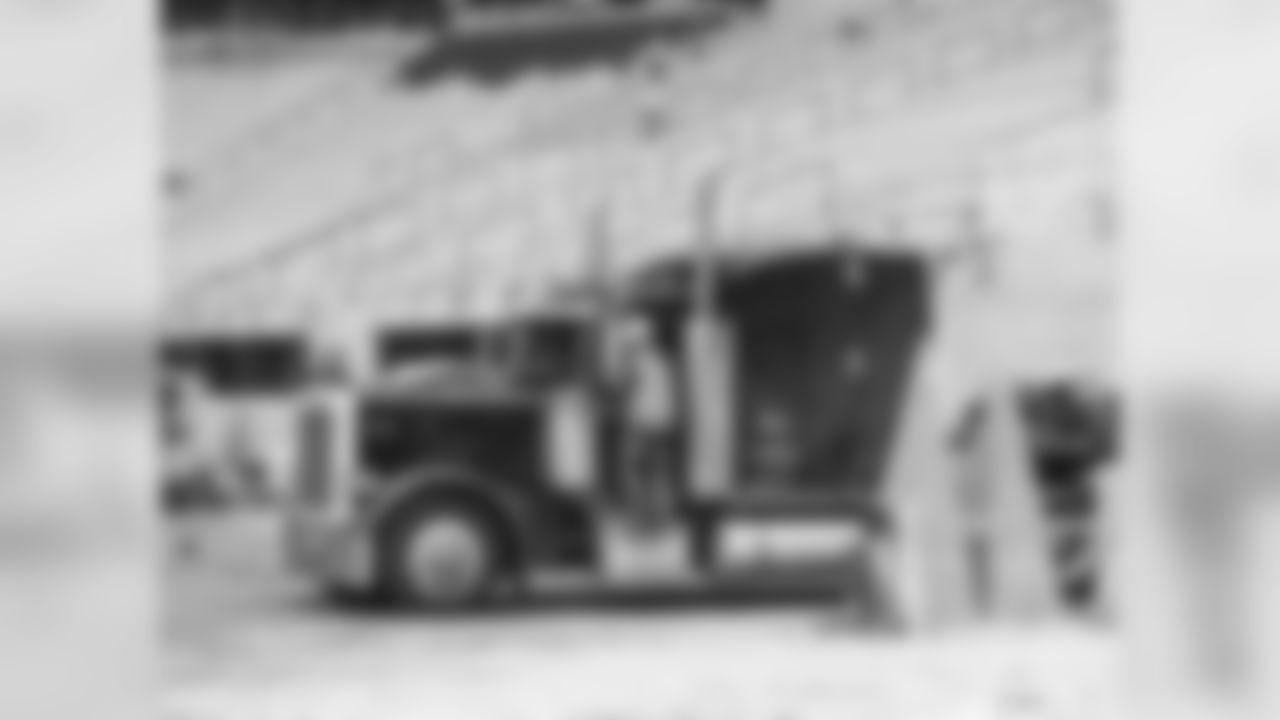
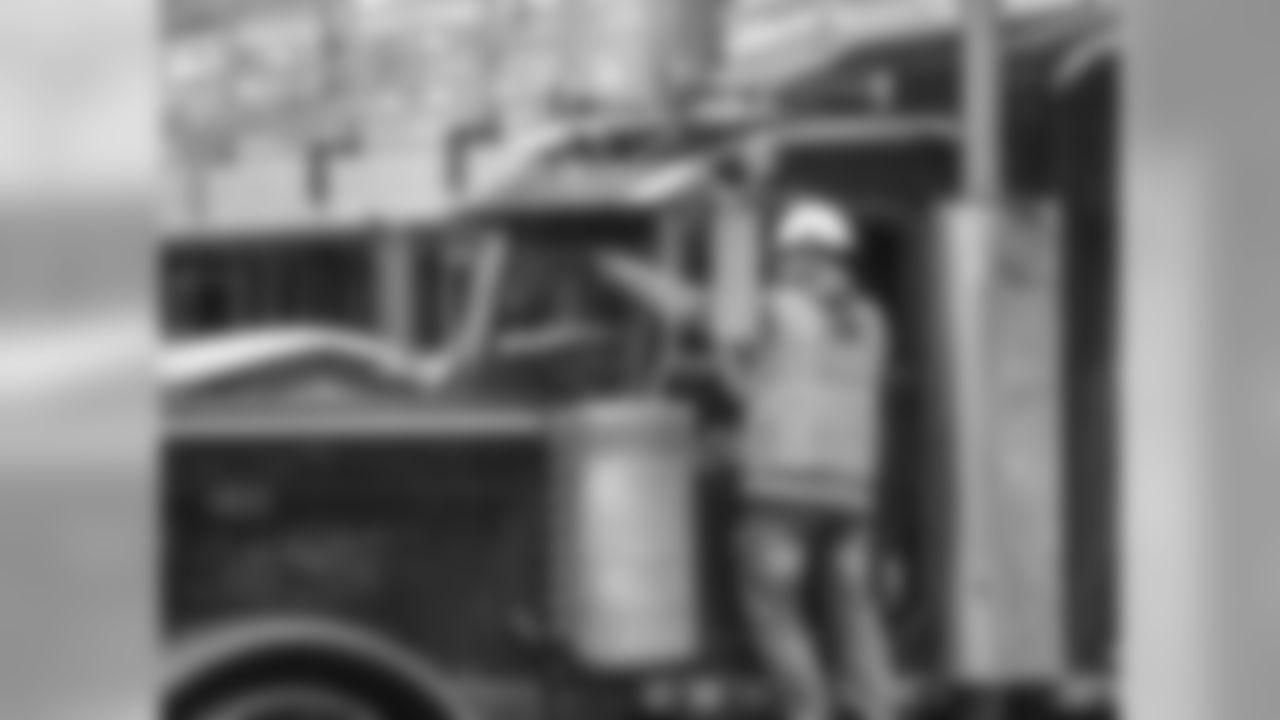
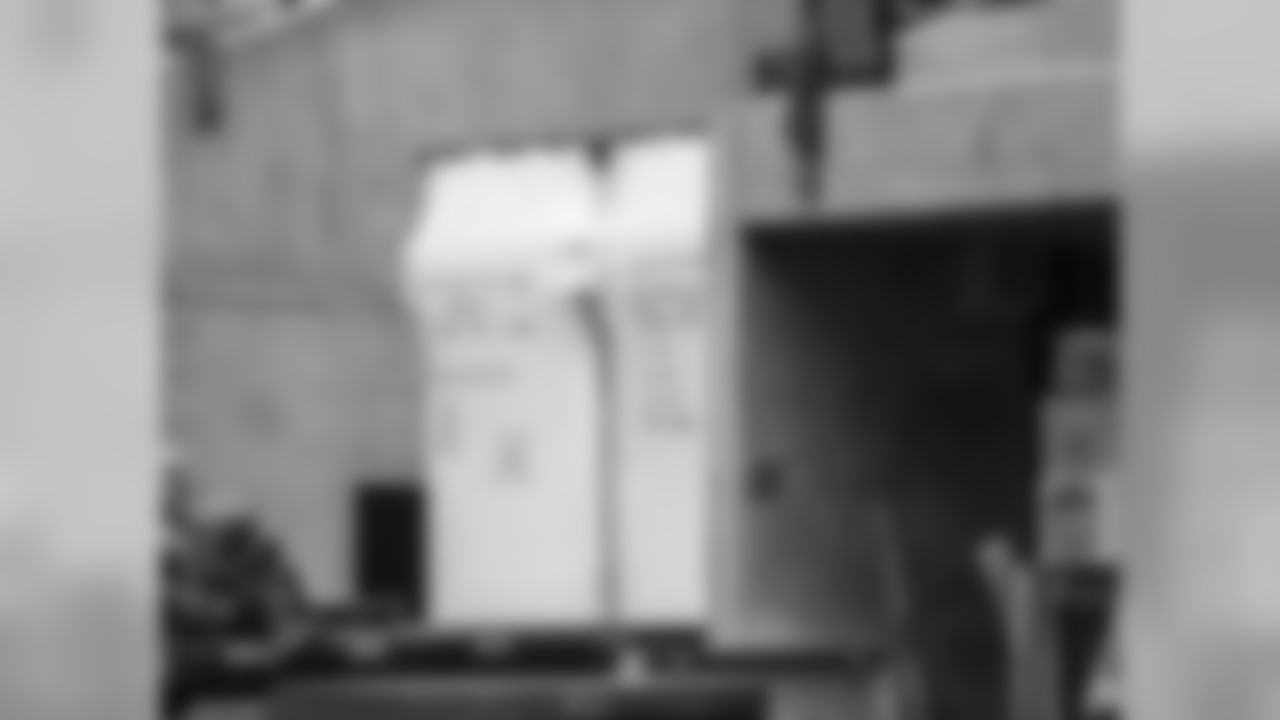
Fast forward 20 years, and Ohm is Daktronics project manager for the more than 25,000 square feet of 13HD video and ribbon boards made in Minnesota for U.S. Bank Stadium. The amount of 13HD displays will be the most in the NFL and will feature a main scoreboard at the east end that will rank as one of the 10 biggest in the NFL.
"It's a dream come true for me," Ohm said of working on this project. "I remember going to games with my father at the Metrodome, and I can't wait to take my son to see games at U.S. Bank Stadium."
Watch: A new view of construction is available from a camera that has been mounted on the west scoreboard. It will provide a view of the installation of the main scoreboard in the east end zone. Panels for the east scoreboard are arriving today.
The Vikings will be one of nine NFL teams using 13HD technology and one of only two NFL teams using 13HD technology for ribbon displays. The state-of-the-art boards will be part of the incredible improvements to experiences for fans when the $1.08 billion venue opens in July 2016, even if the Vikings have been built to keep teams from lighting up the scoreboards.
"[Safety] Harrison Smith coming across the middle is as exciting as a touchdown for me, so I think it's great," Ohm said. "A lot of those games are decided at the final kick, so if they're watching the replays, watching the clocks, I think it adds to the game experience."
Ohm has put about eight months of work into the project. He visits the construction site regularly, coordinating with architects, engineers and project managers for the venue that is the largest project in state history.
Recently he met Daktronics Vice President of Manufacturing Matt Kurtenbach, who traveled from the company's headquarters in Brookings, South Dakota, to Redwood Falls, a town of more than 5,000 located approximately 115 miles southwest of U.S. Bank Stadium.
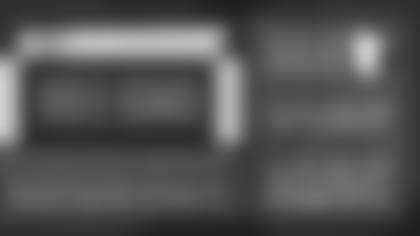
They joined Redwood Falls Plant Manager Tom Quackenbush in guiding a crew from Vikings Entertainment Network through the 150,000-square foot factory that opened in 2007. The location has previously produced a majority of the boards at Target Field, as well as indoor and outdoor boards at the University of Minnesota and some for the Jacksonville Jaguars.
The weather on this Thursday was cold with winds sweeping through under a blanket of blah clouds, but inside, misters maintained humidity levels in a warm environment to best aid construction of electronics. Panels of pixels that are capable of creating trillions of colors with different combinations of red, green and blue LEDs are built in this space.
Go inside the Daktronics' Factory in Redwood Falls to see what's going into the lighting at U.S. Bank Stadium.
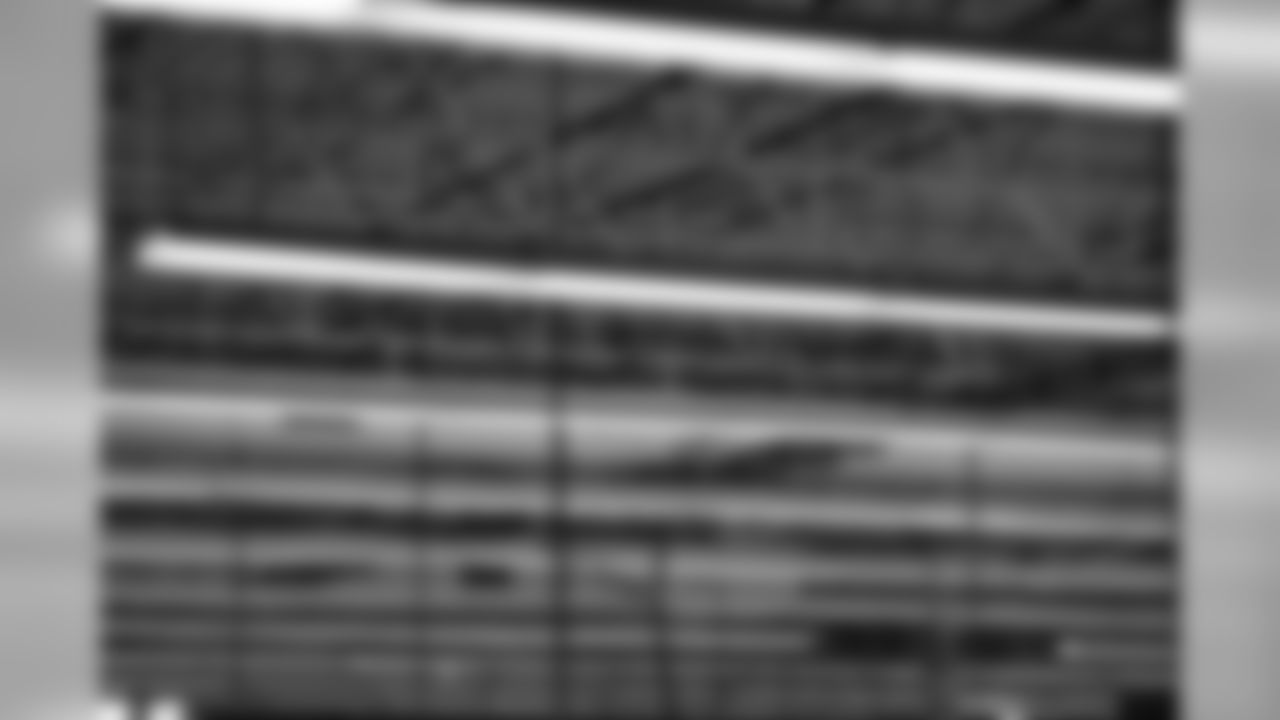
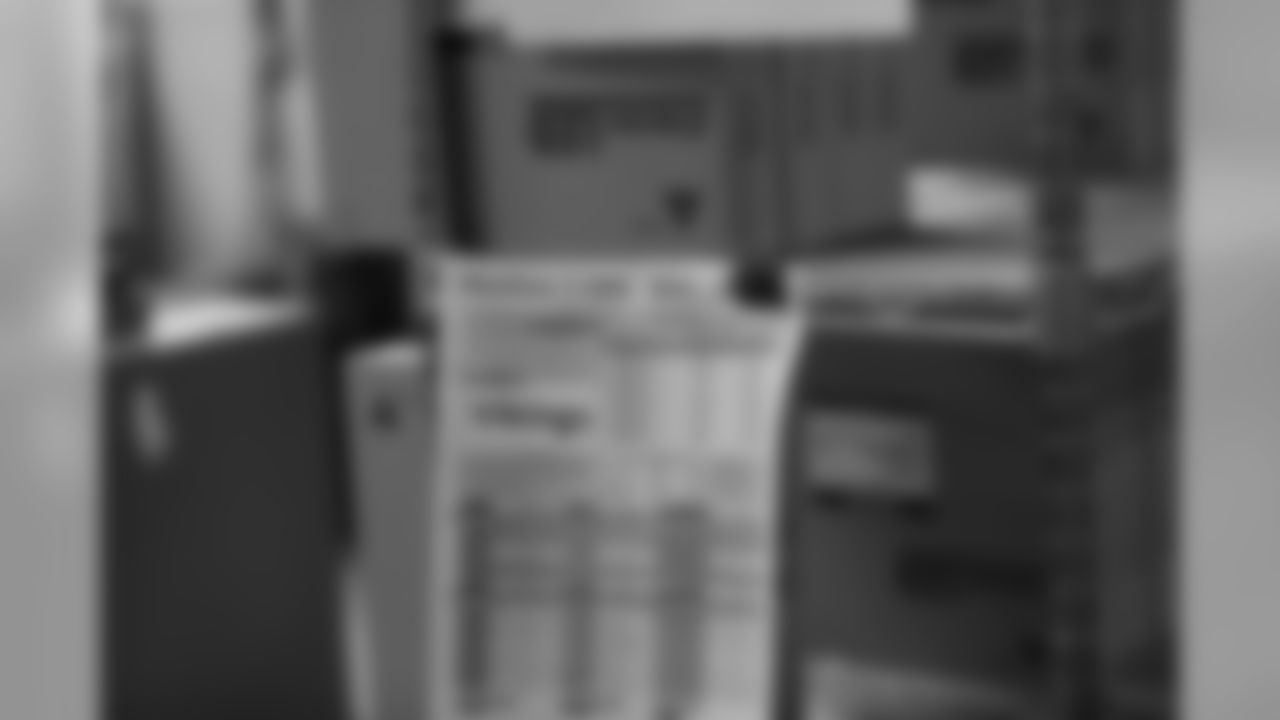
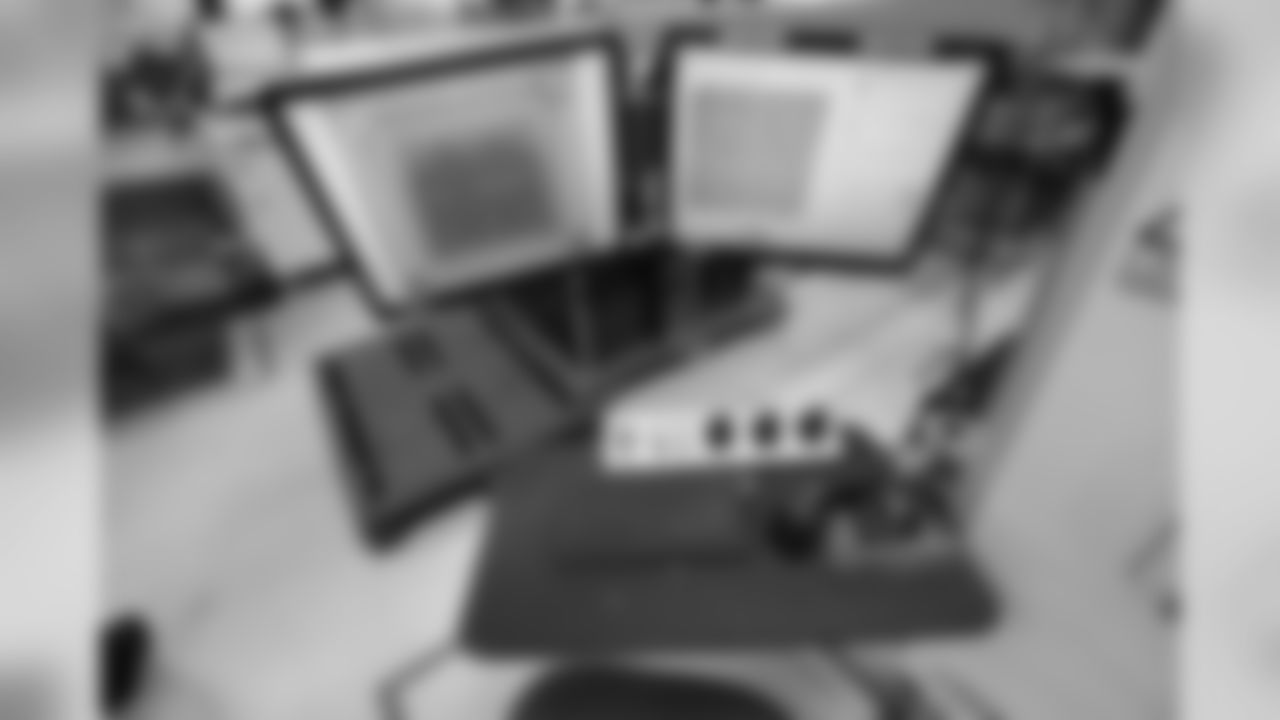
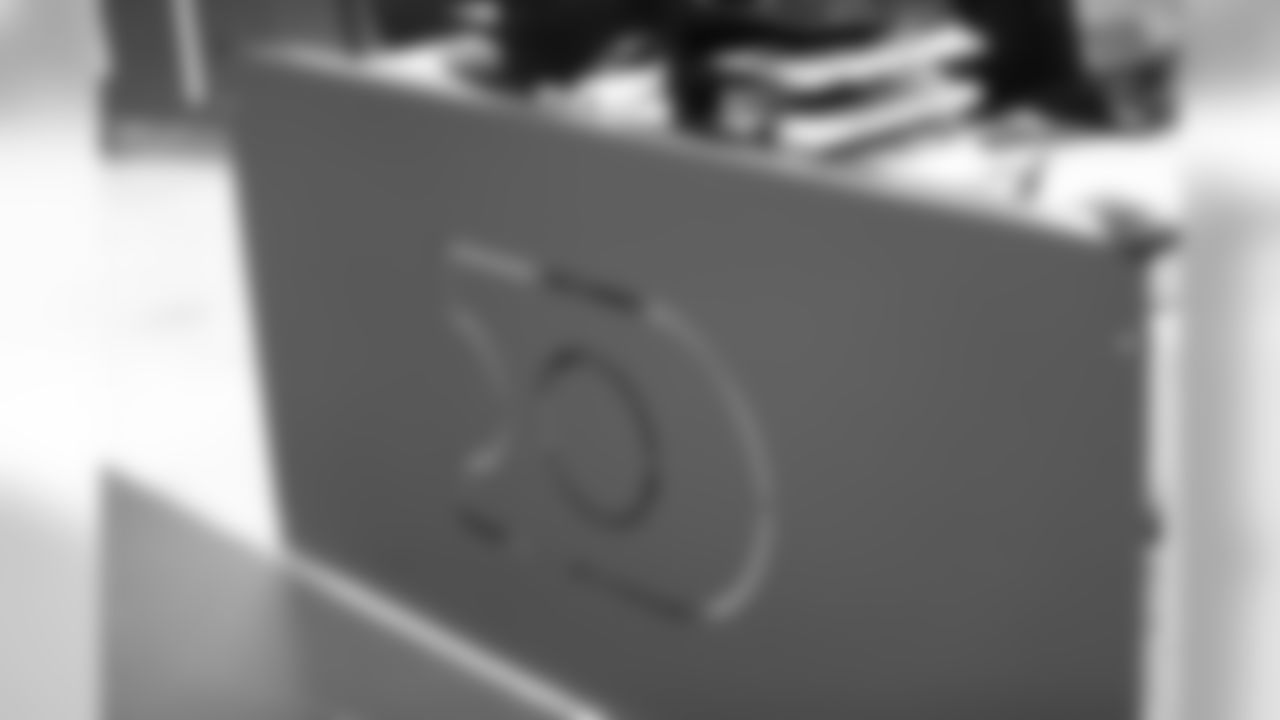
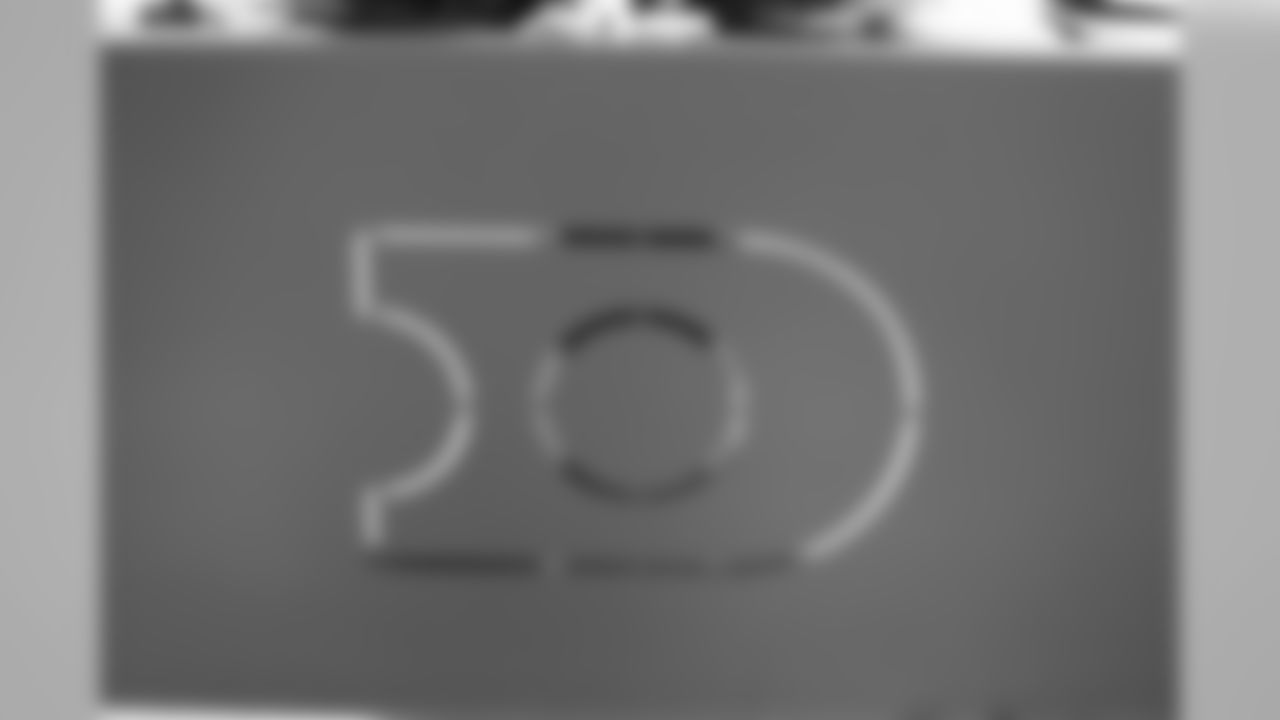
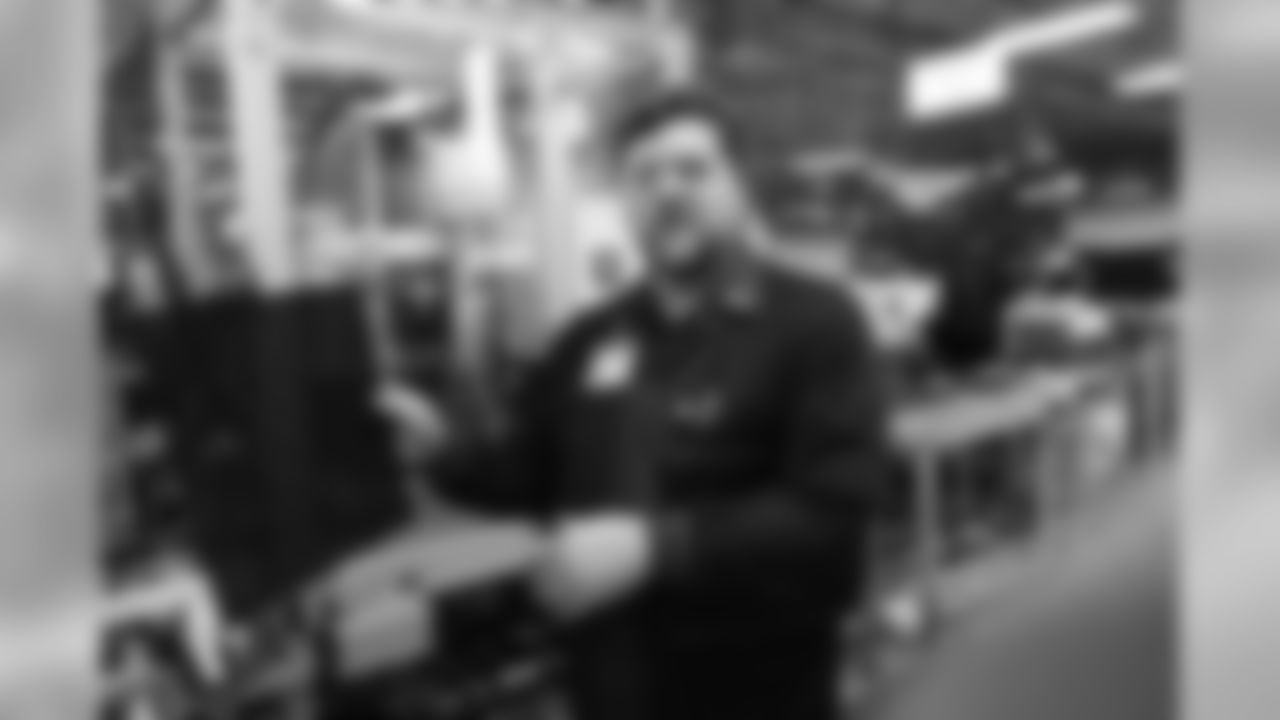
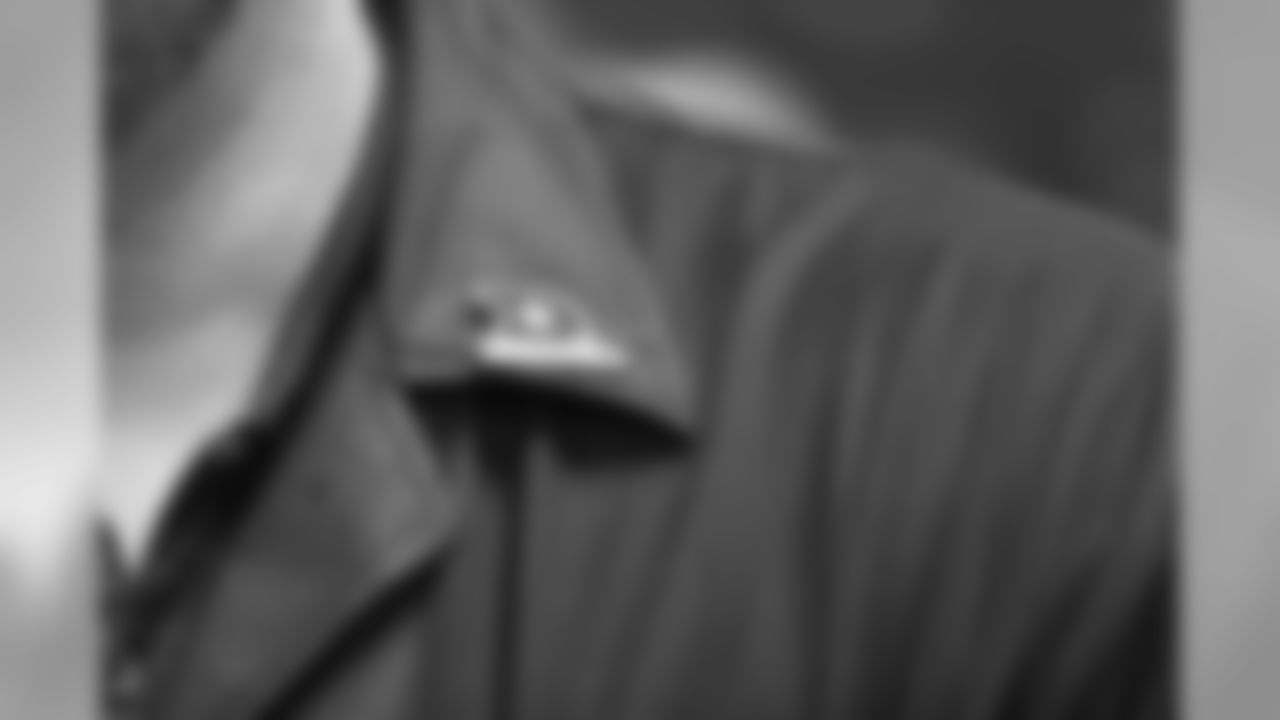
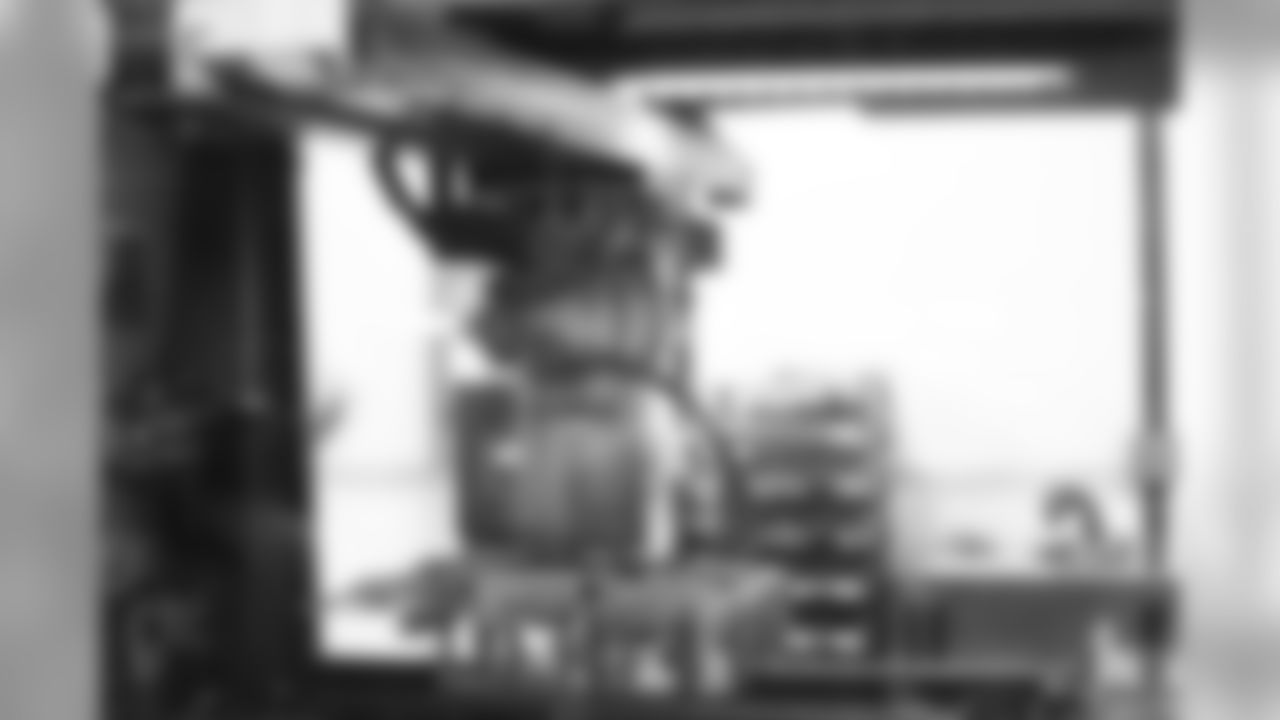
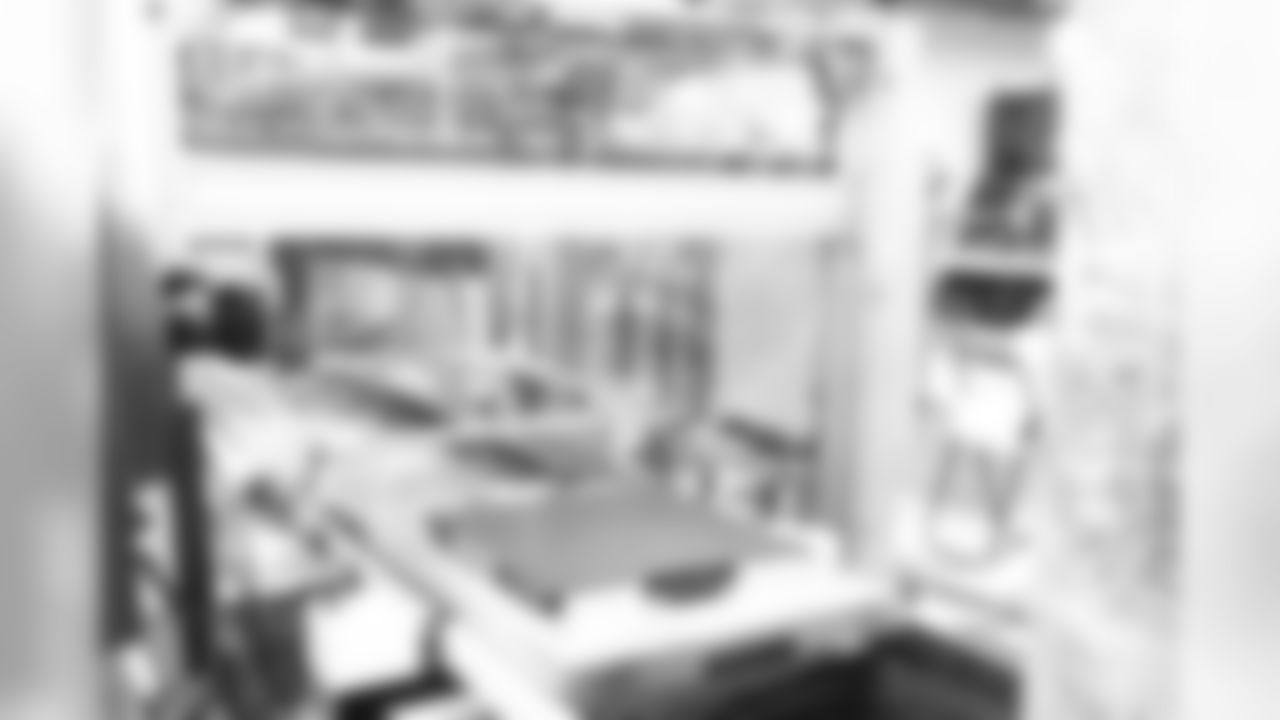
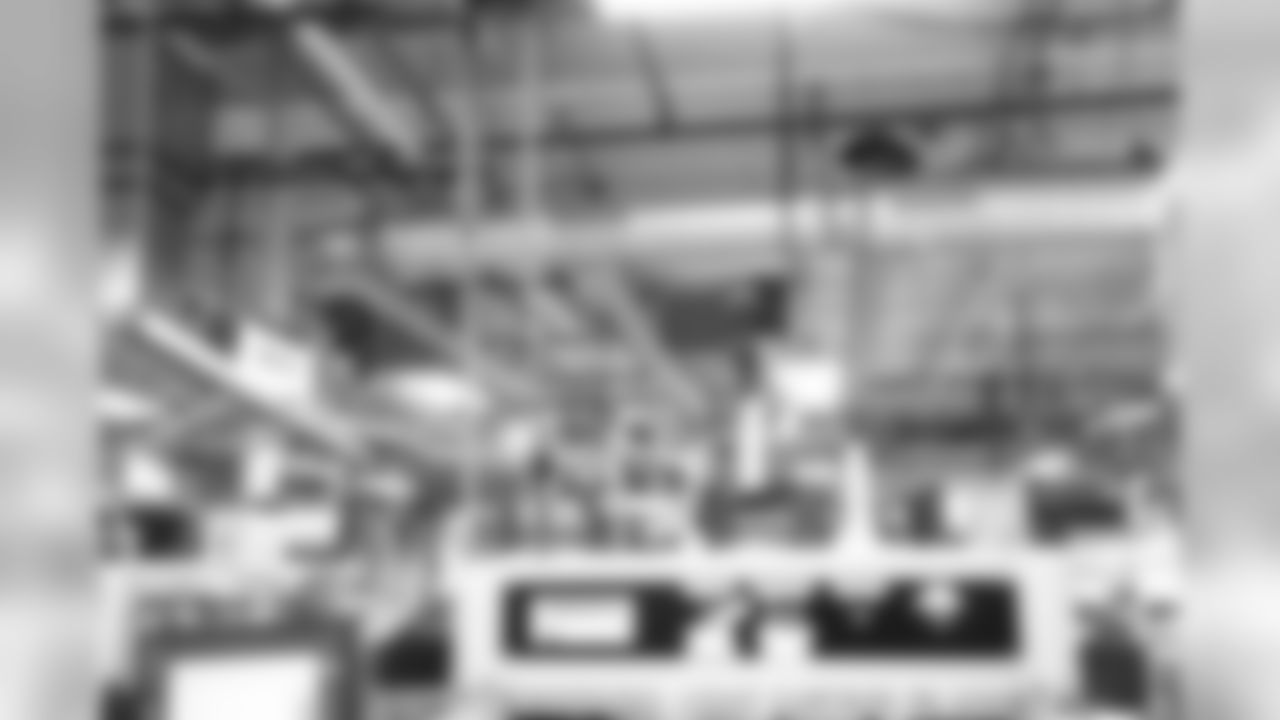
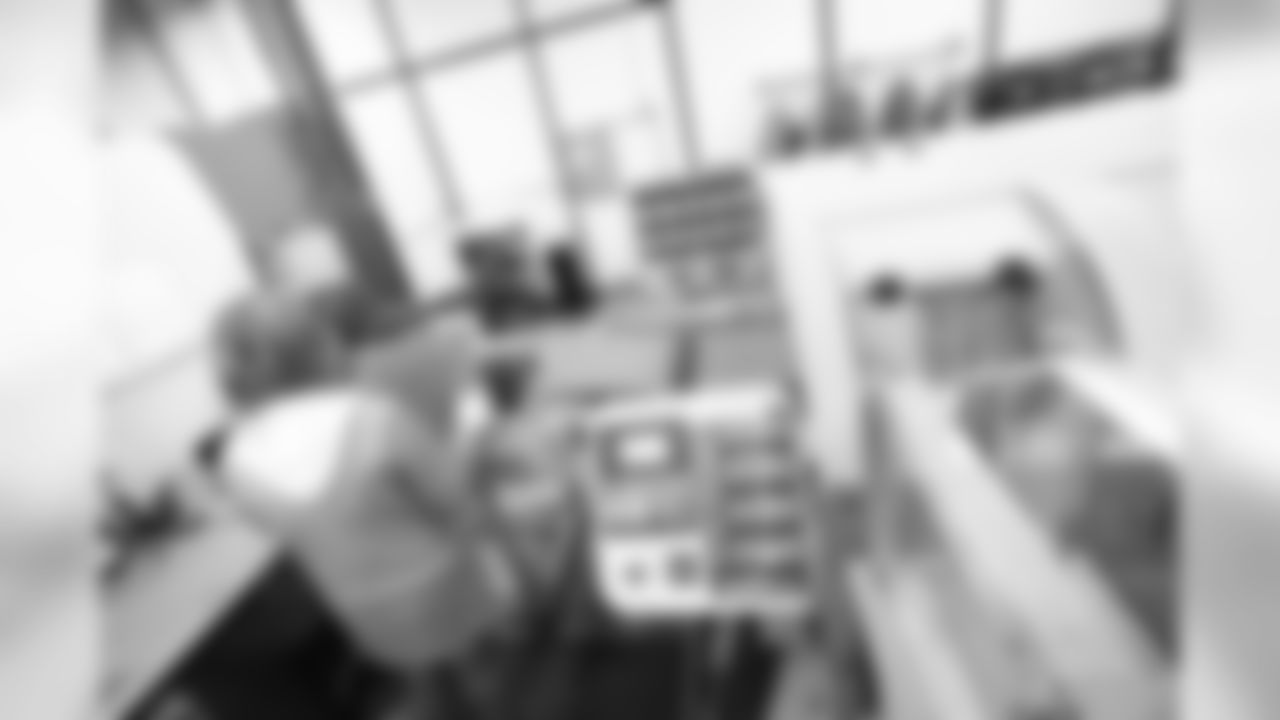
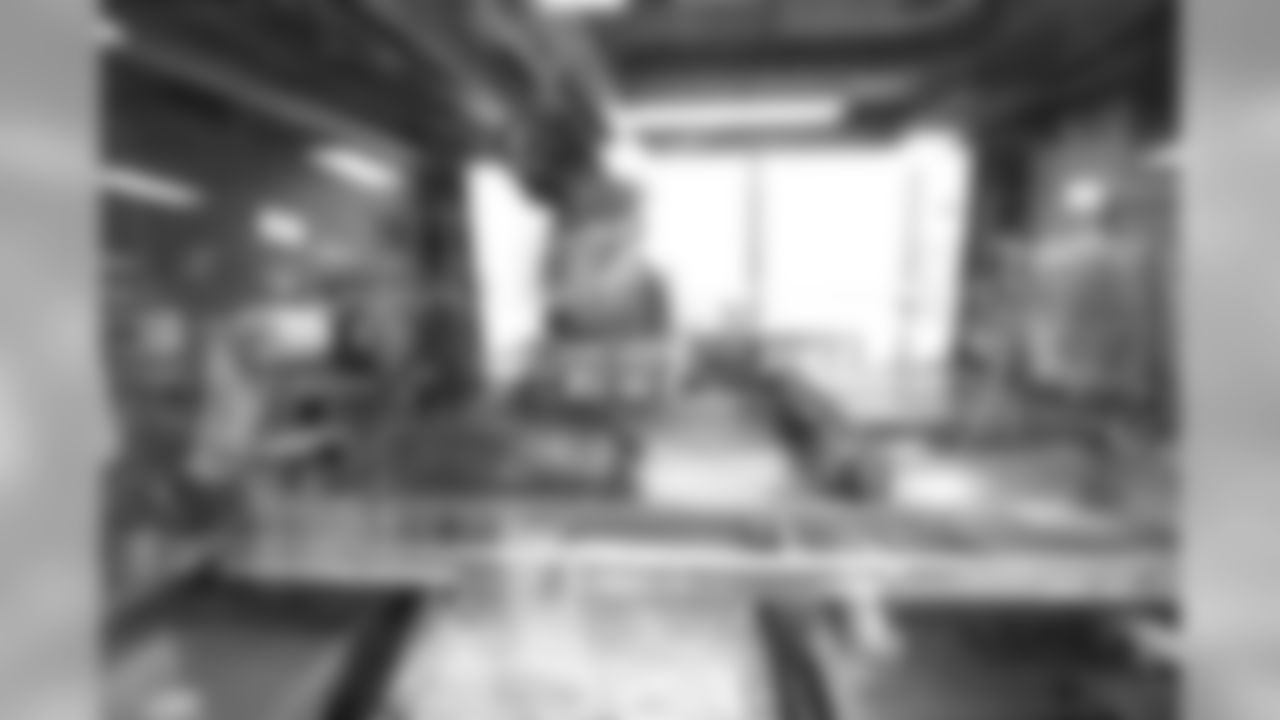
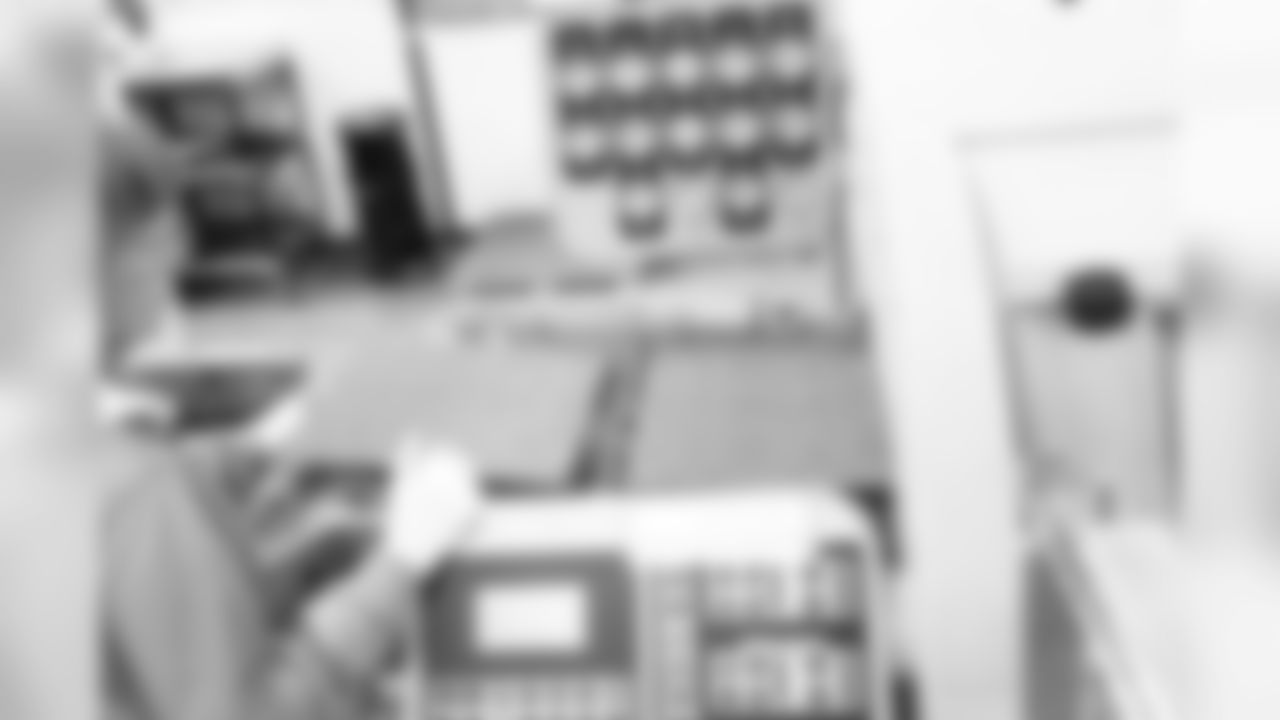
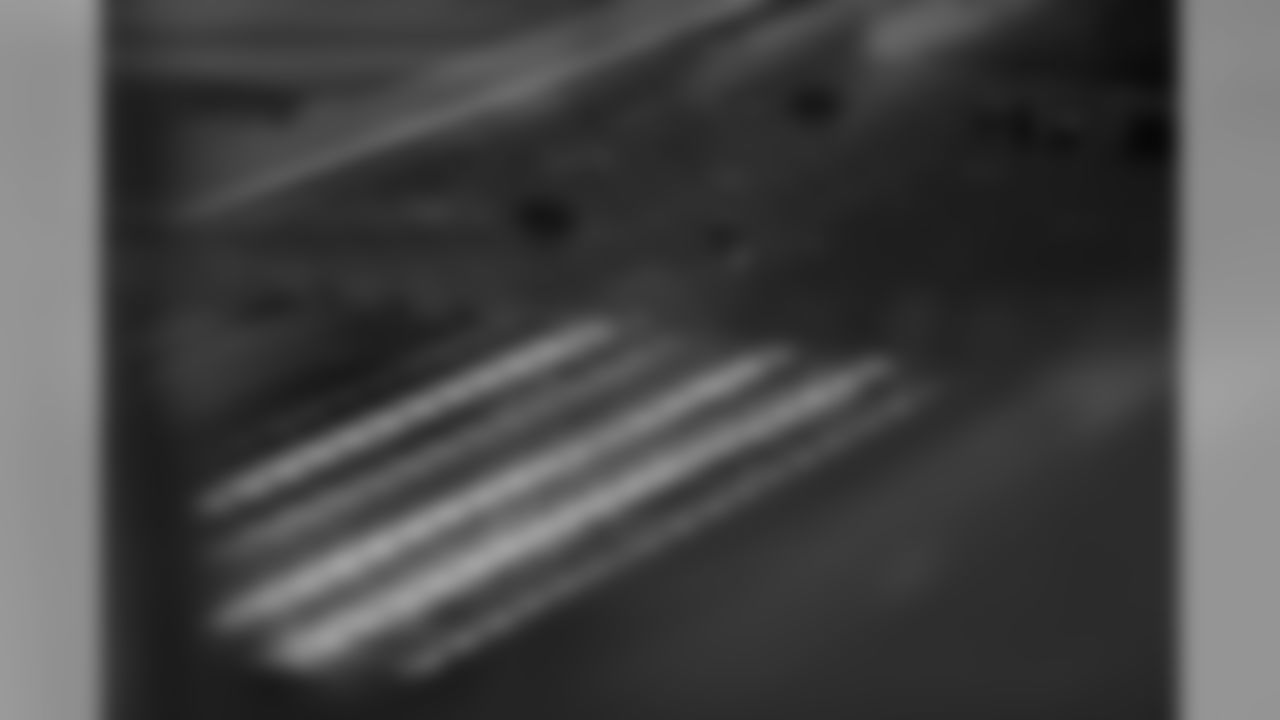
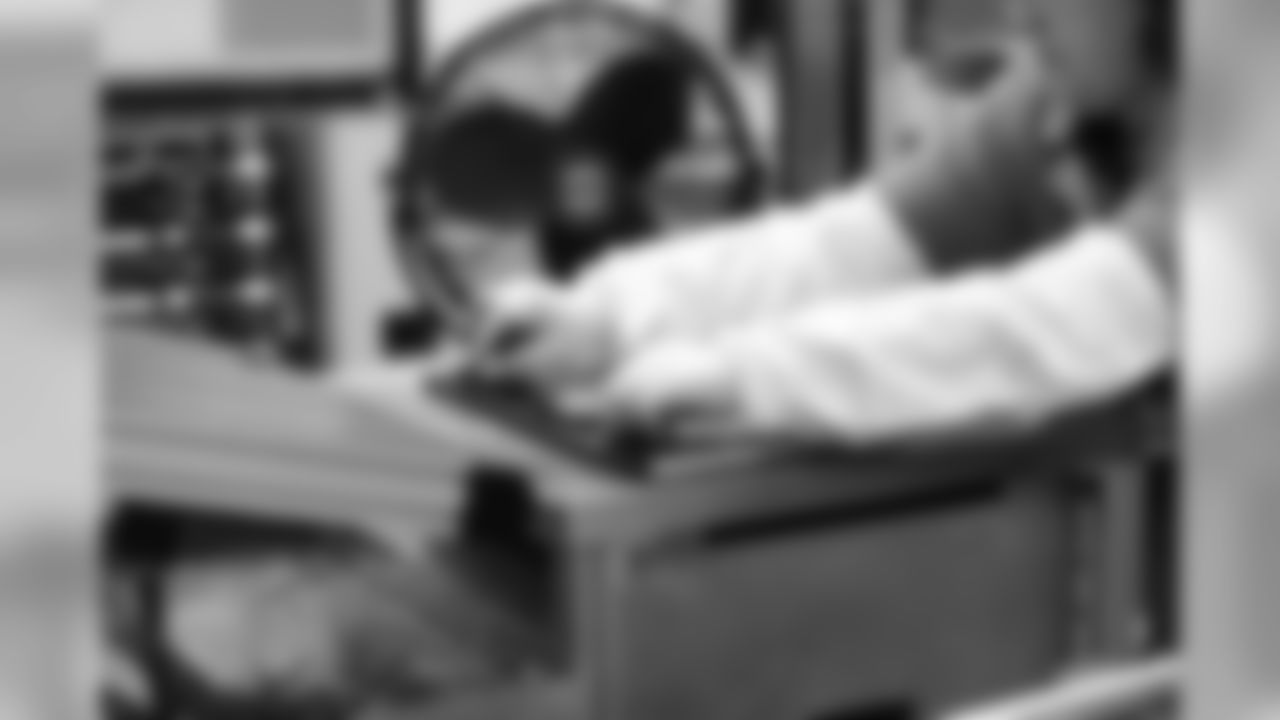
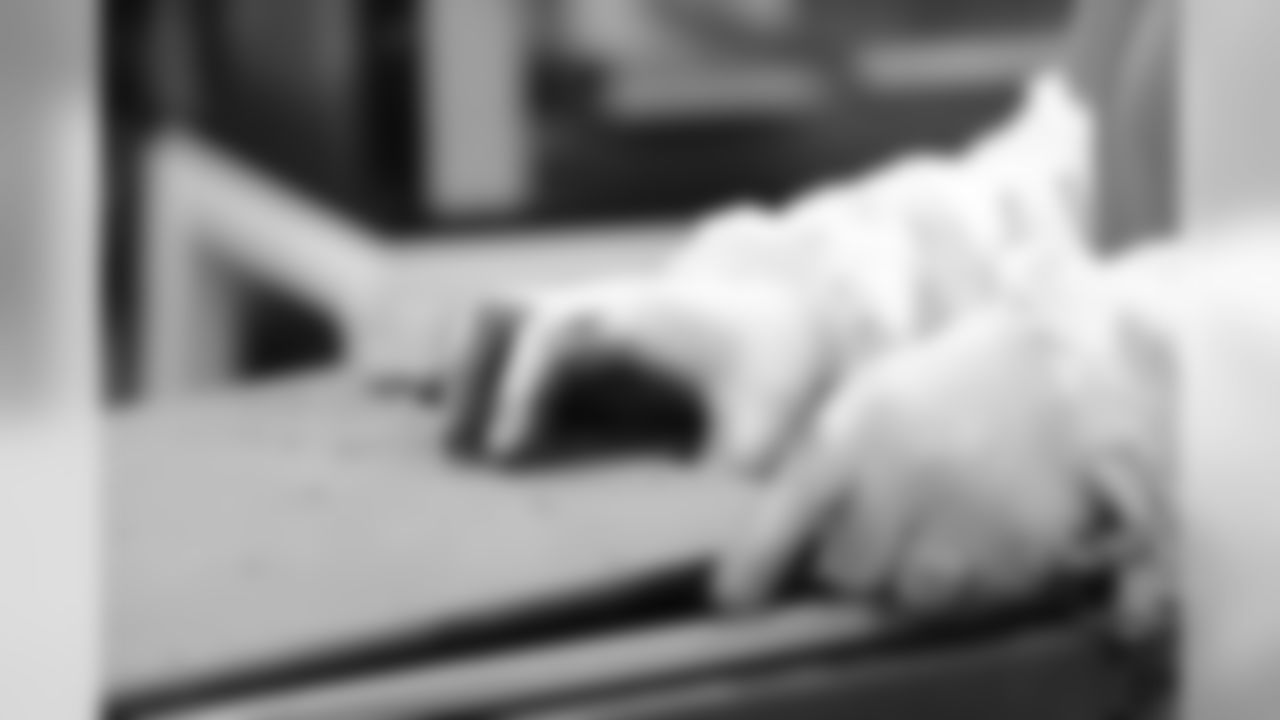
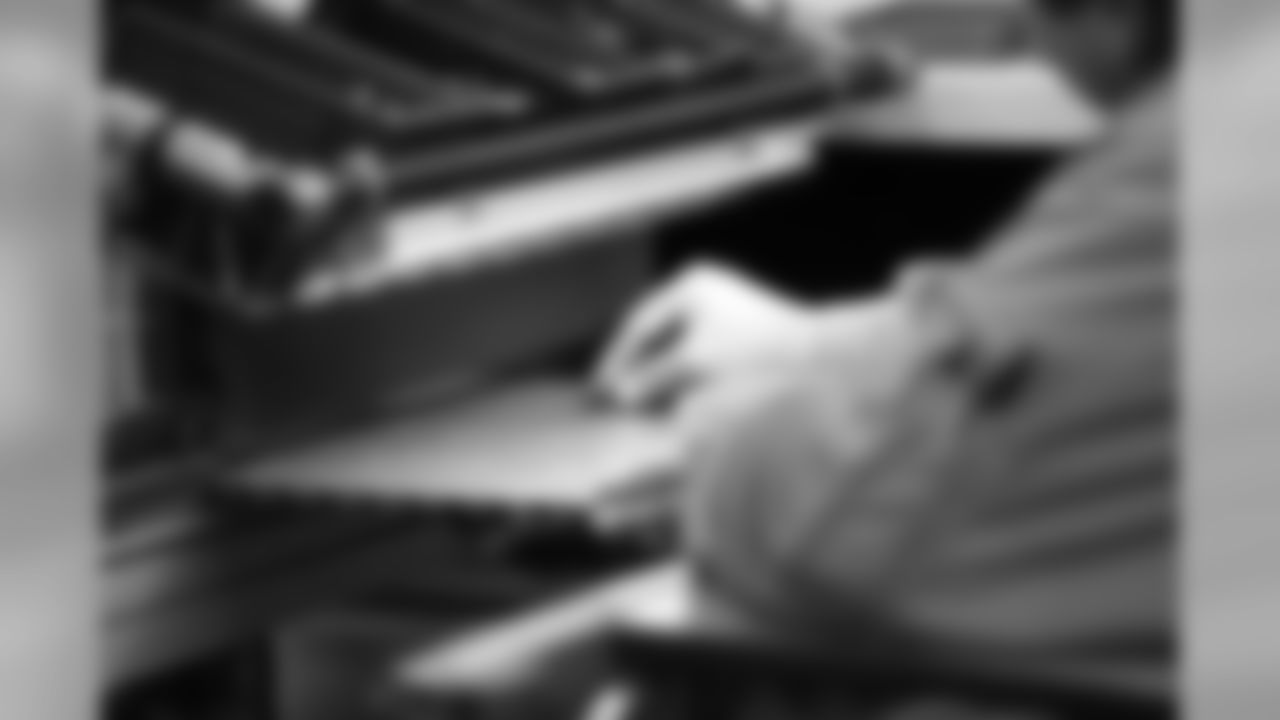
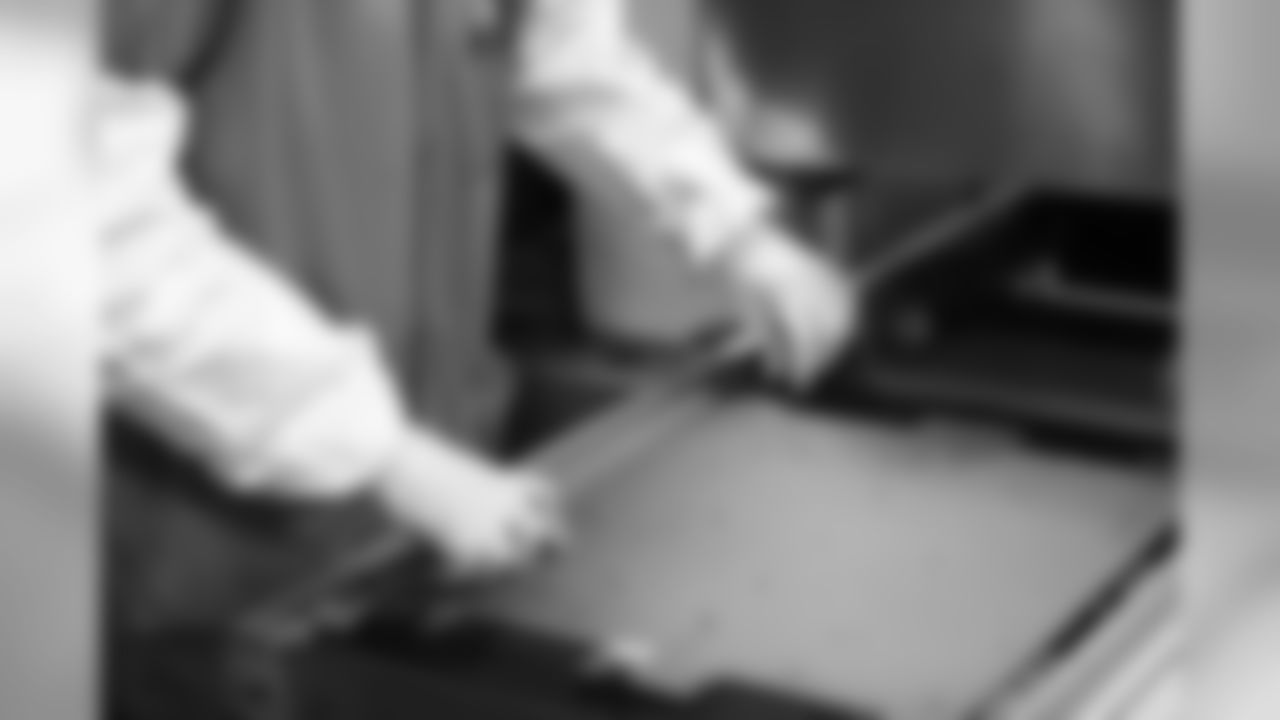
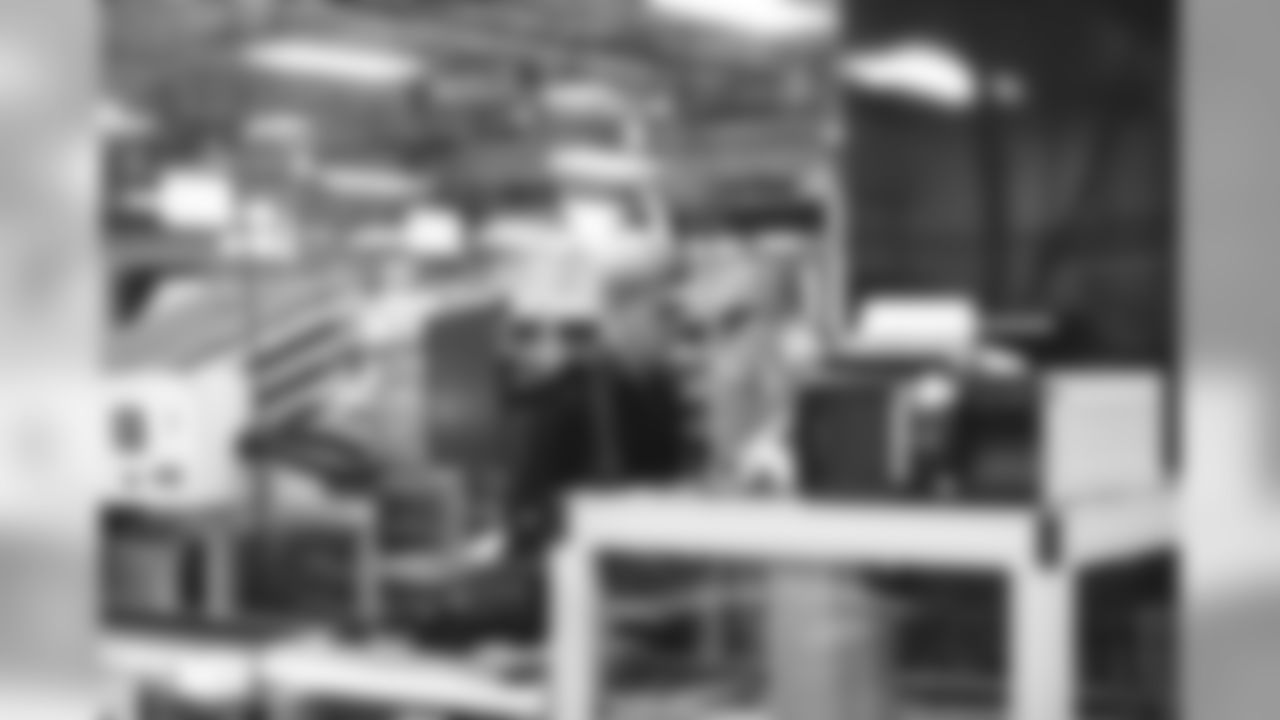
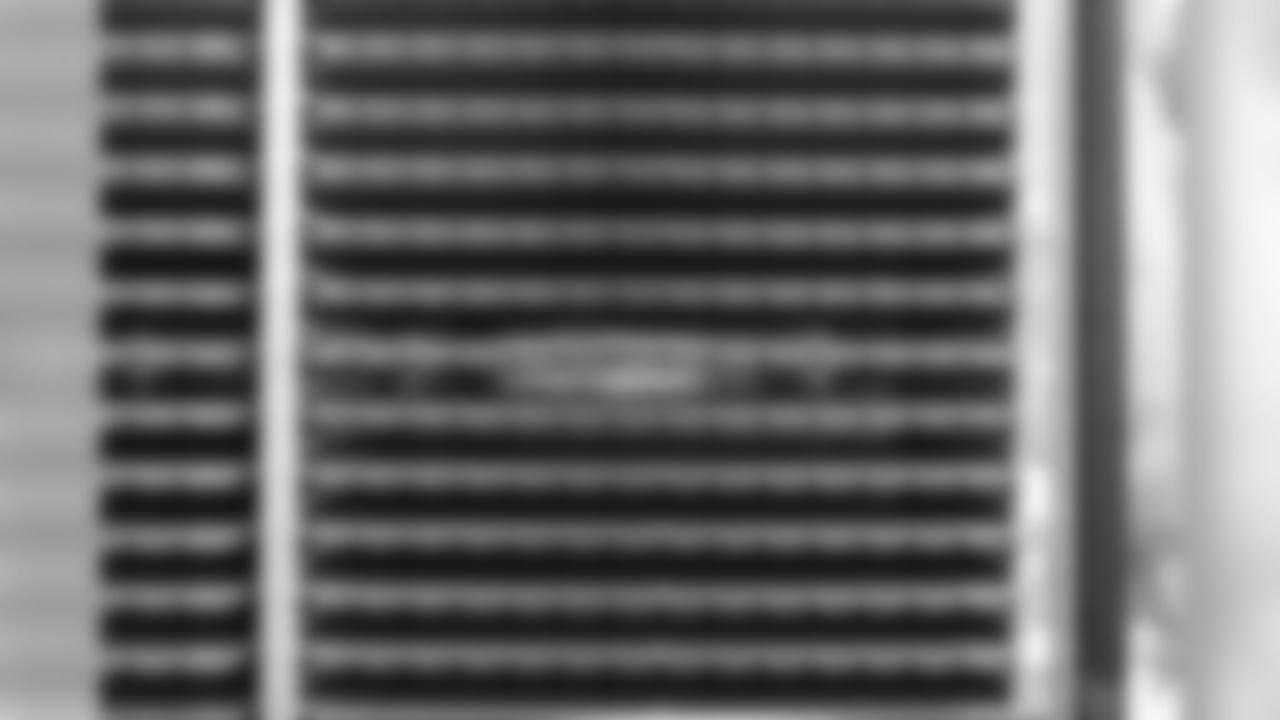

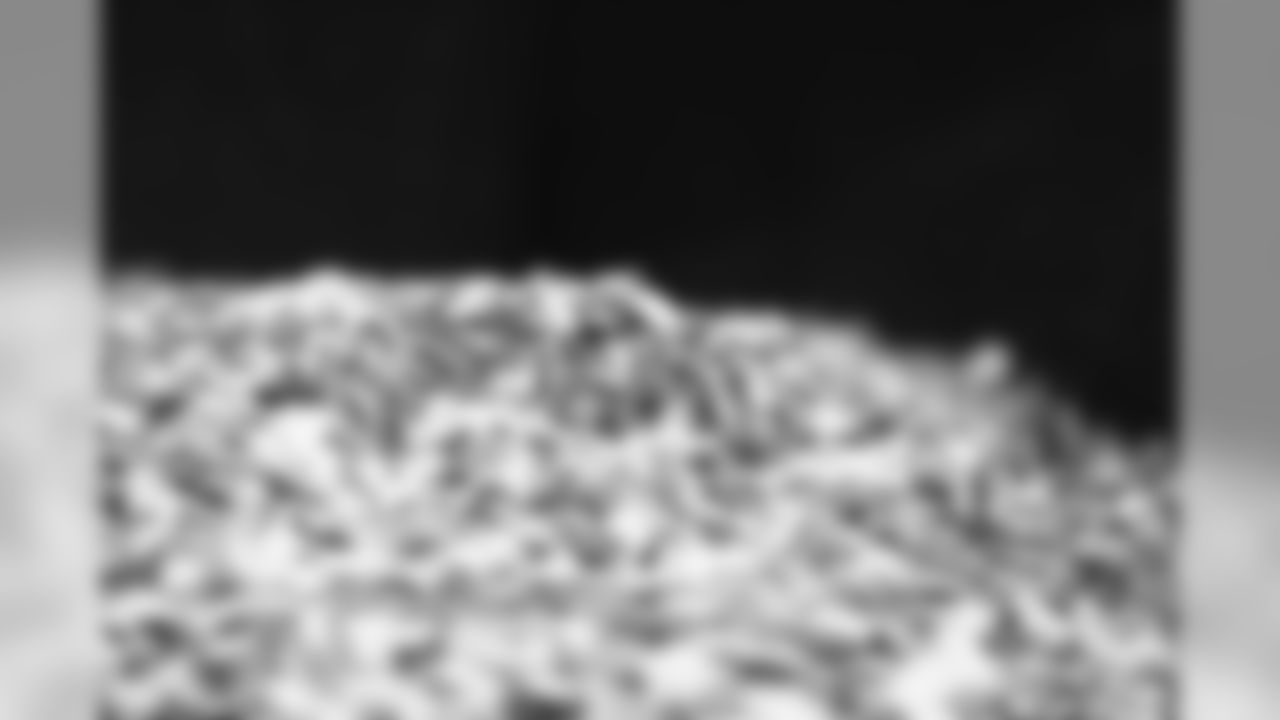
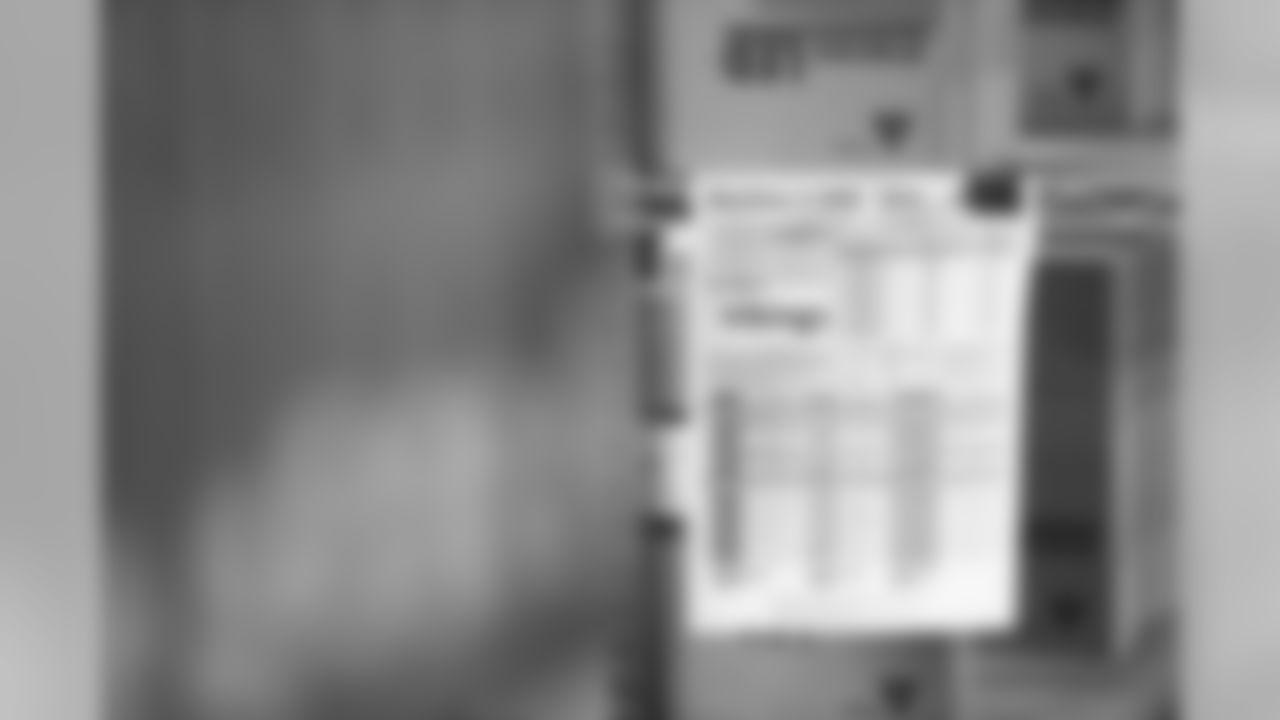
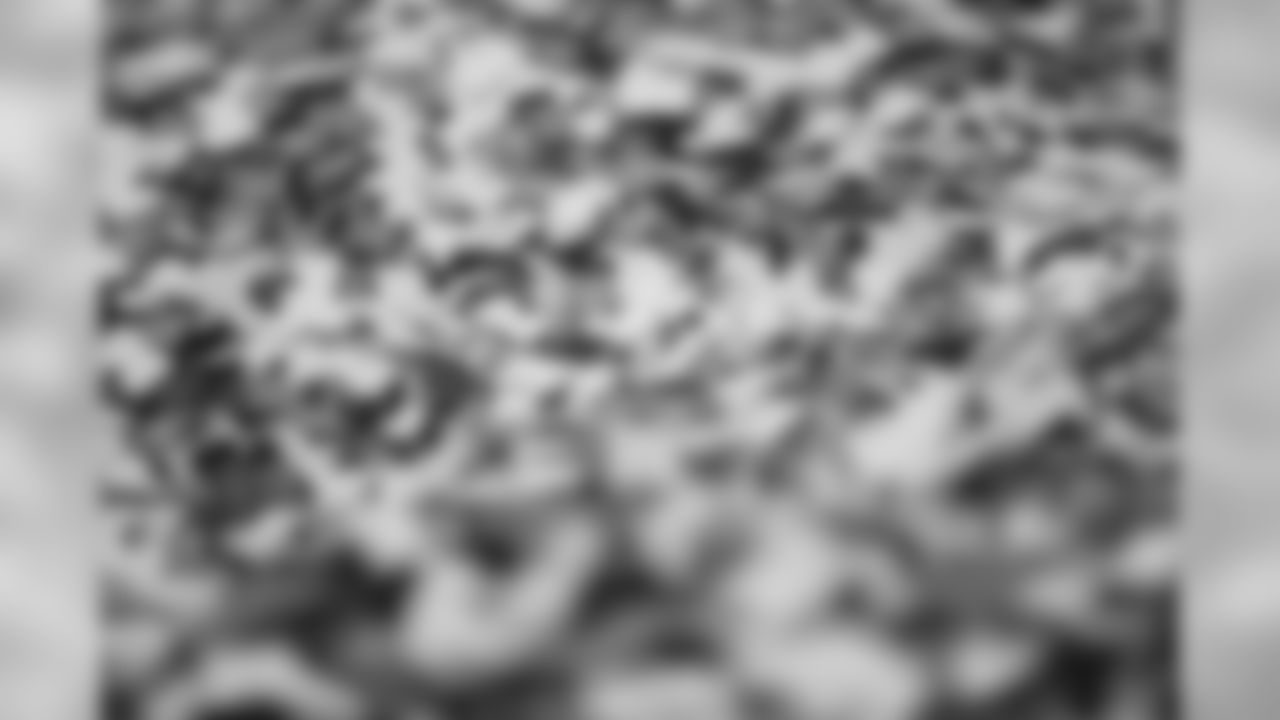
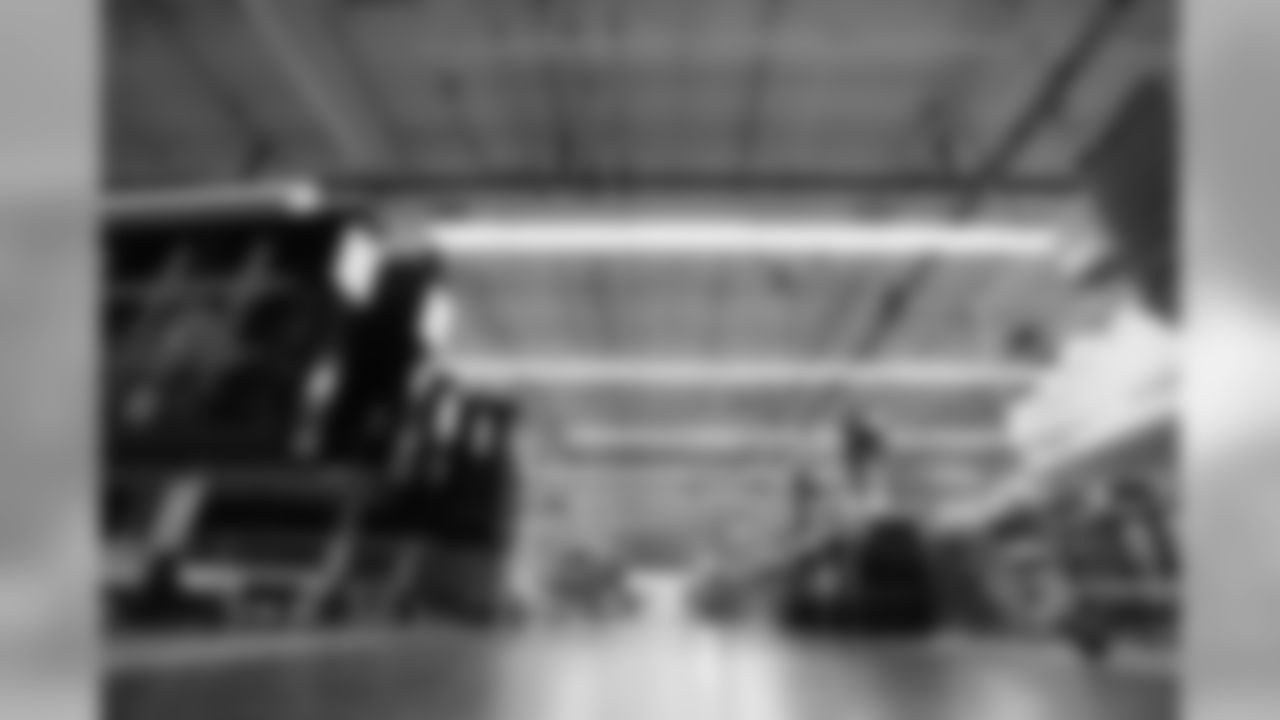
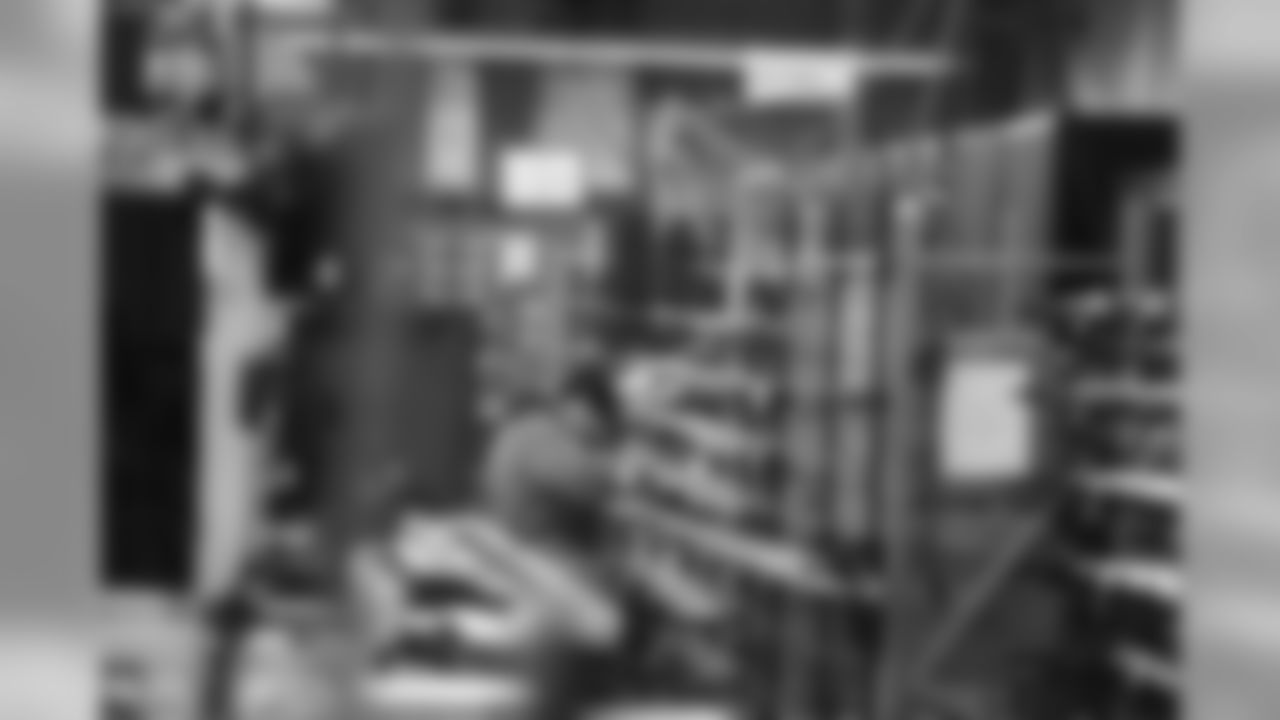
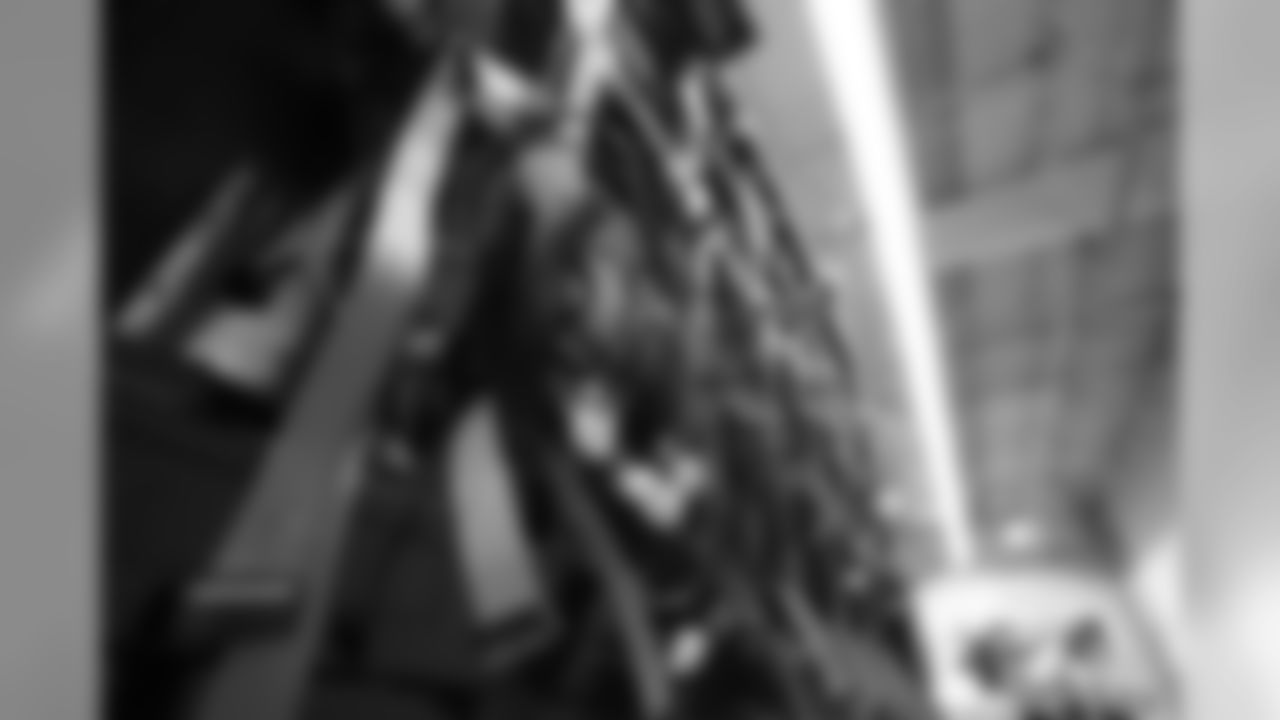

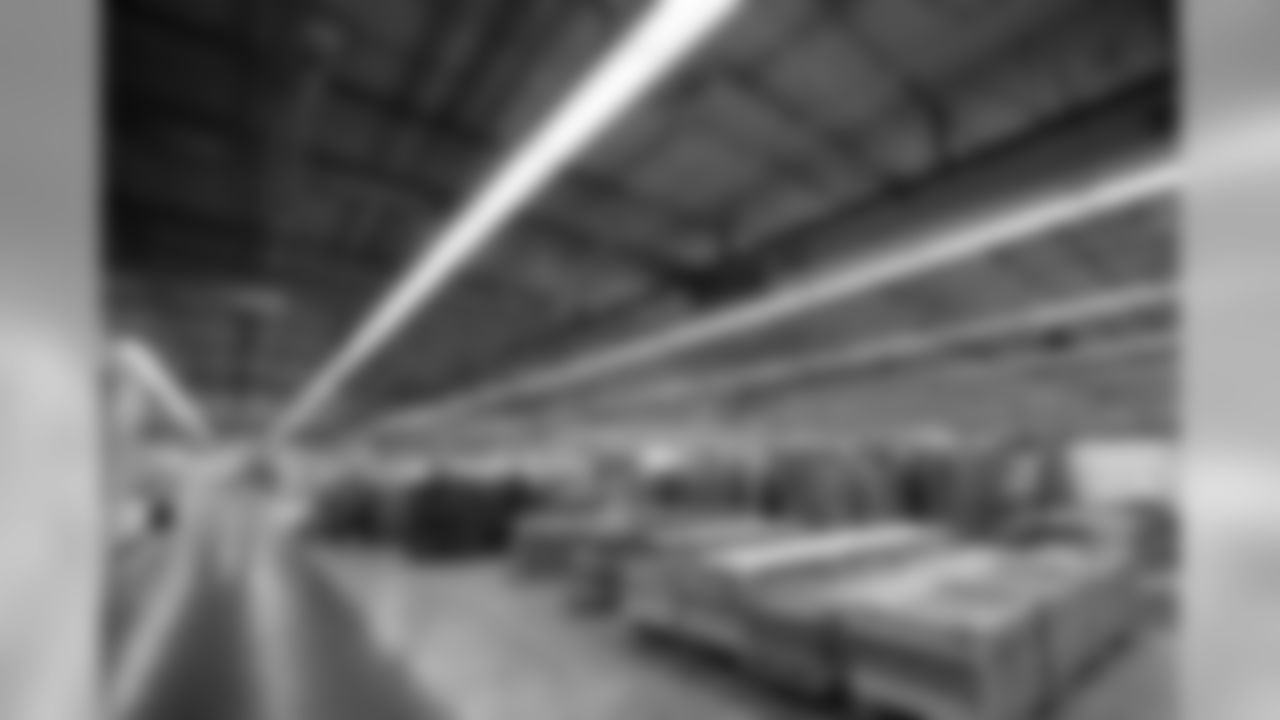
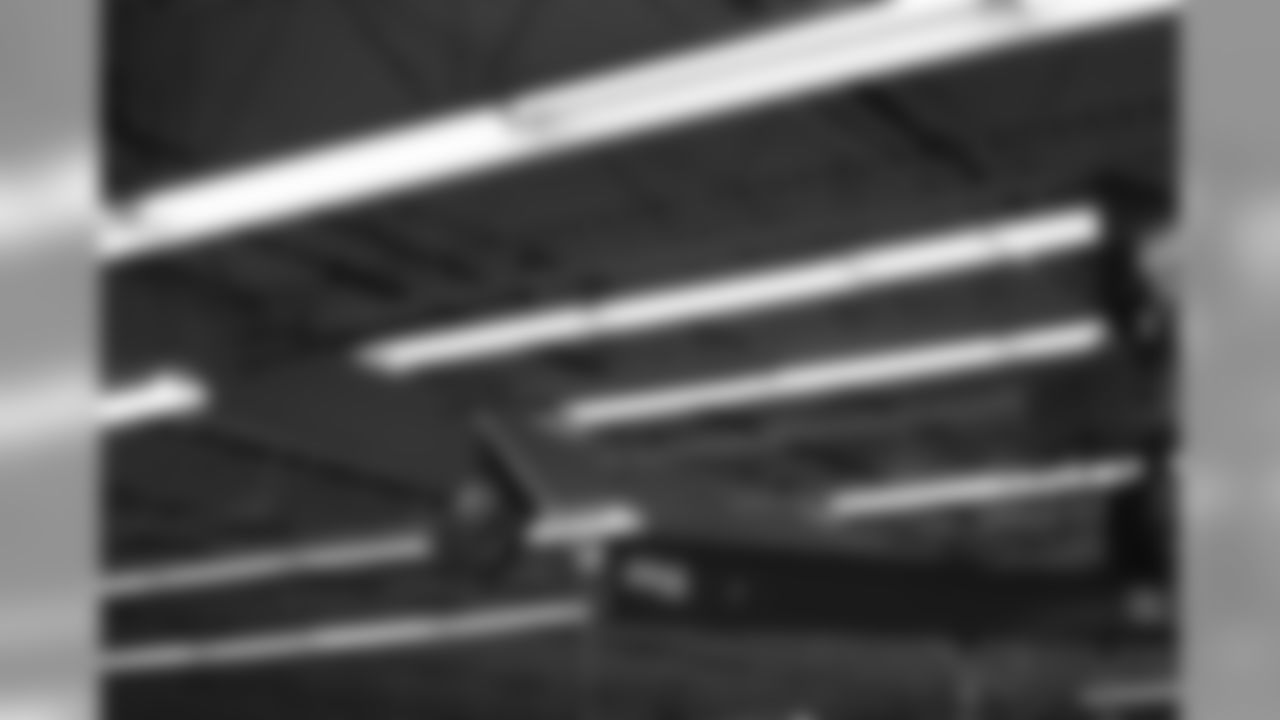
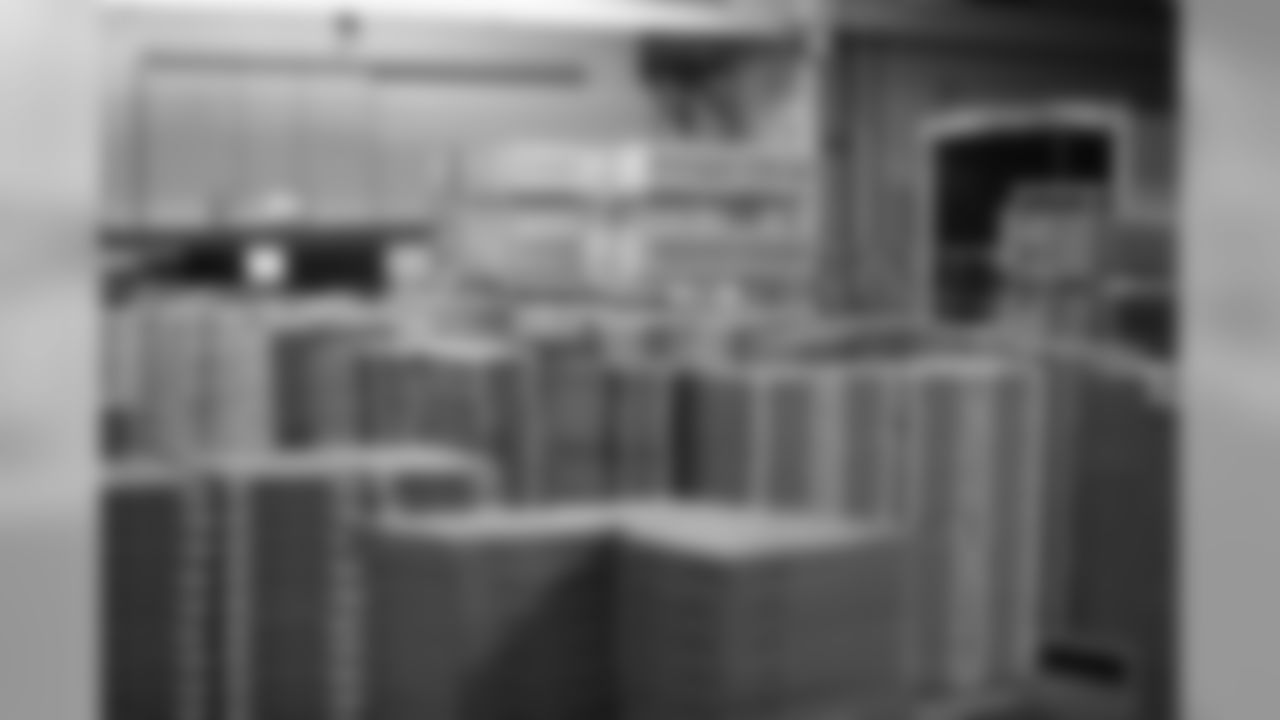
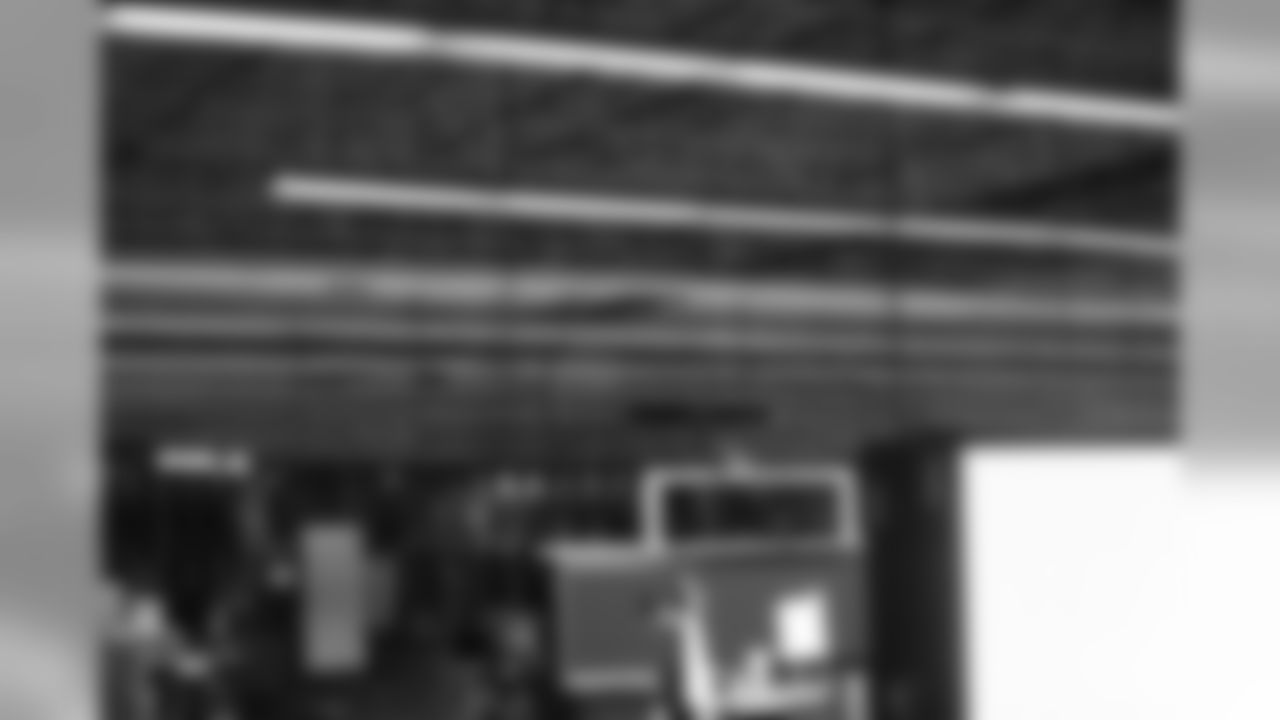
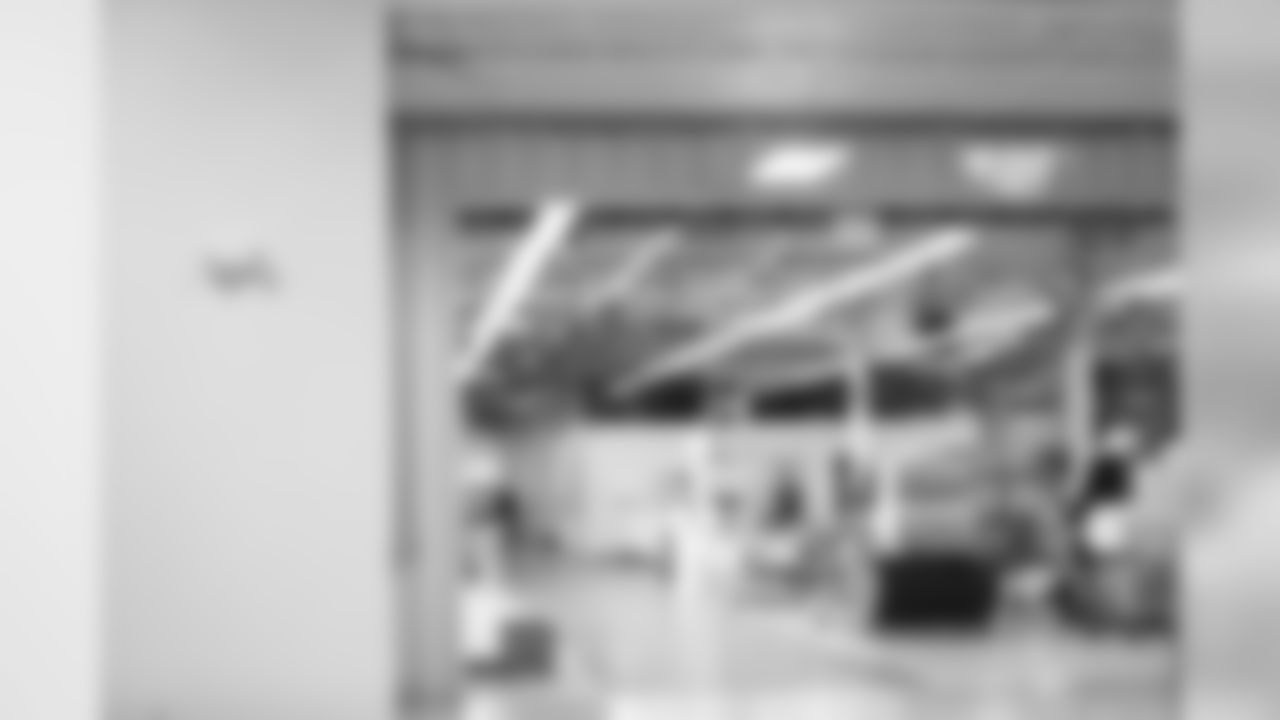
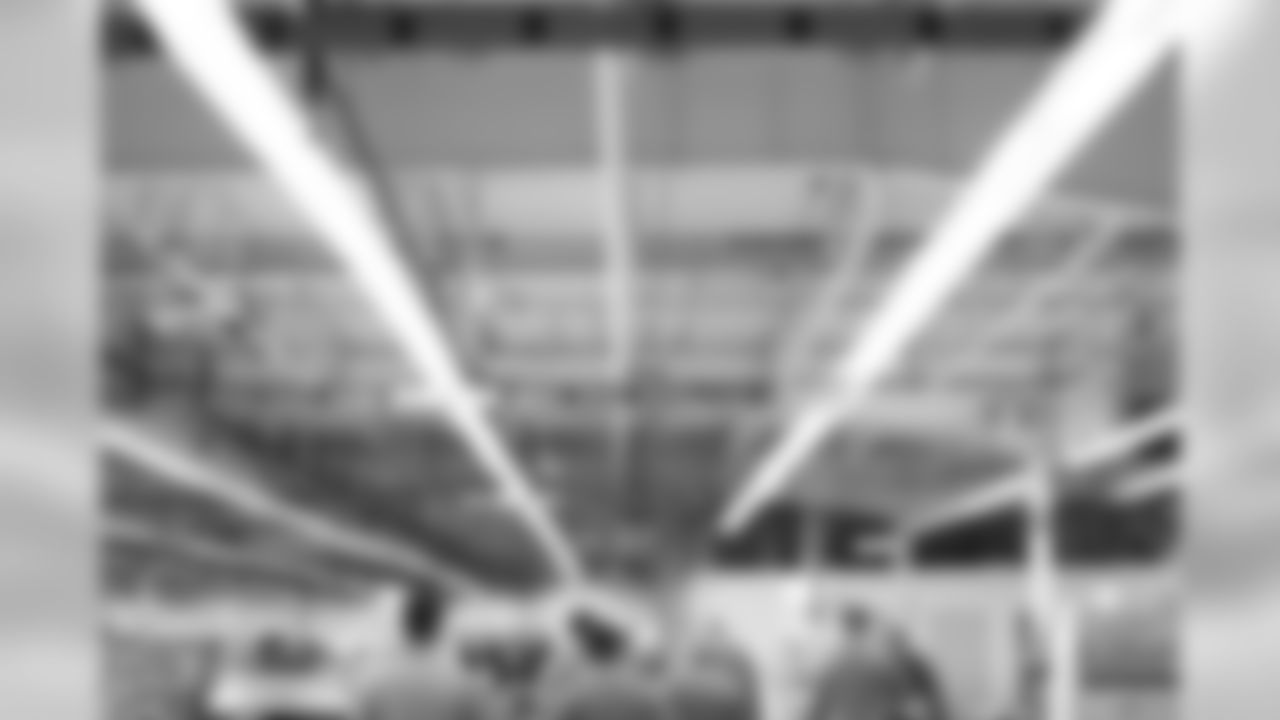
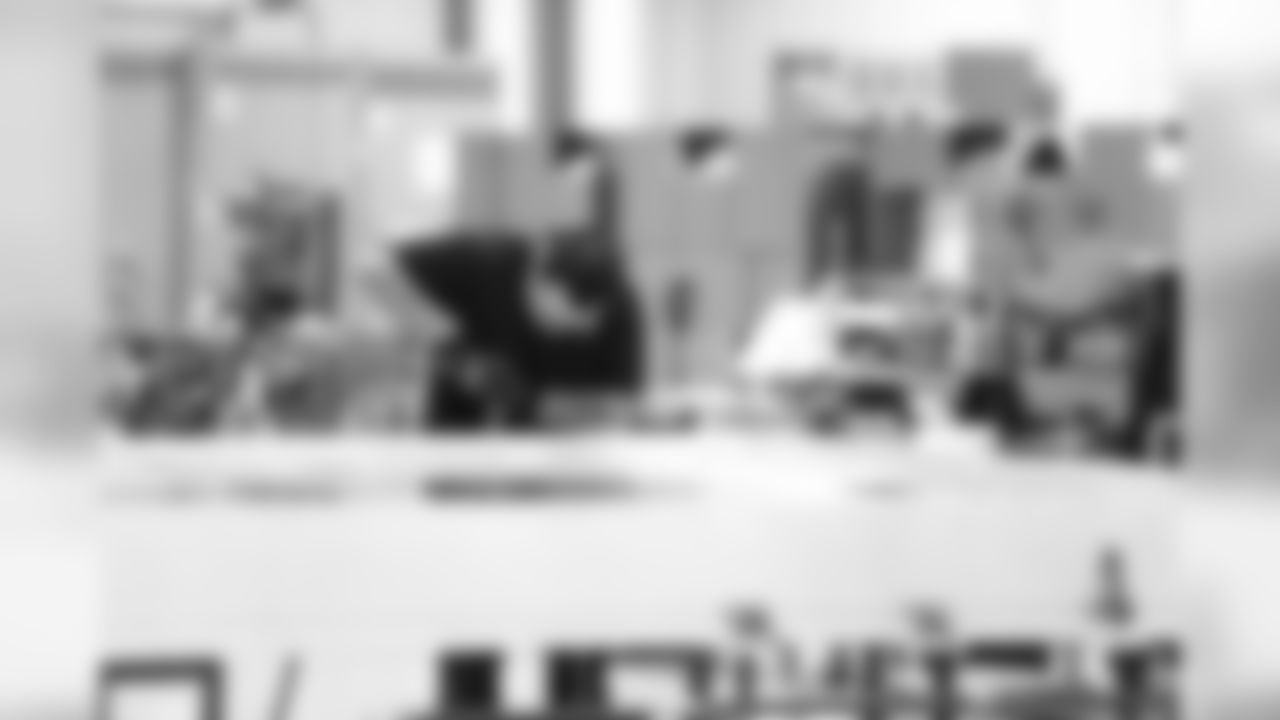
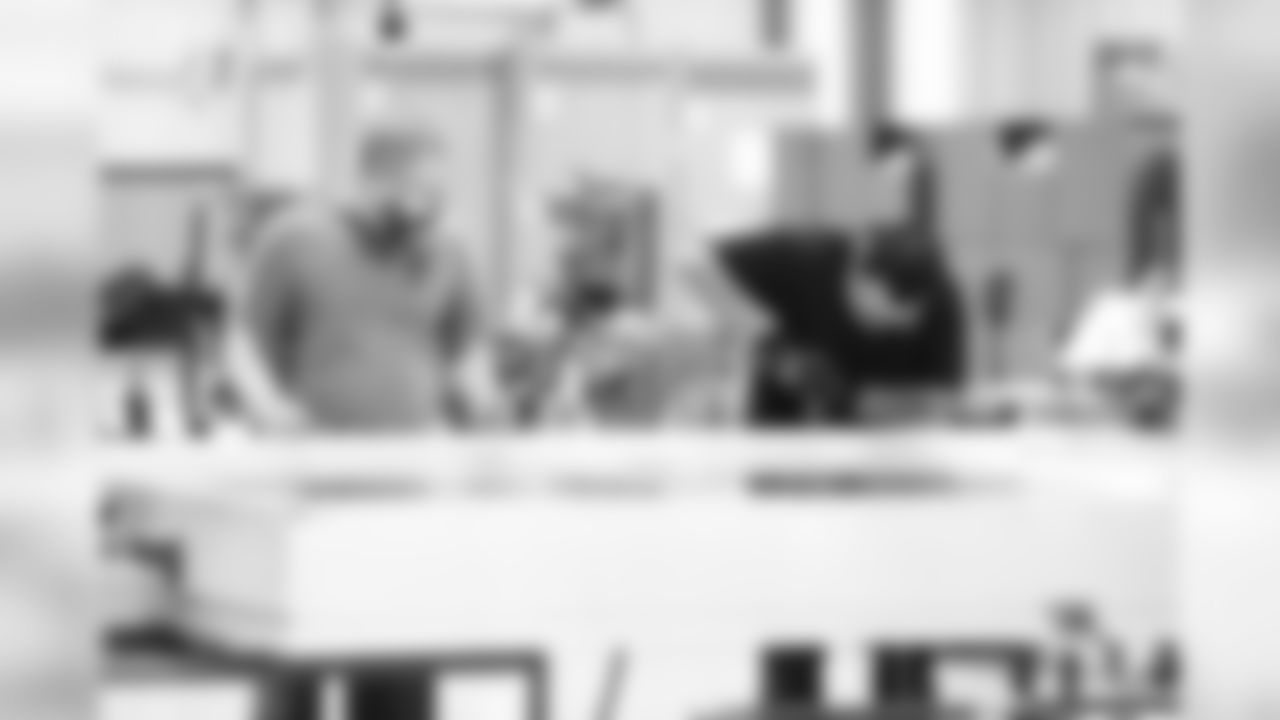

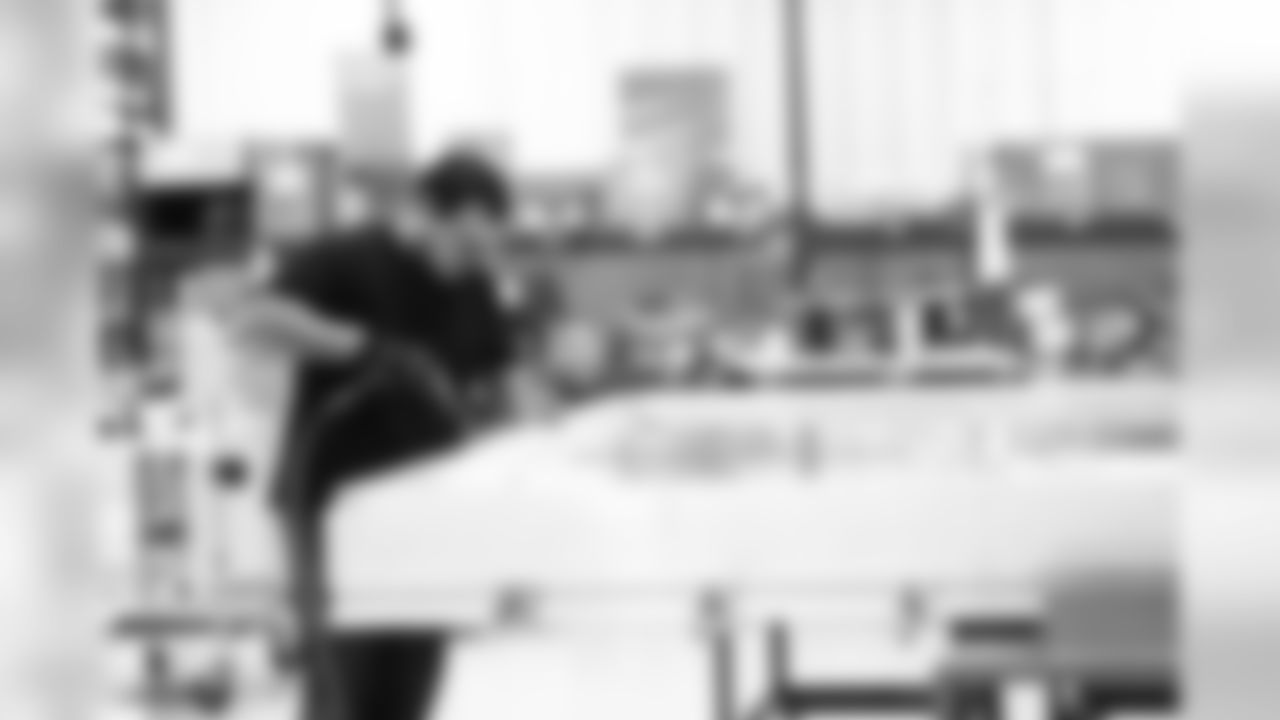
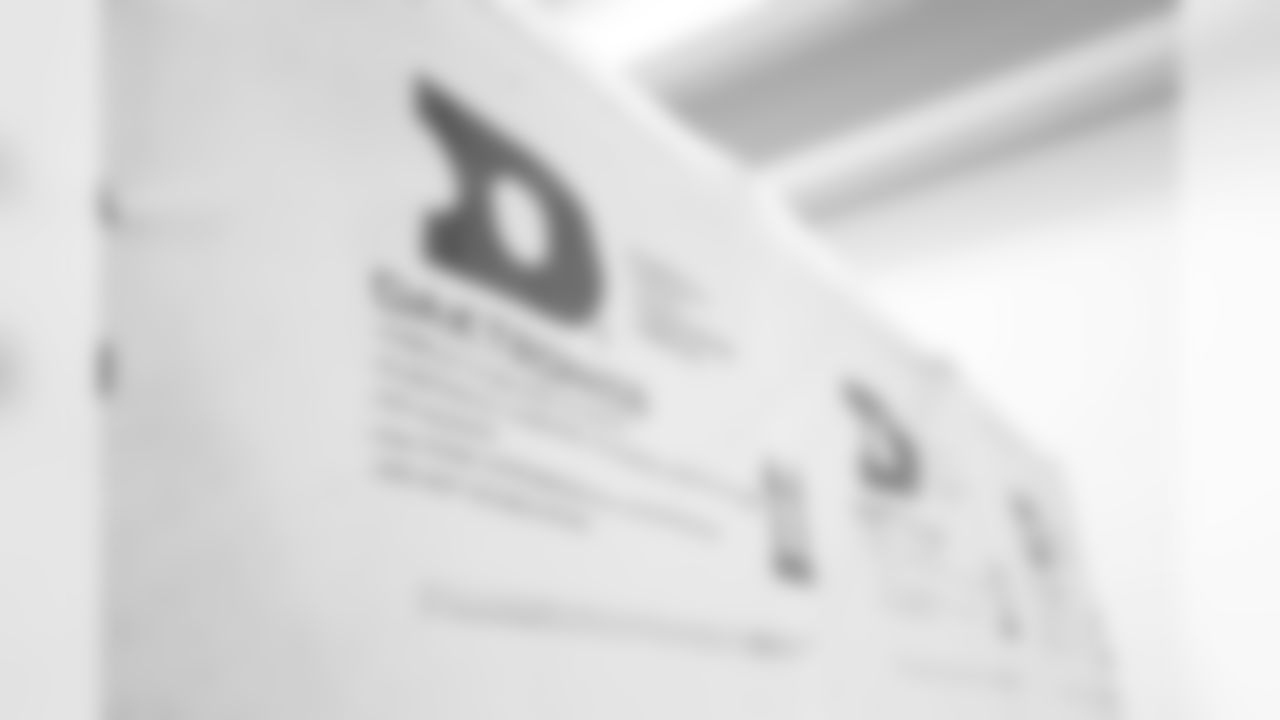
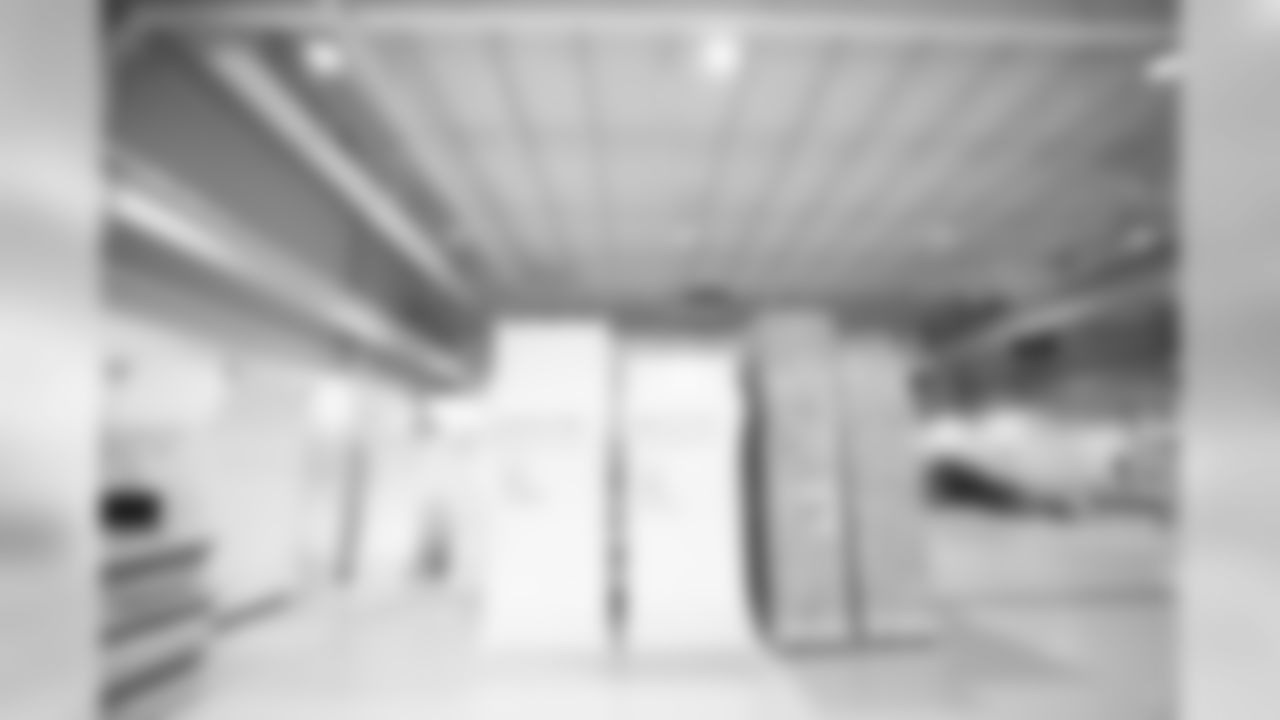
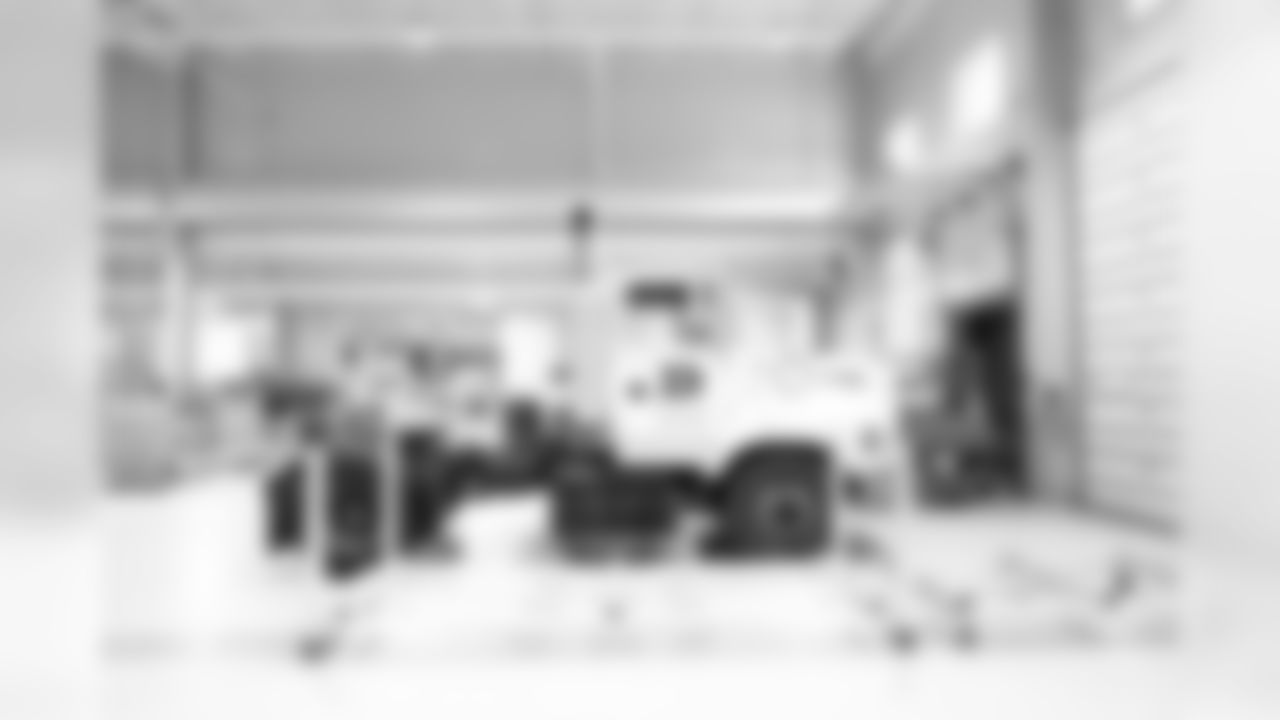
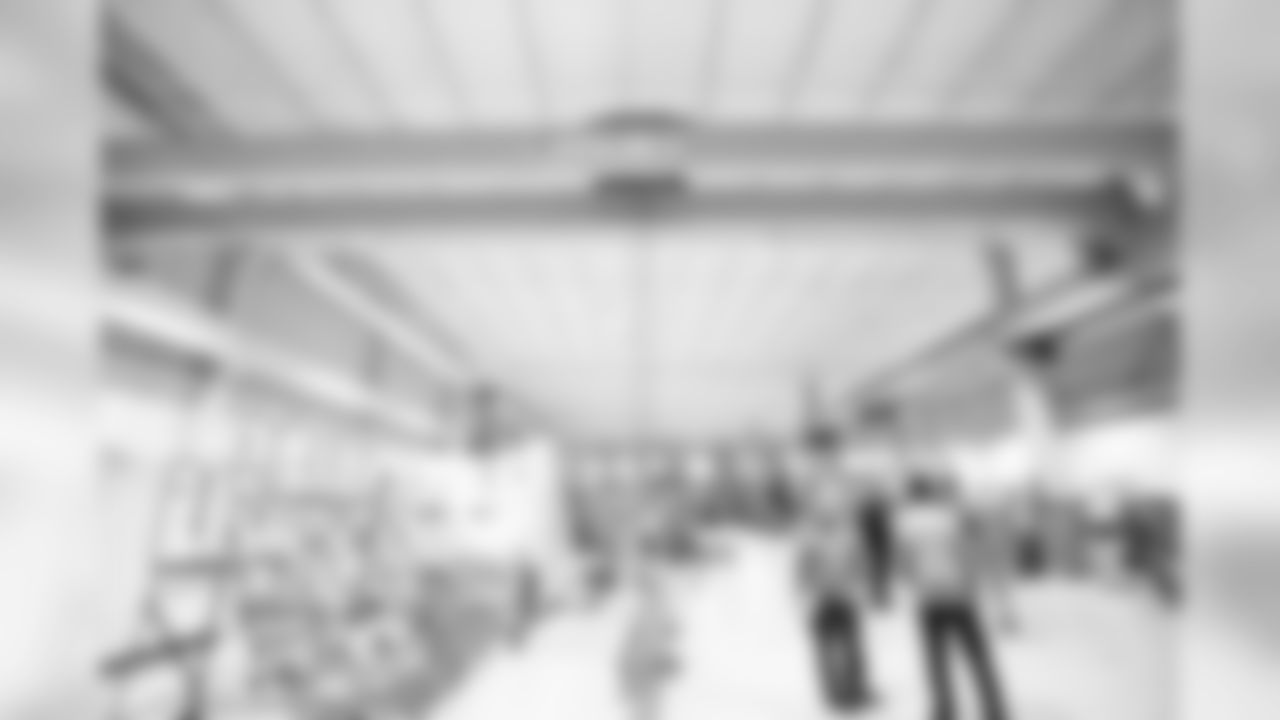
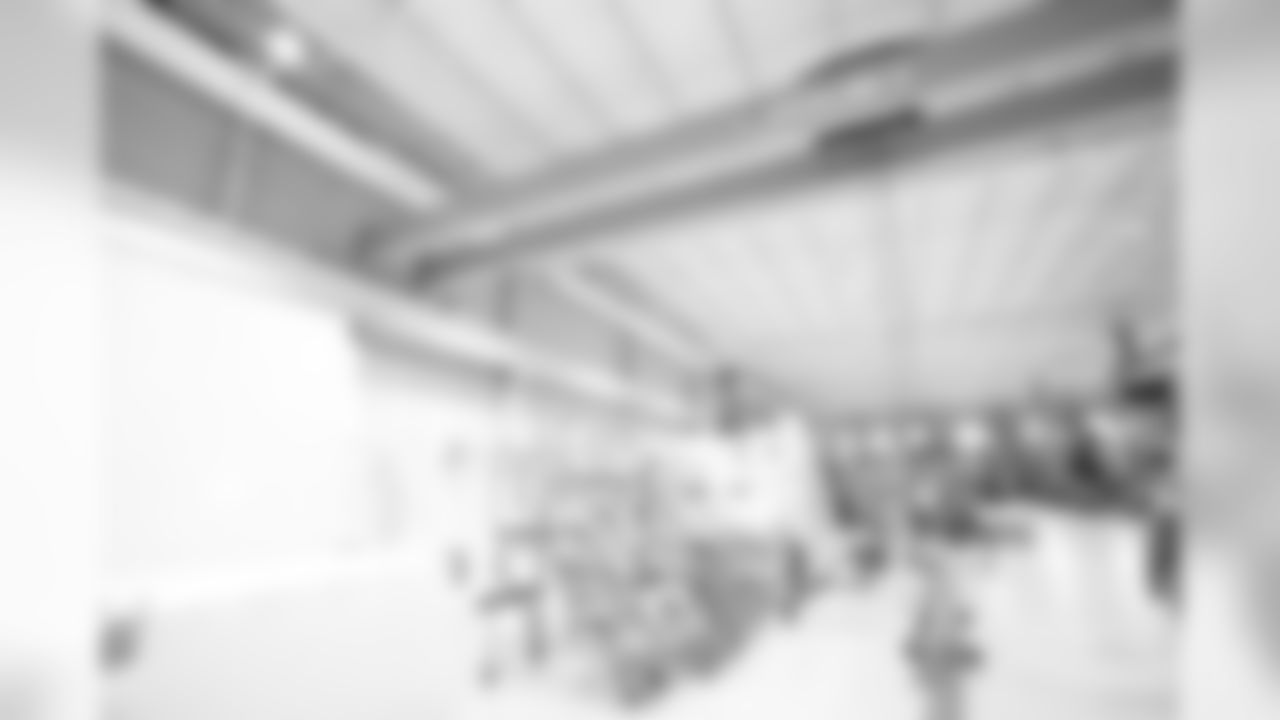
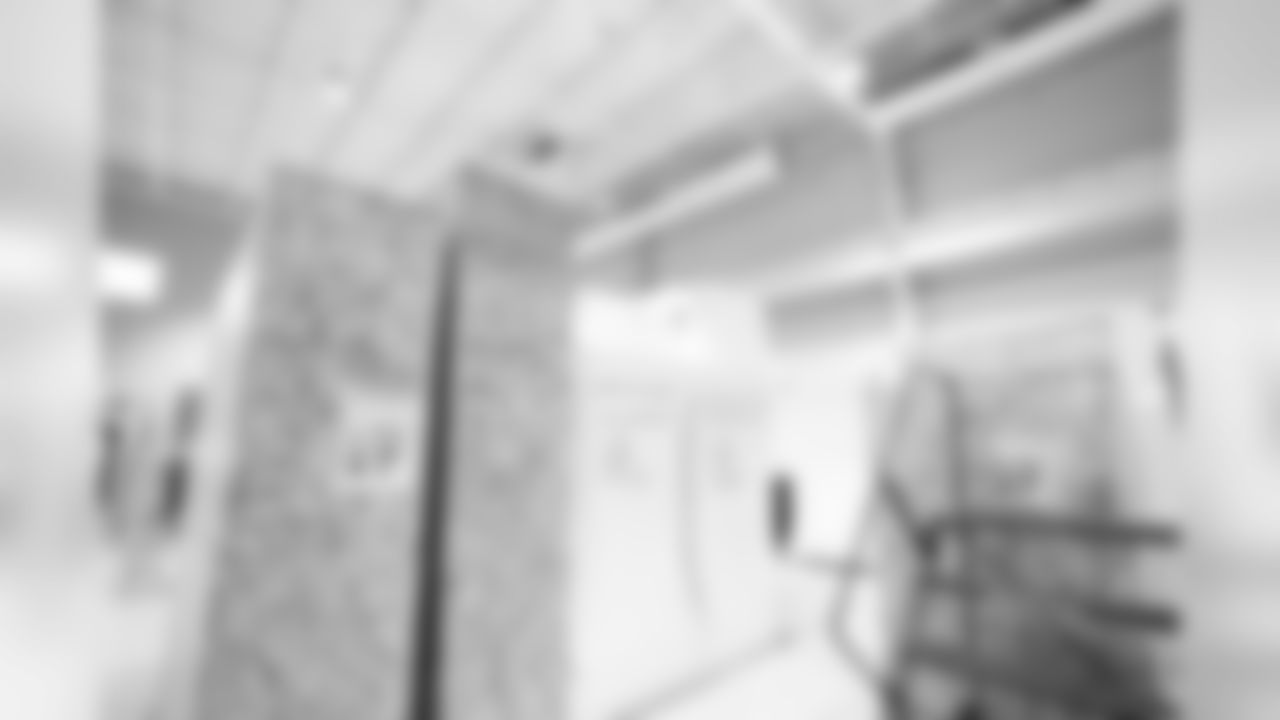
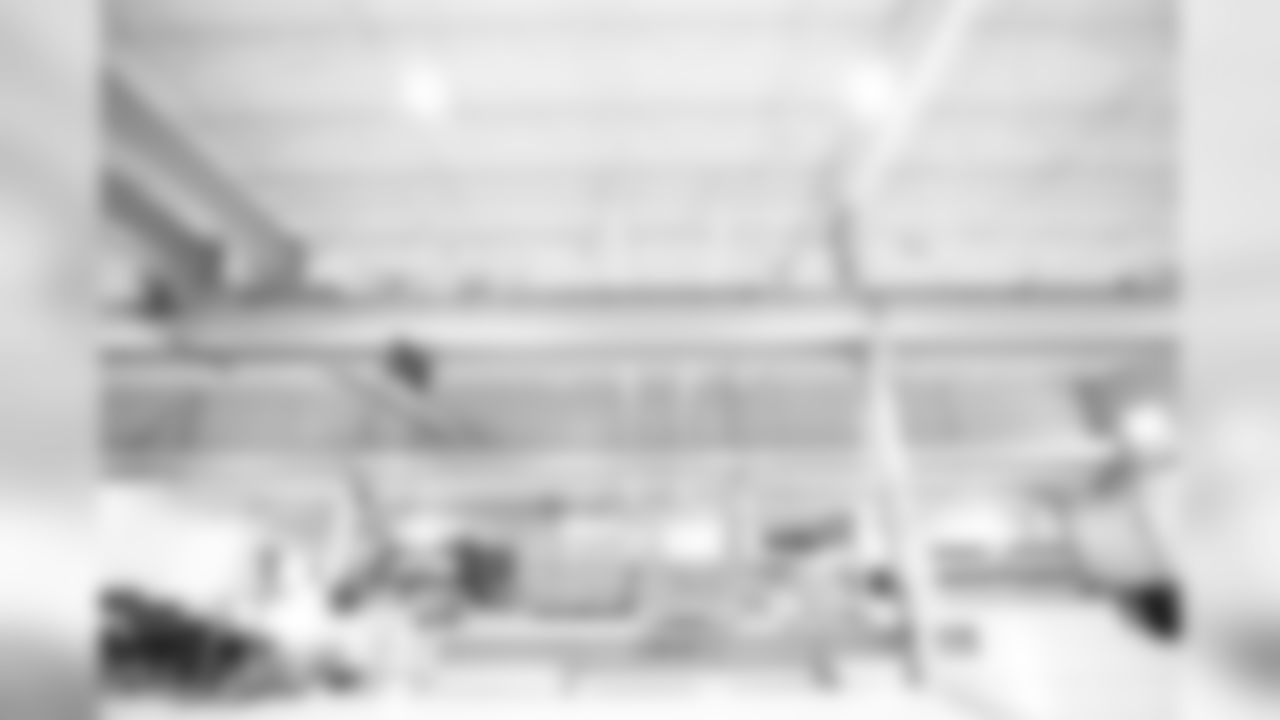
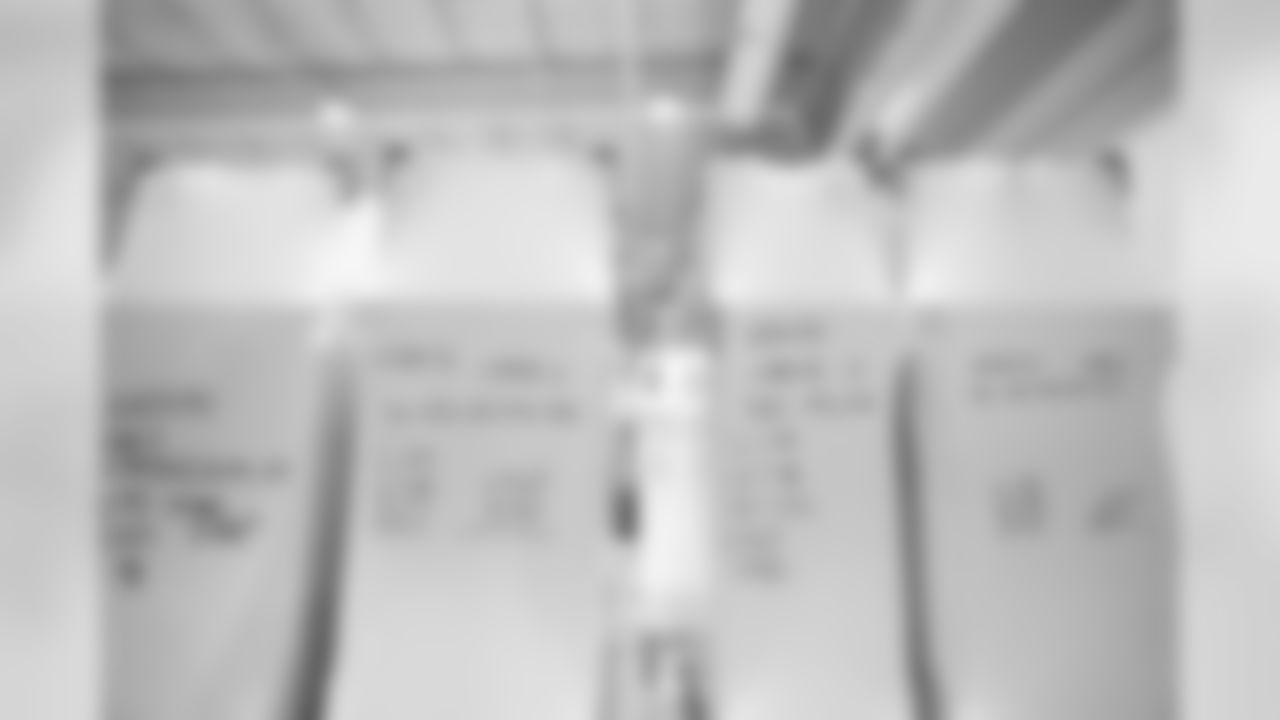
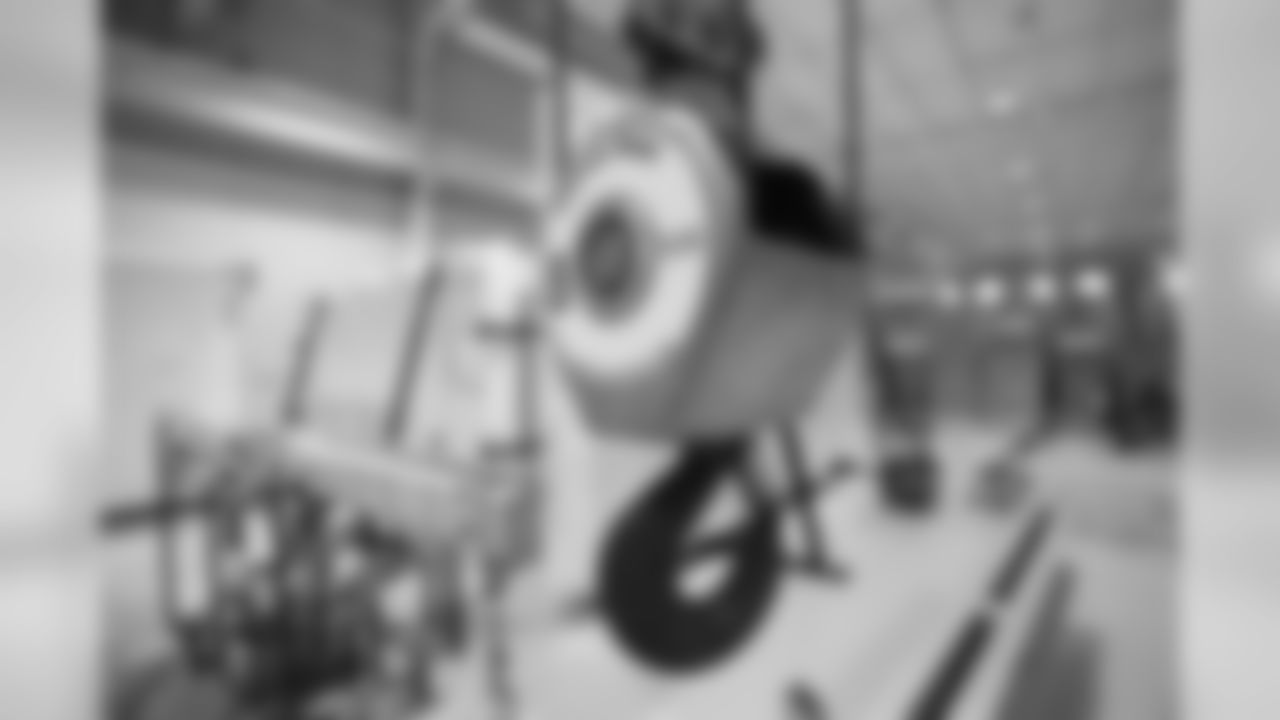
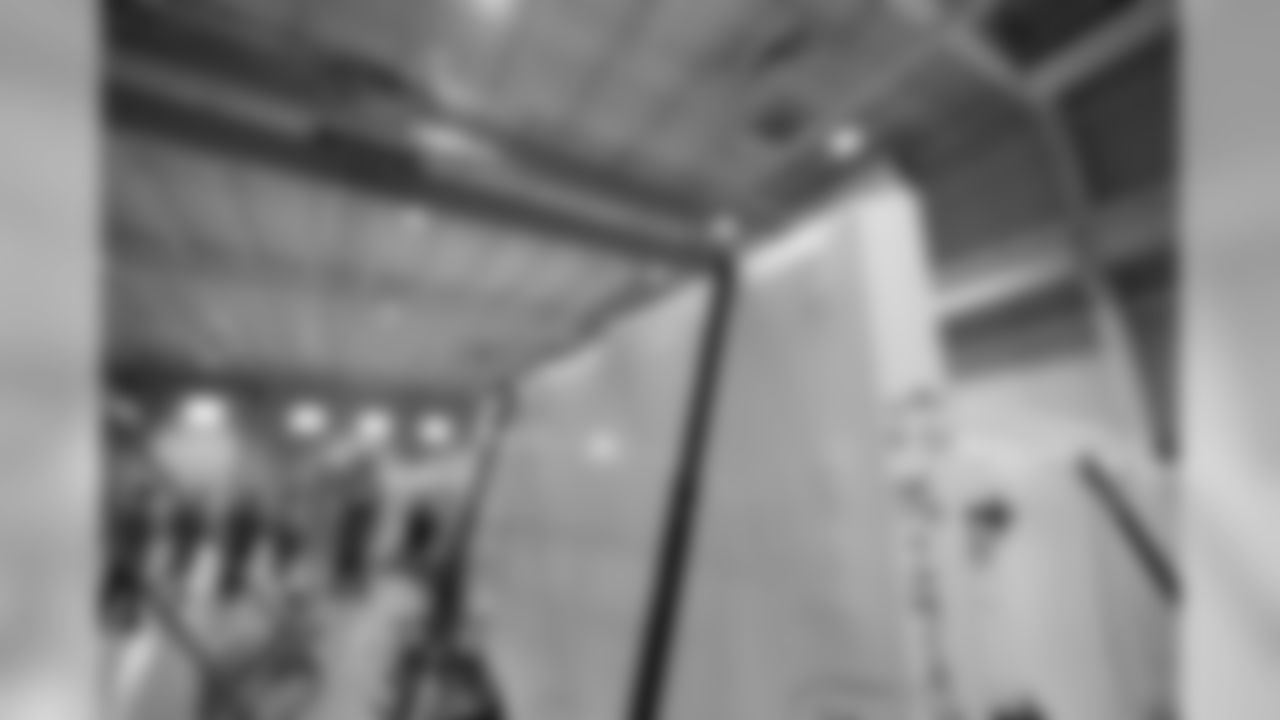
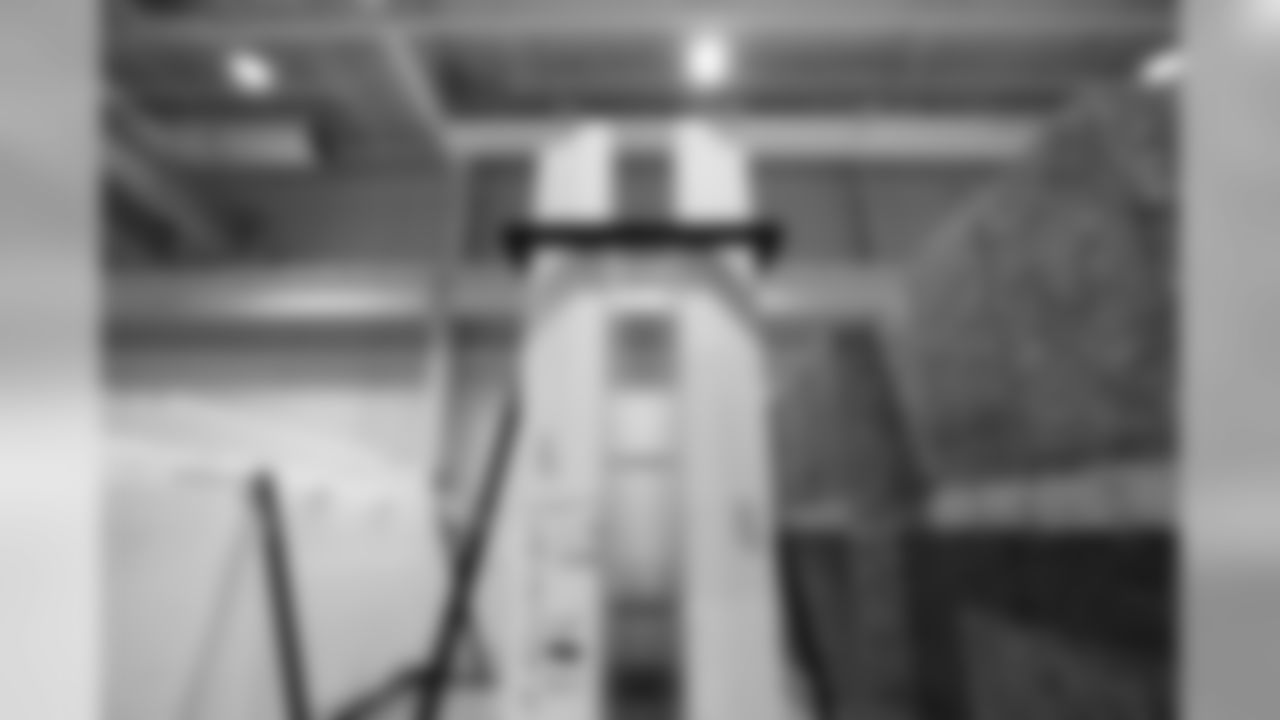
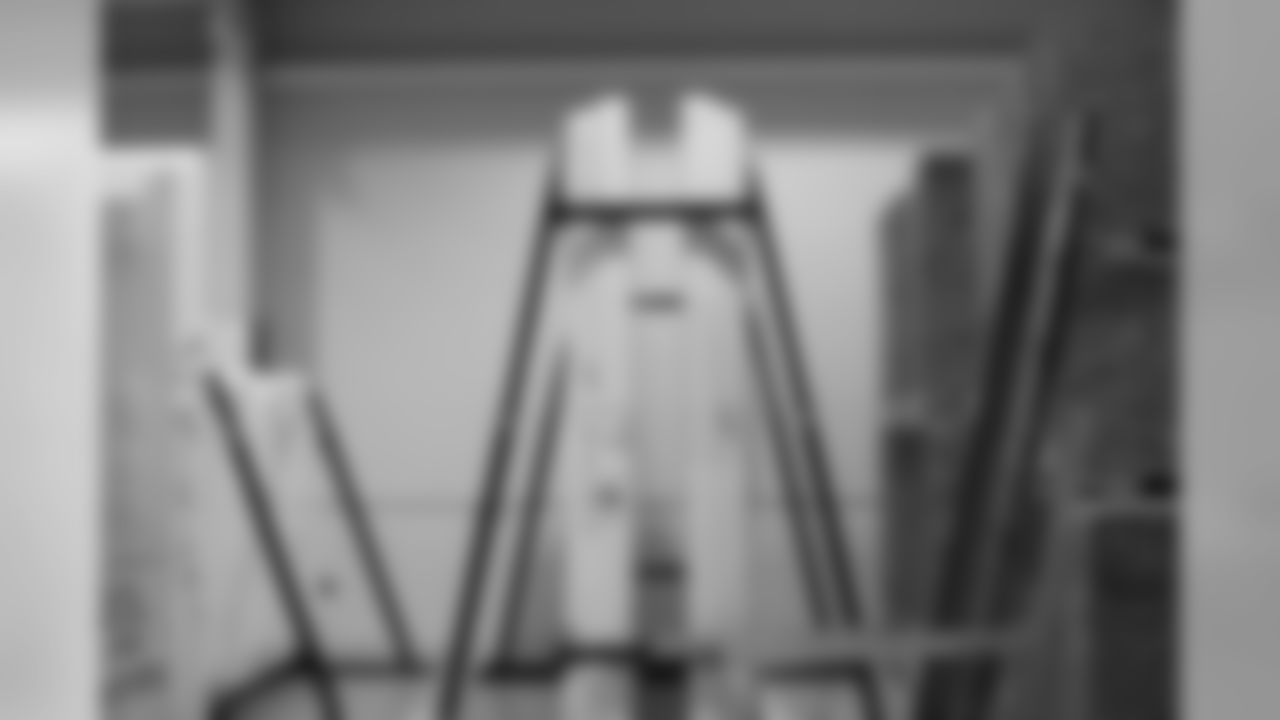
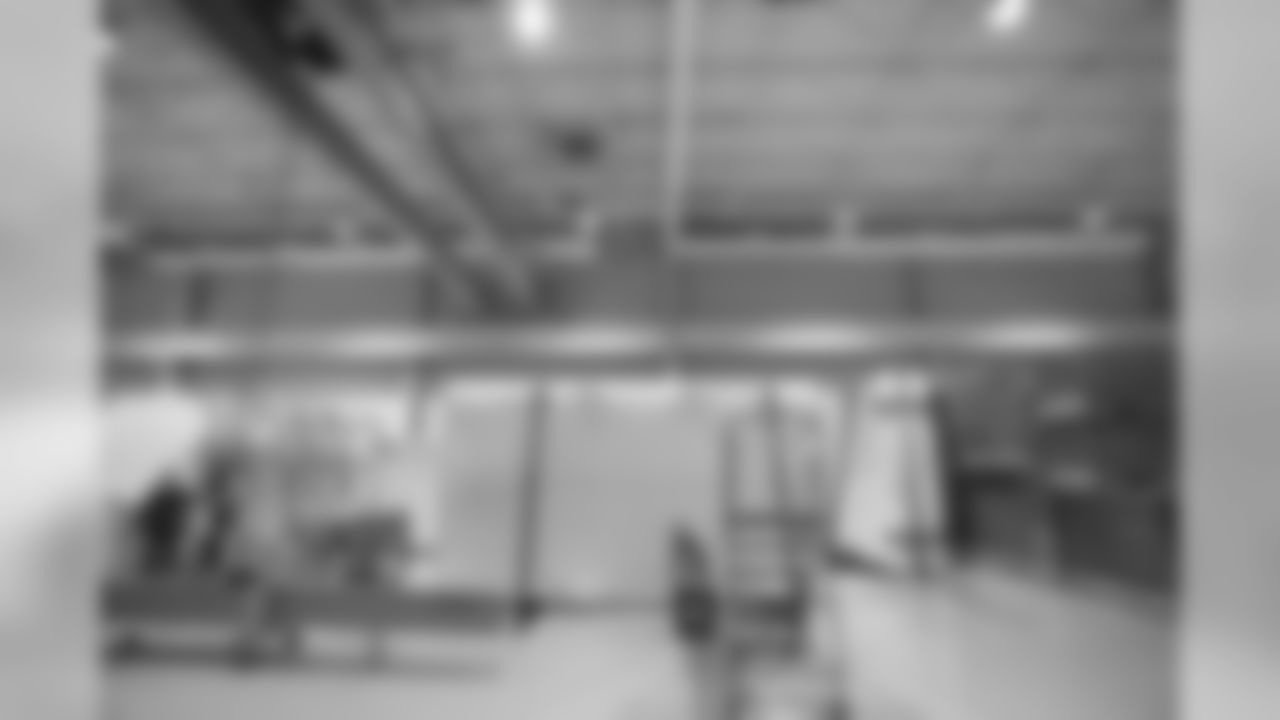
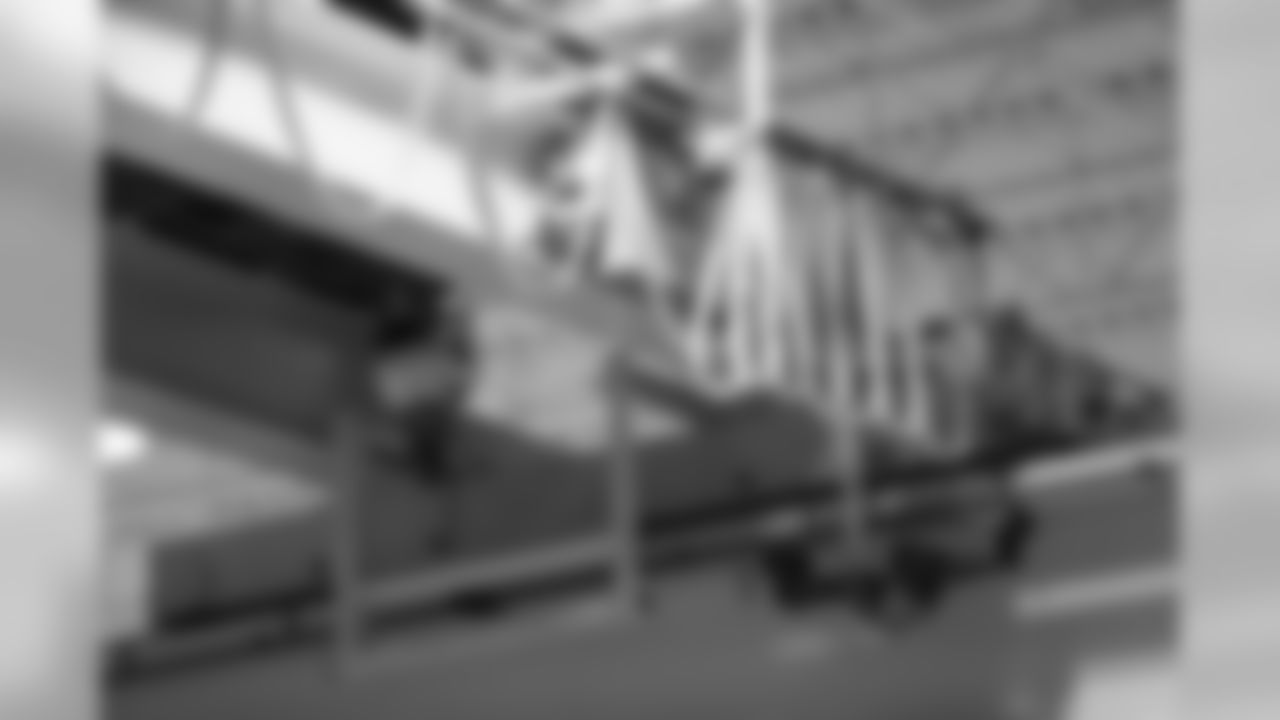
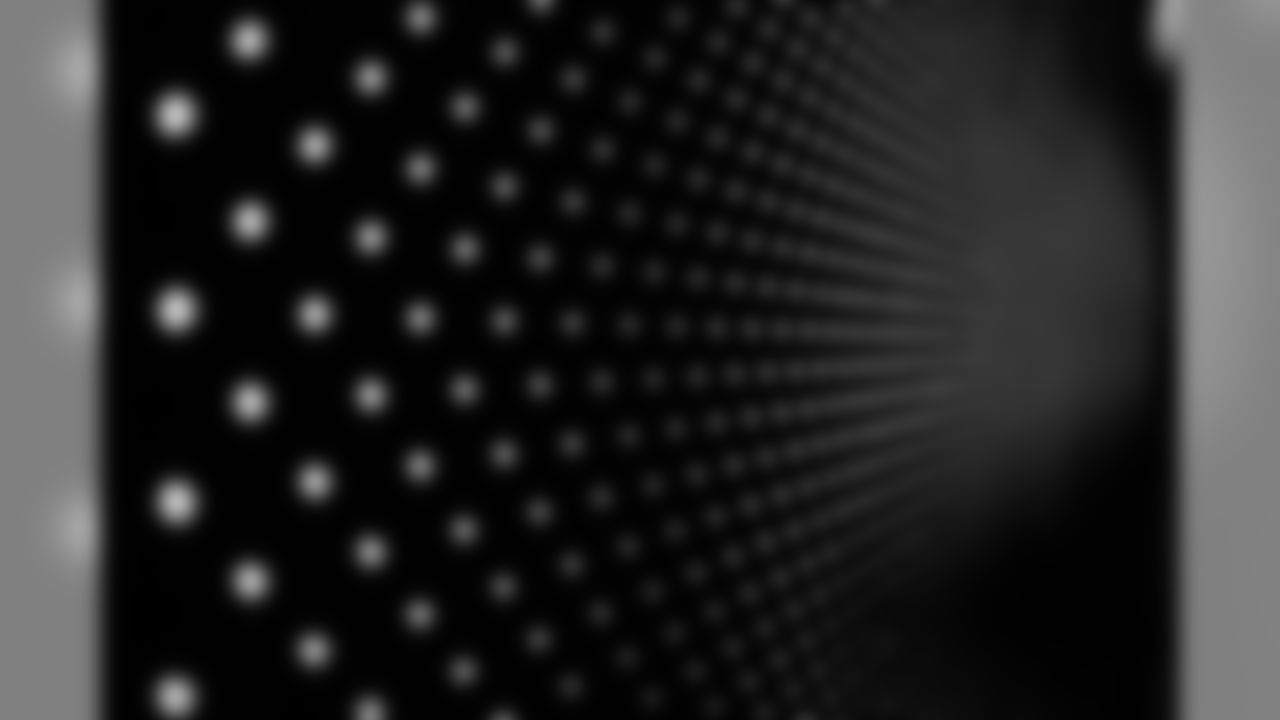
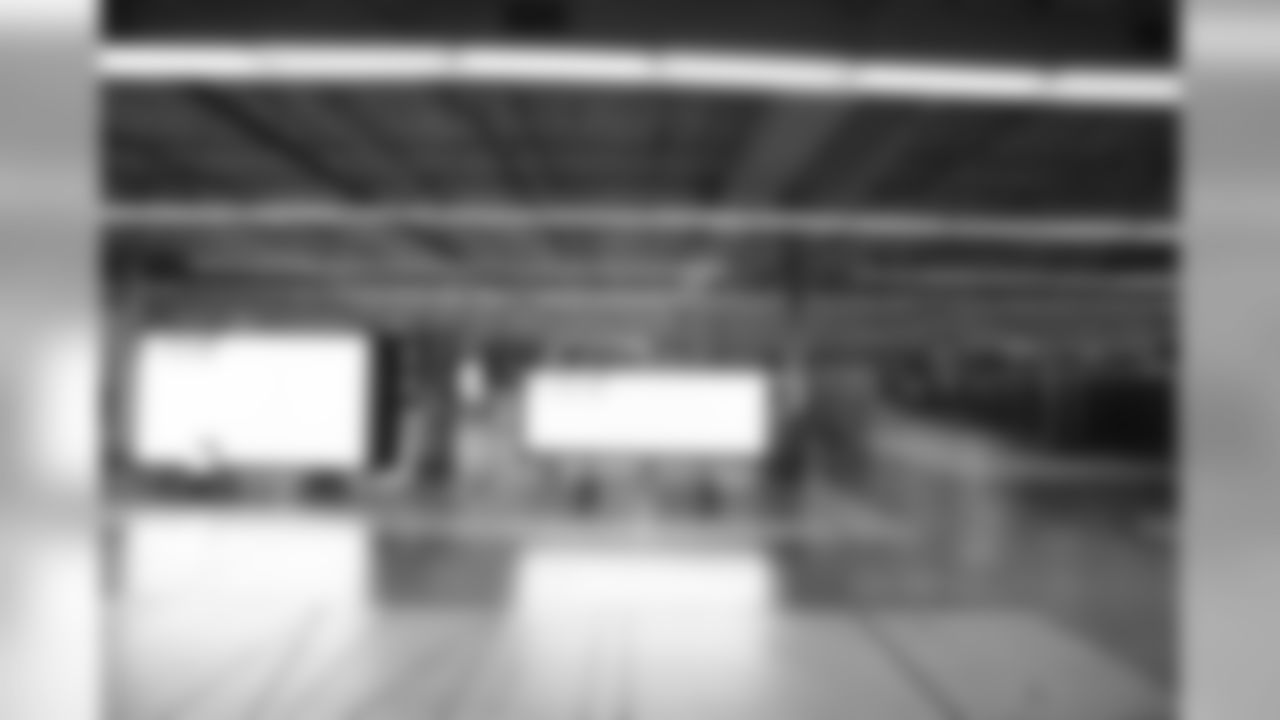
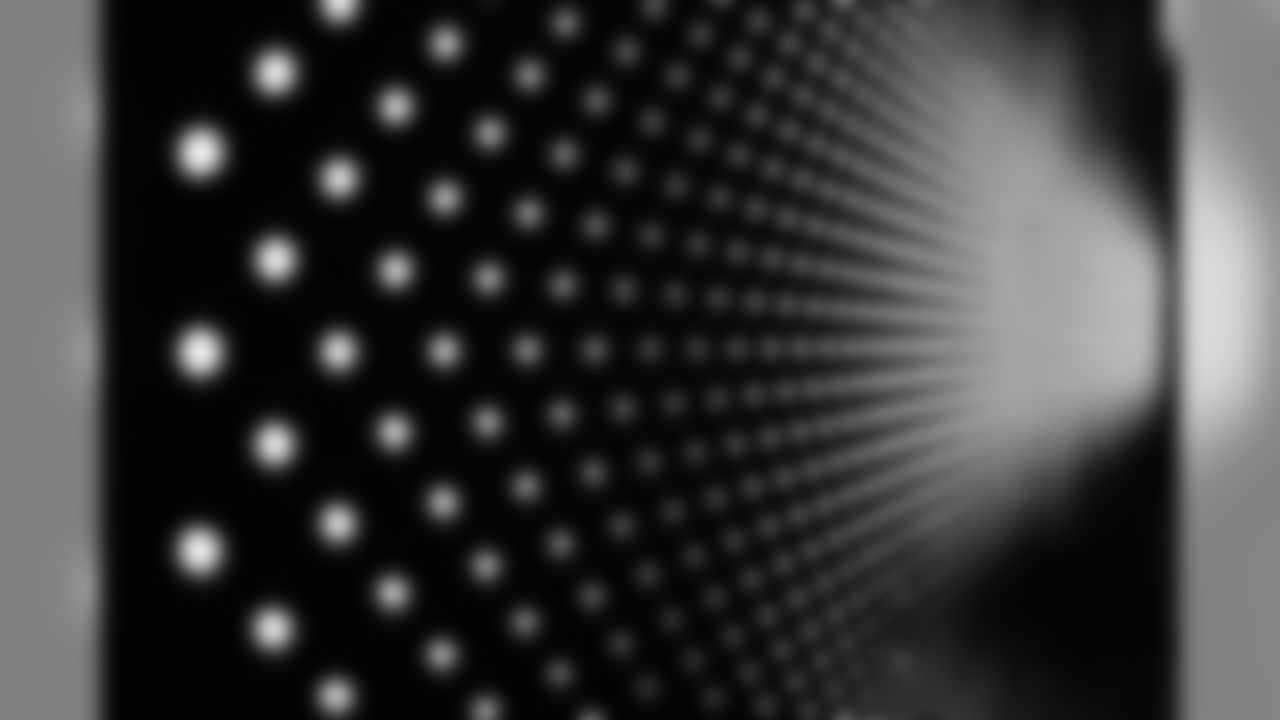
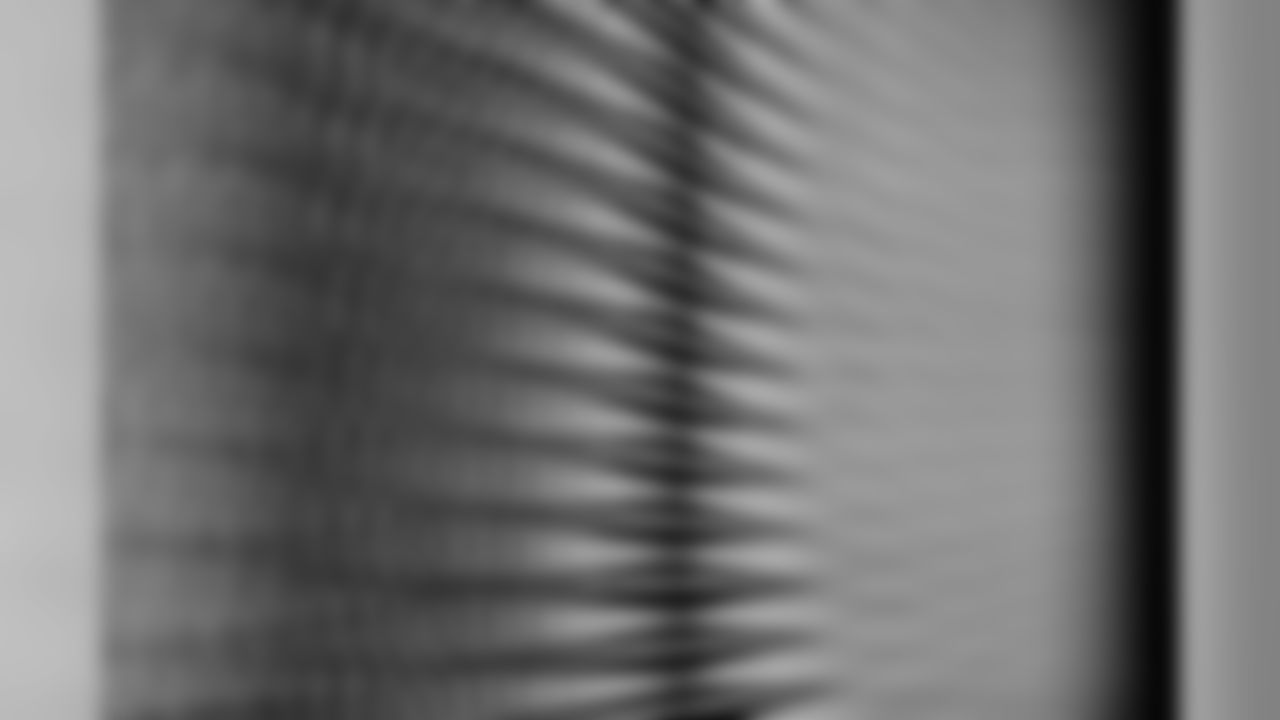
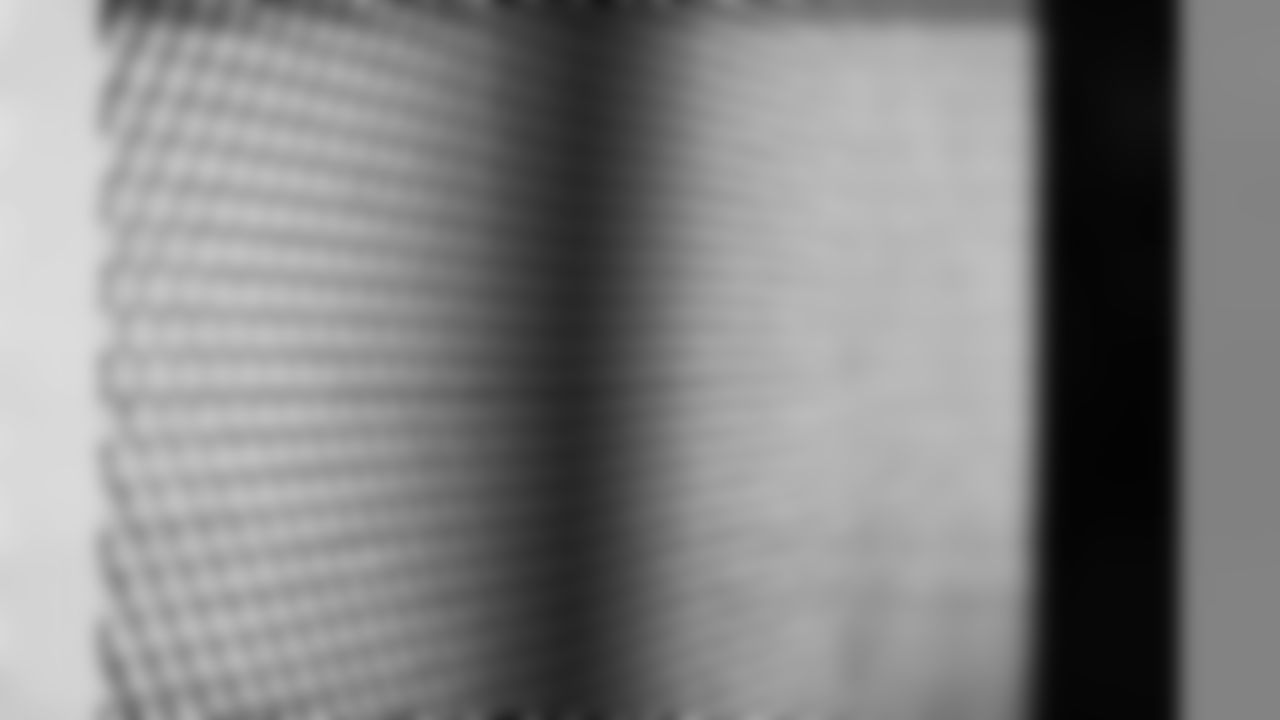
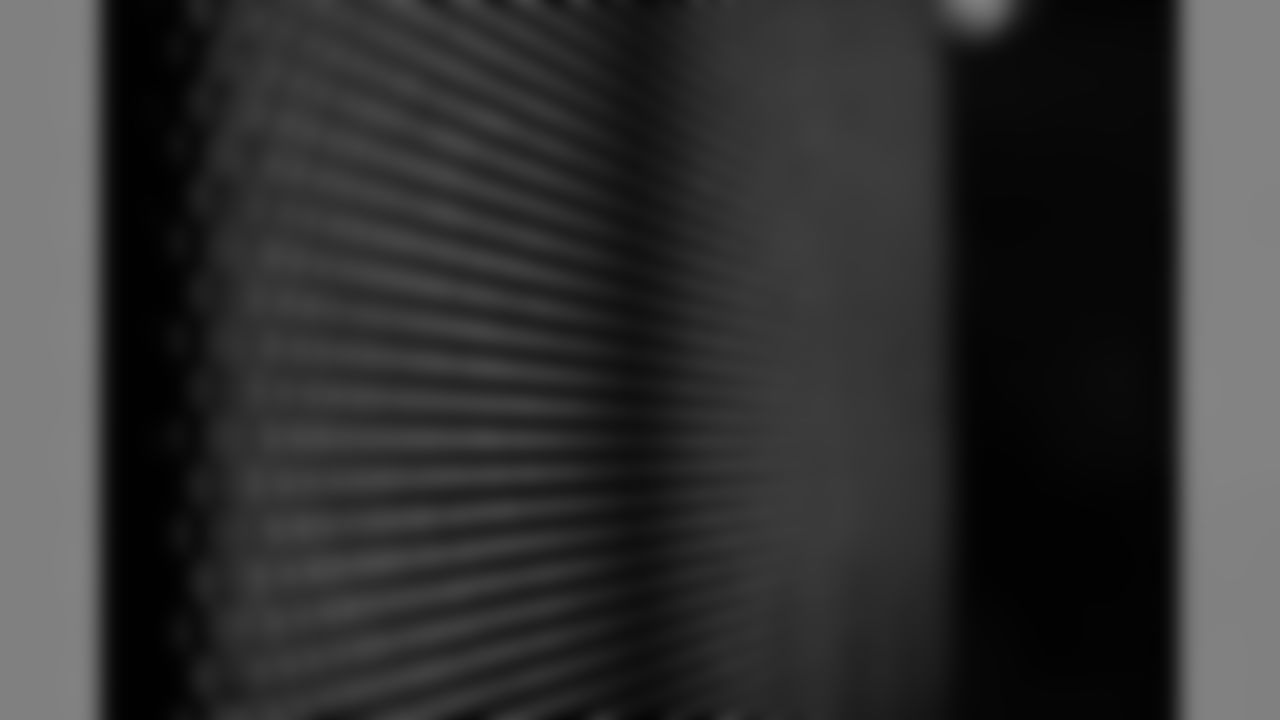
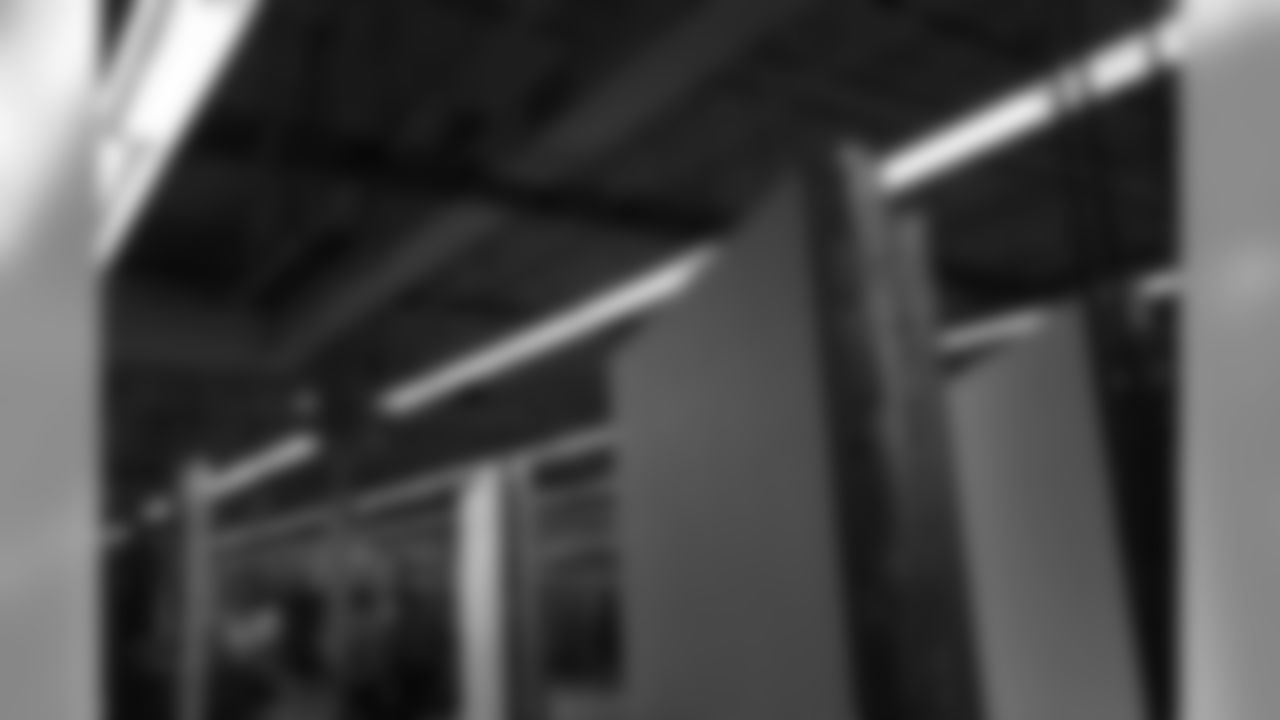
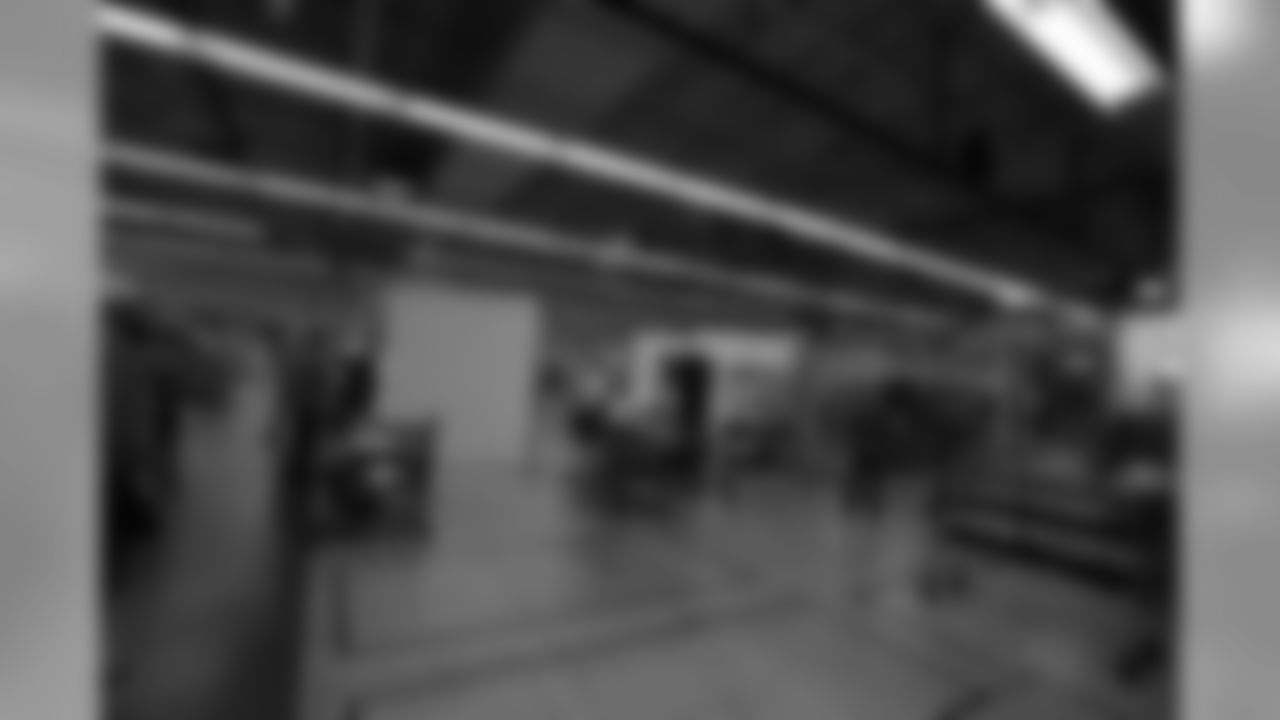
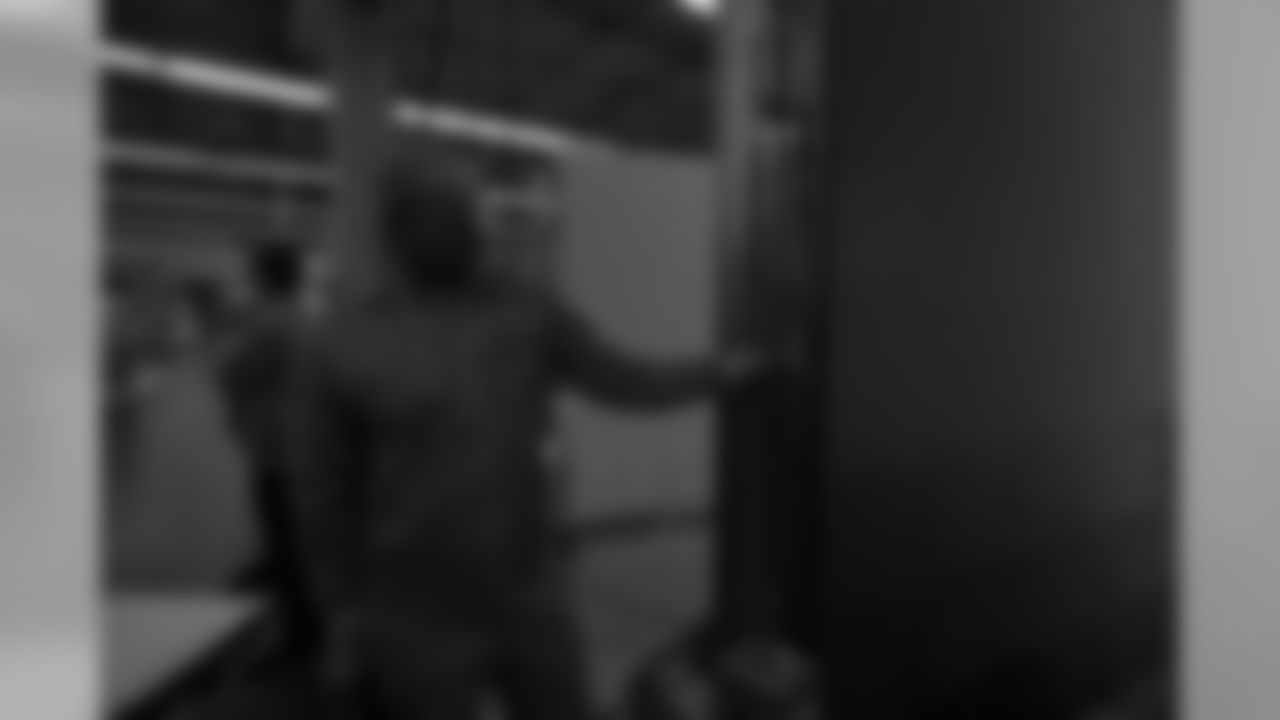
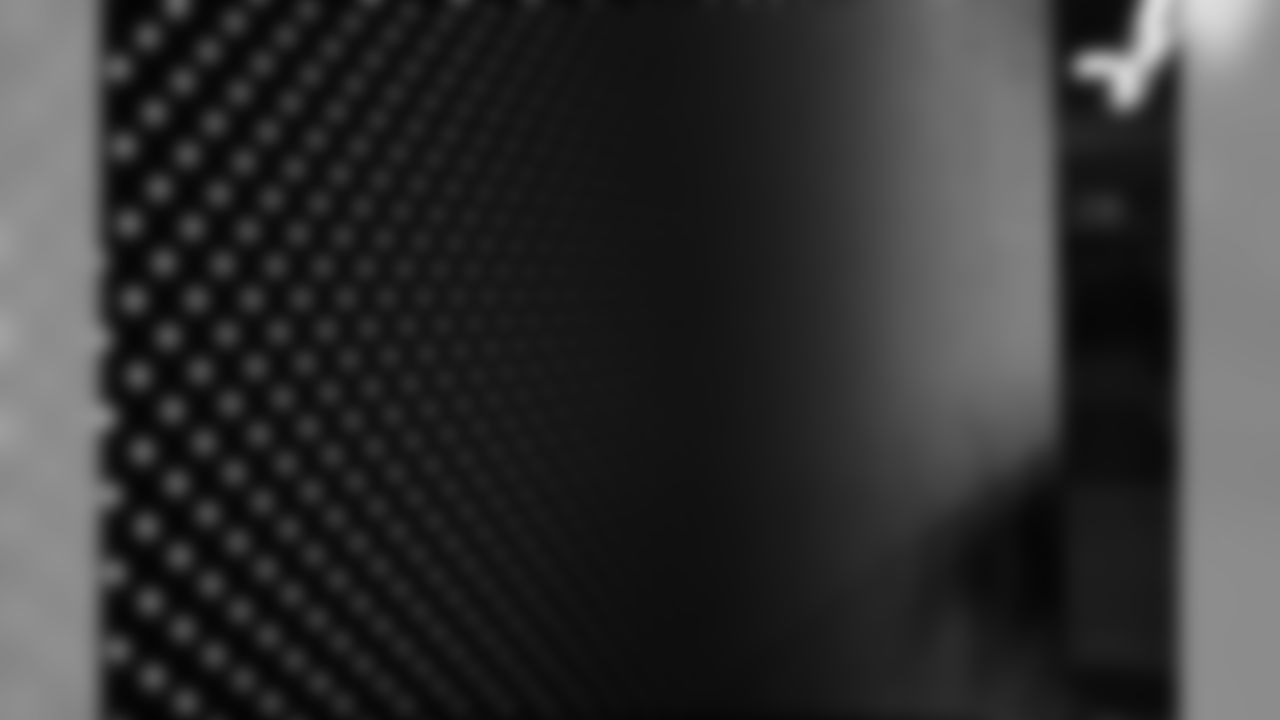
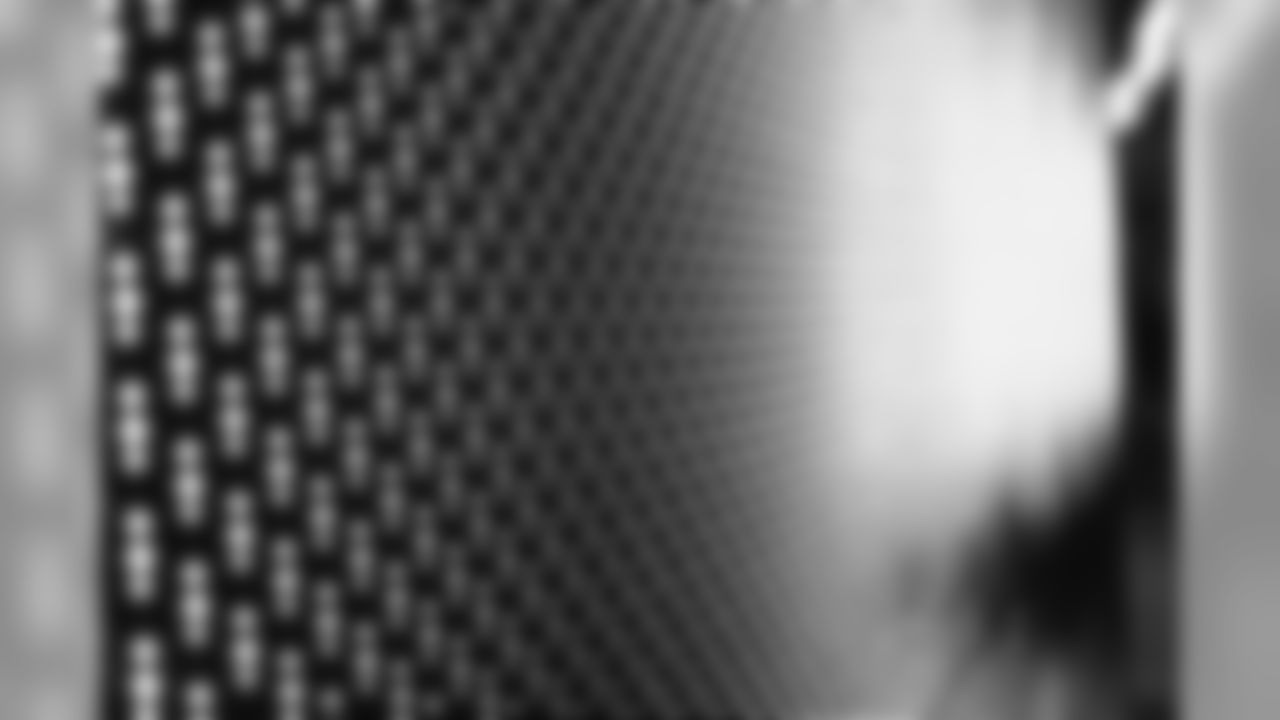
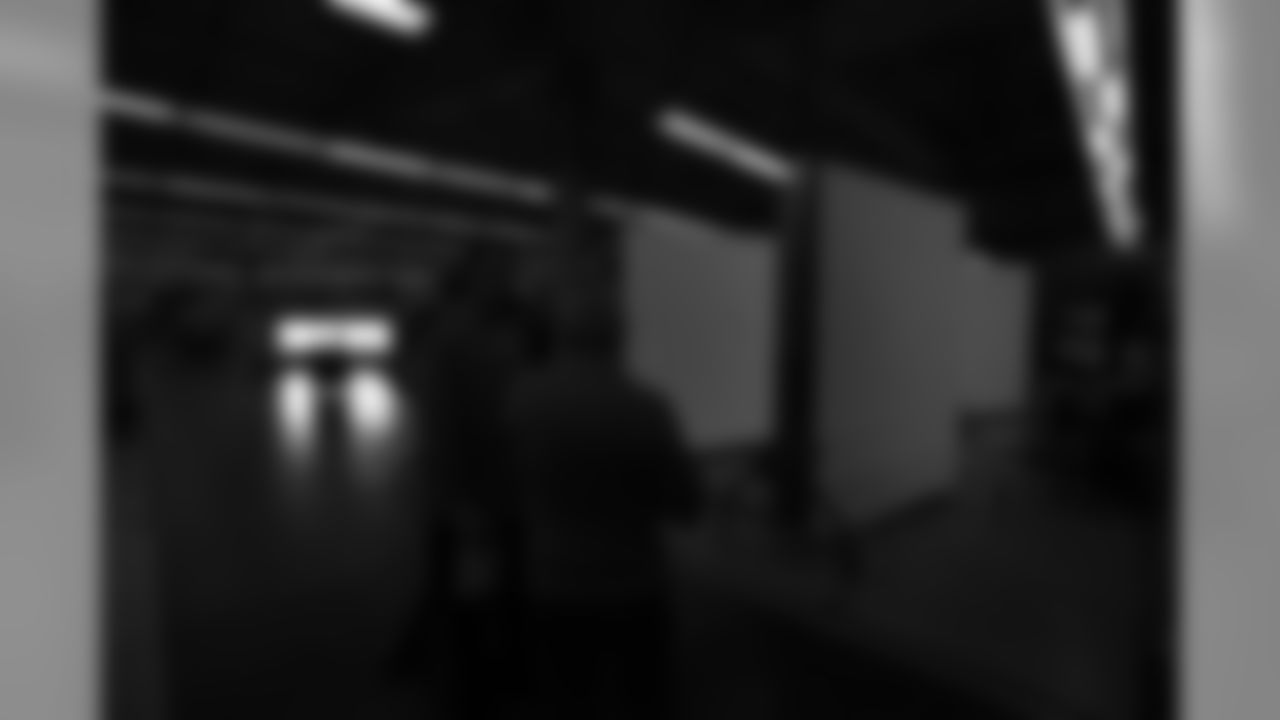
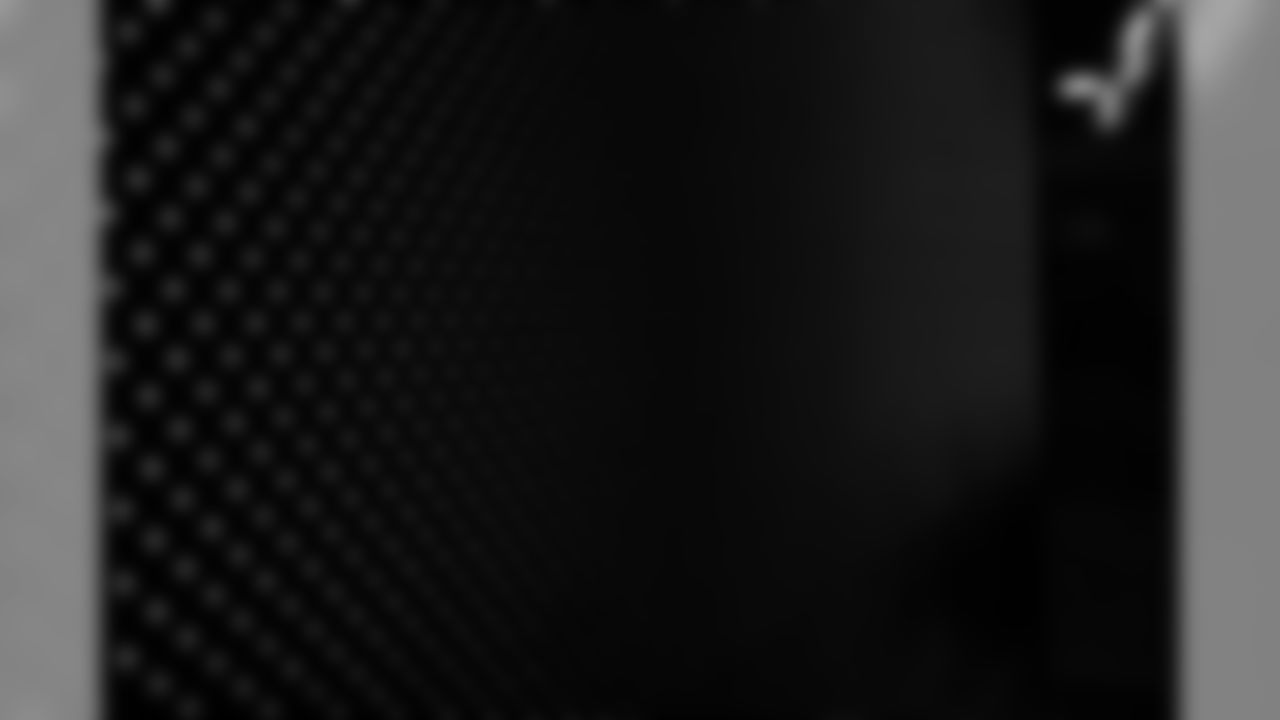
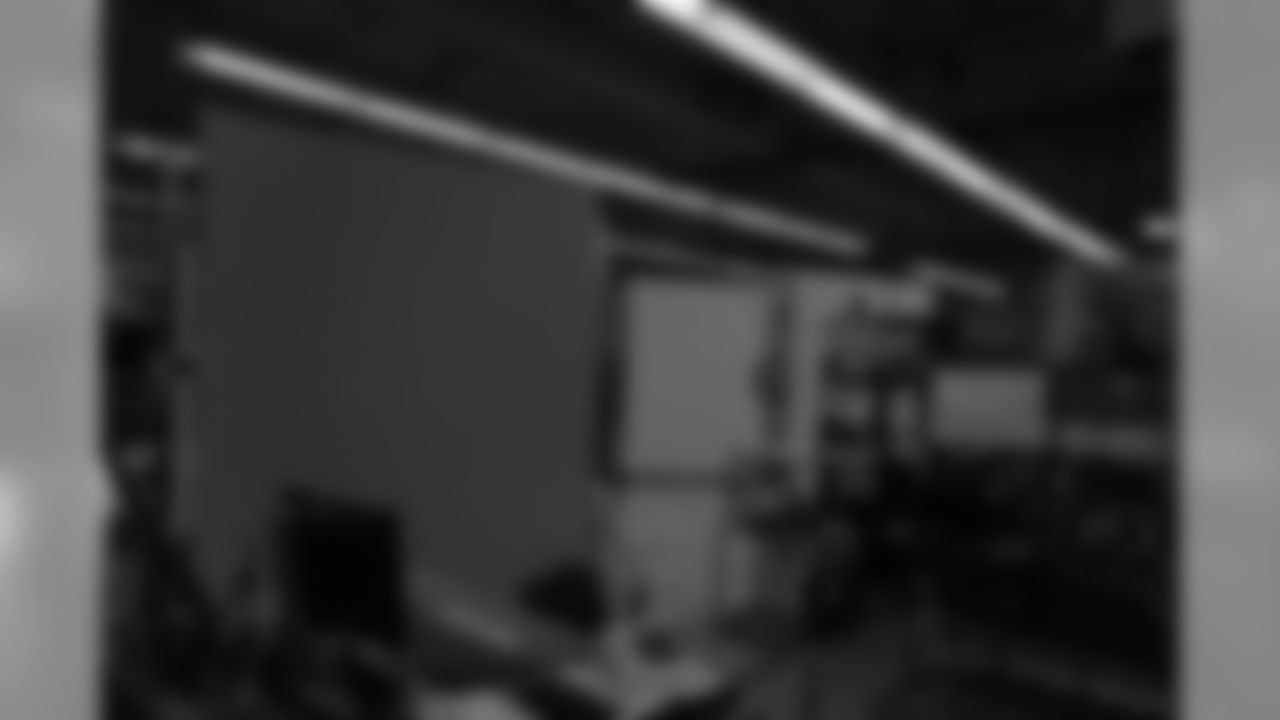
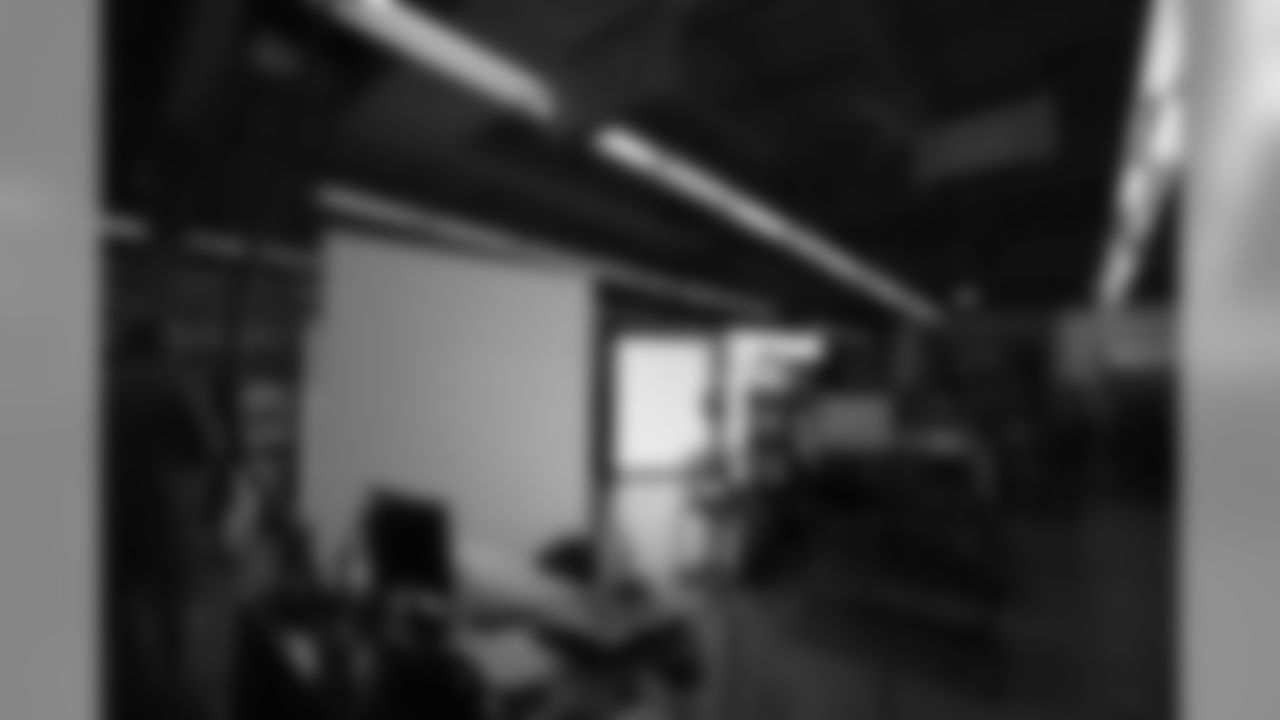
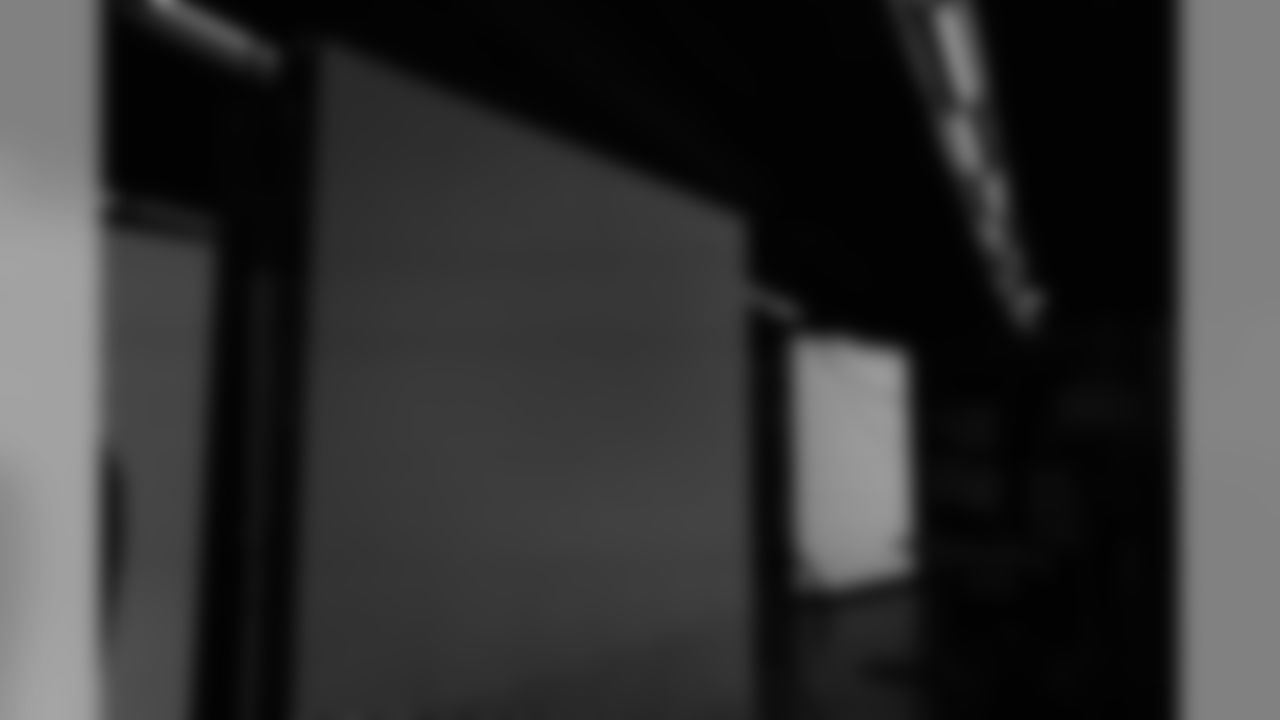
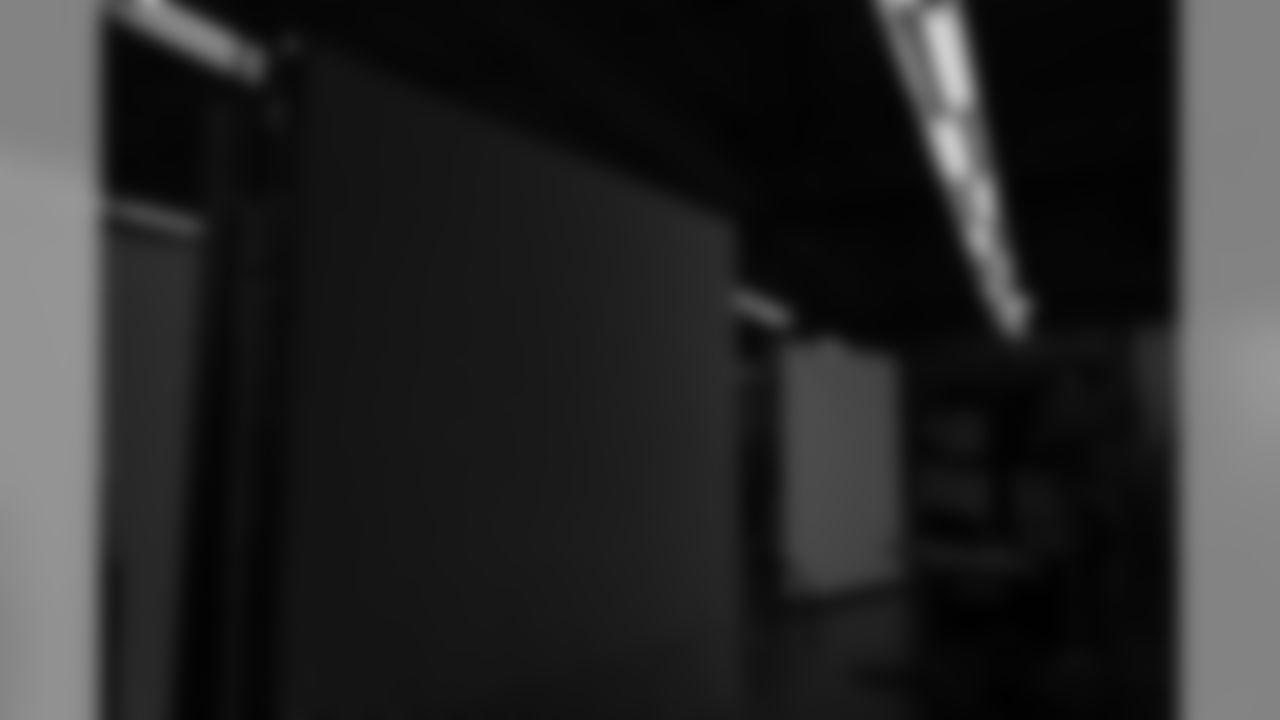

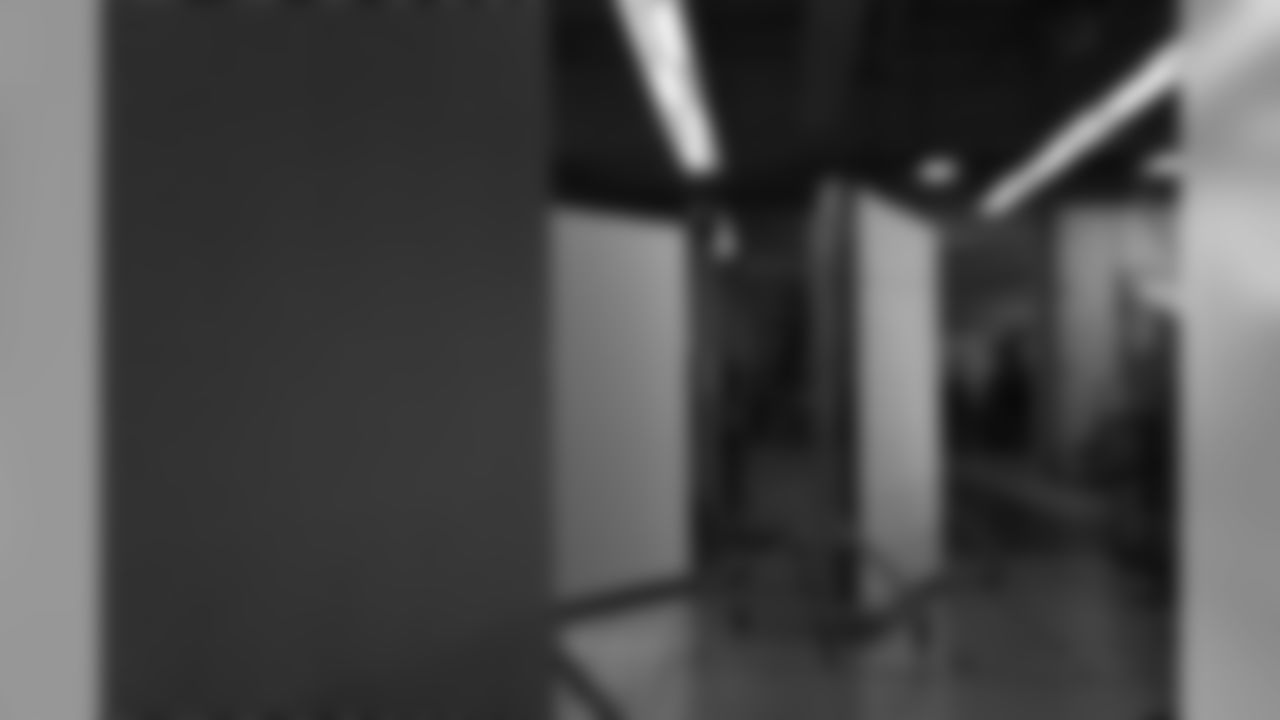
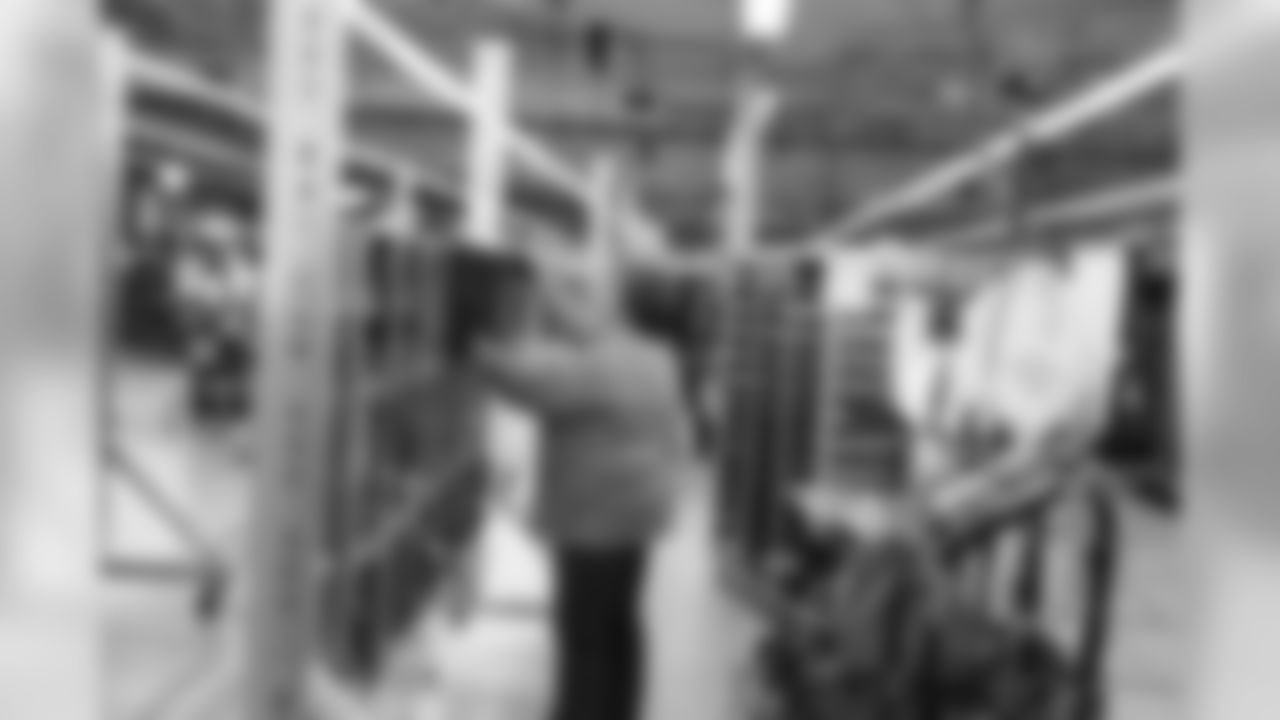
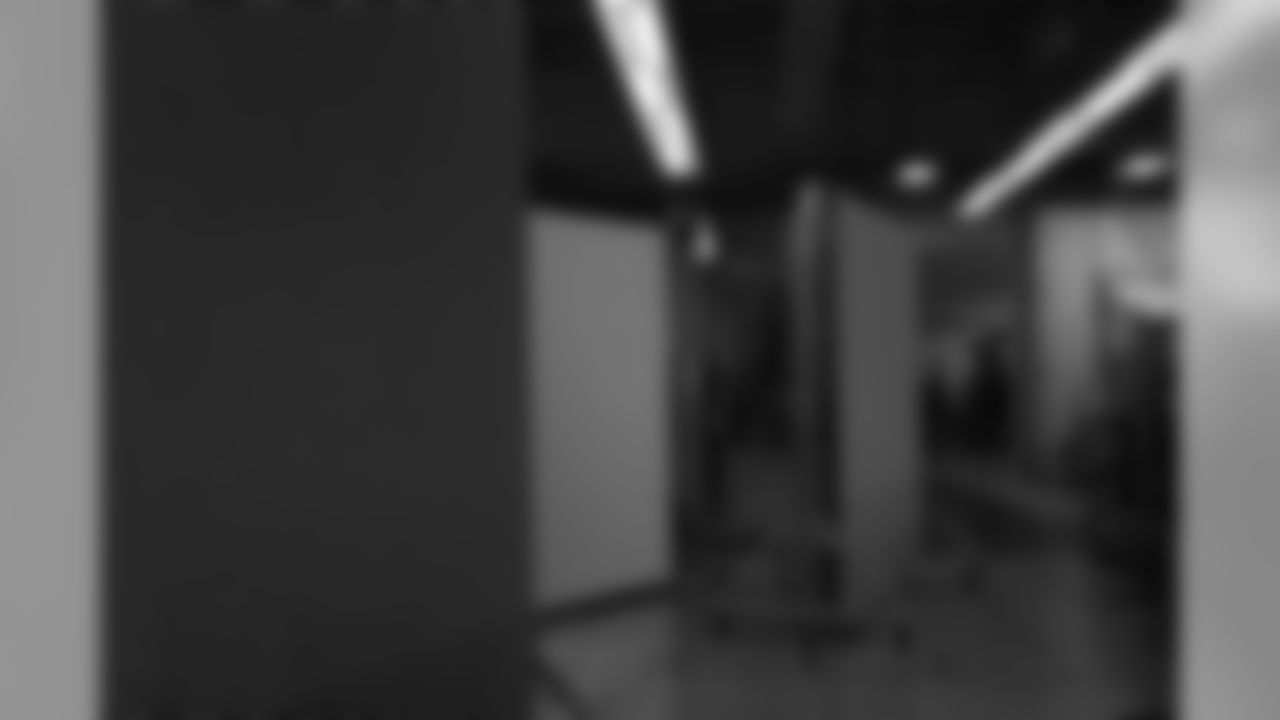
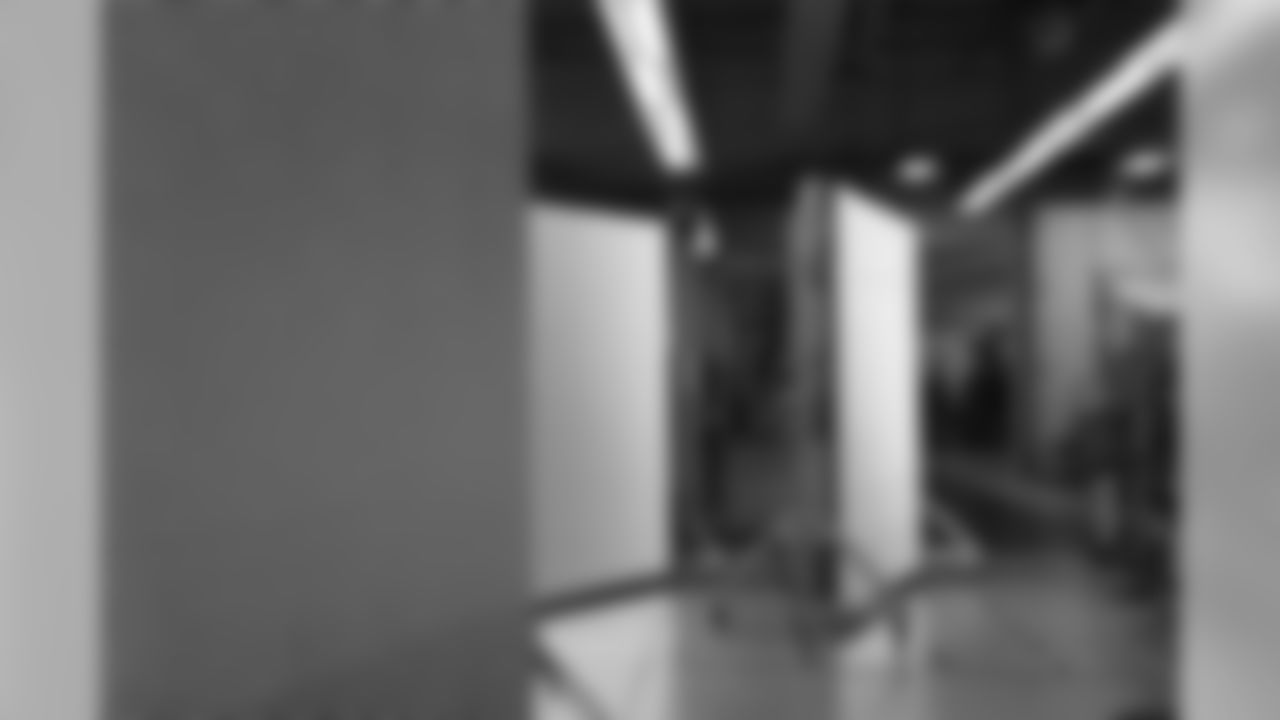
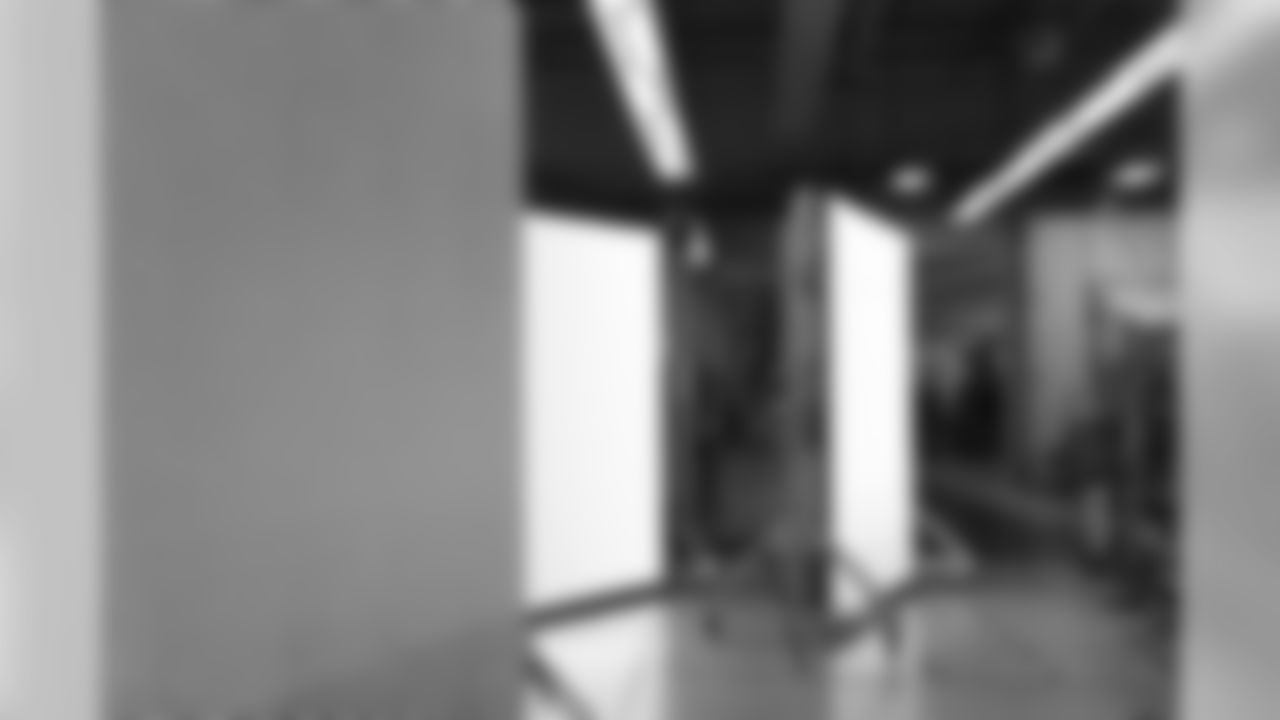
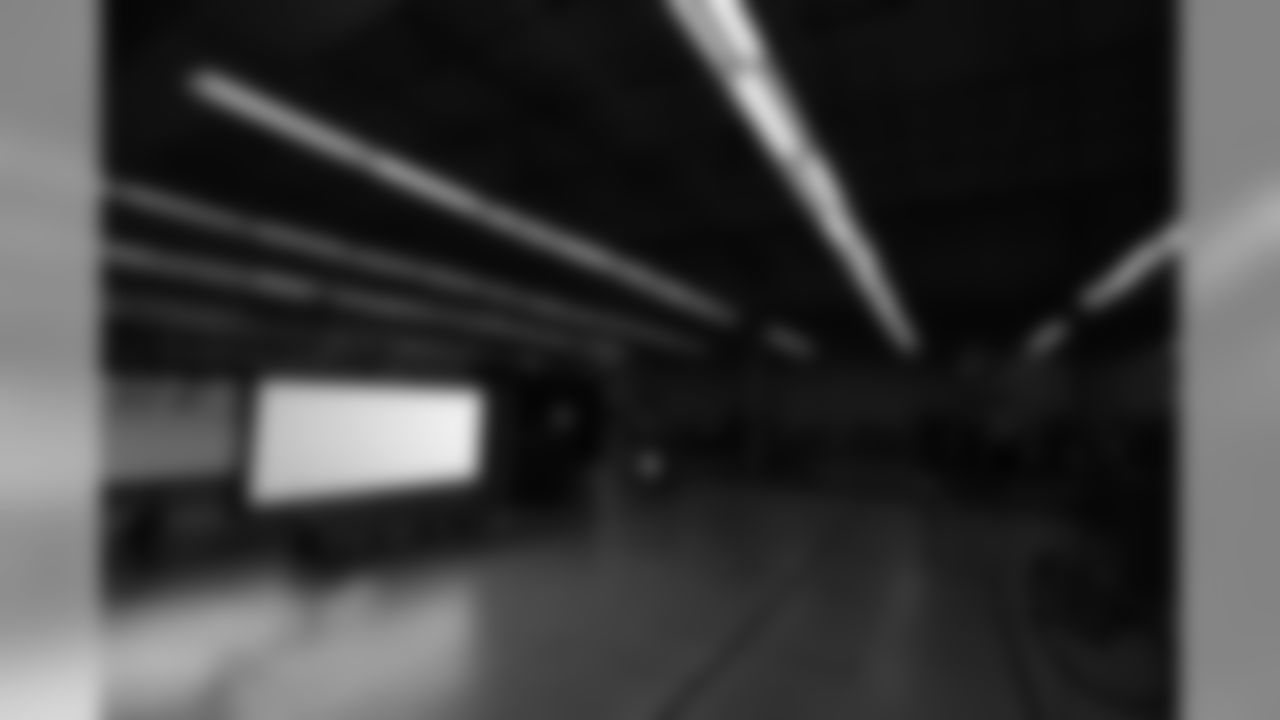
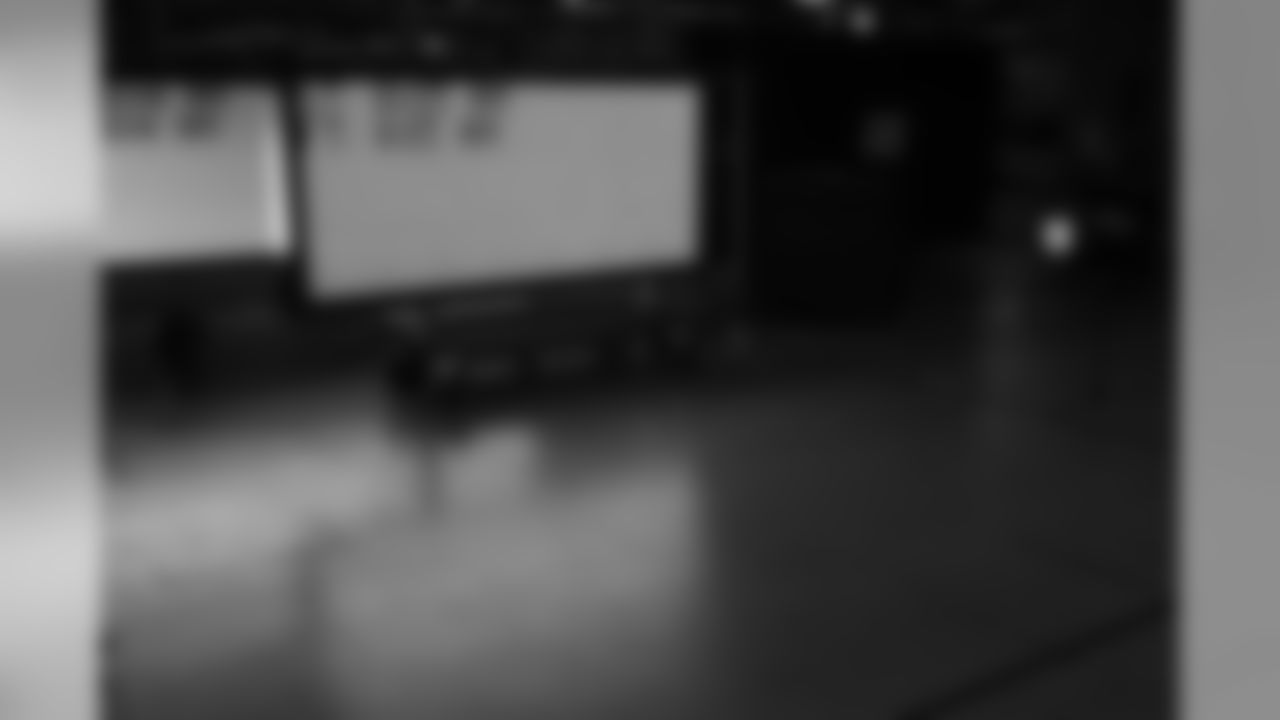
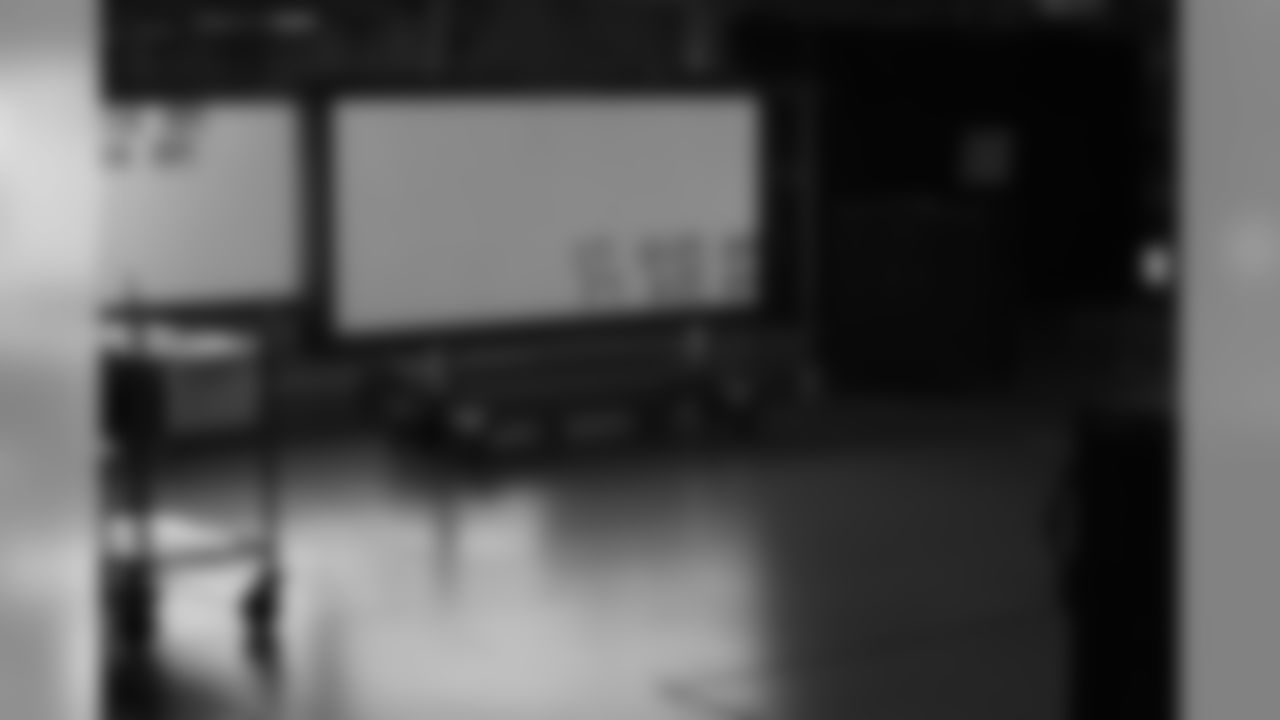
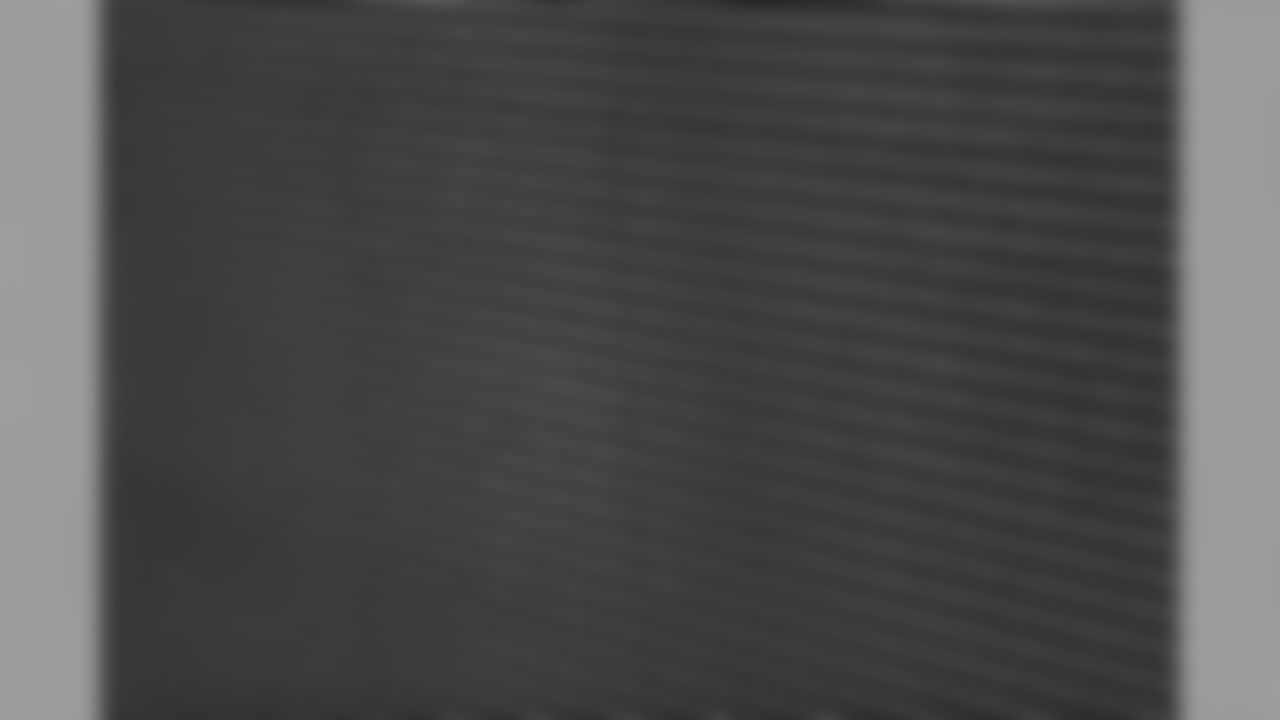
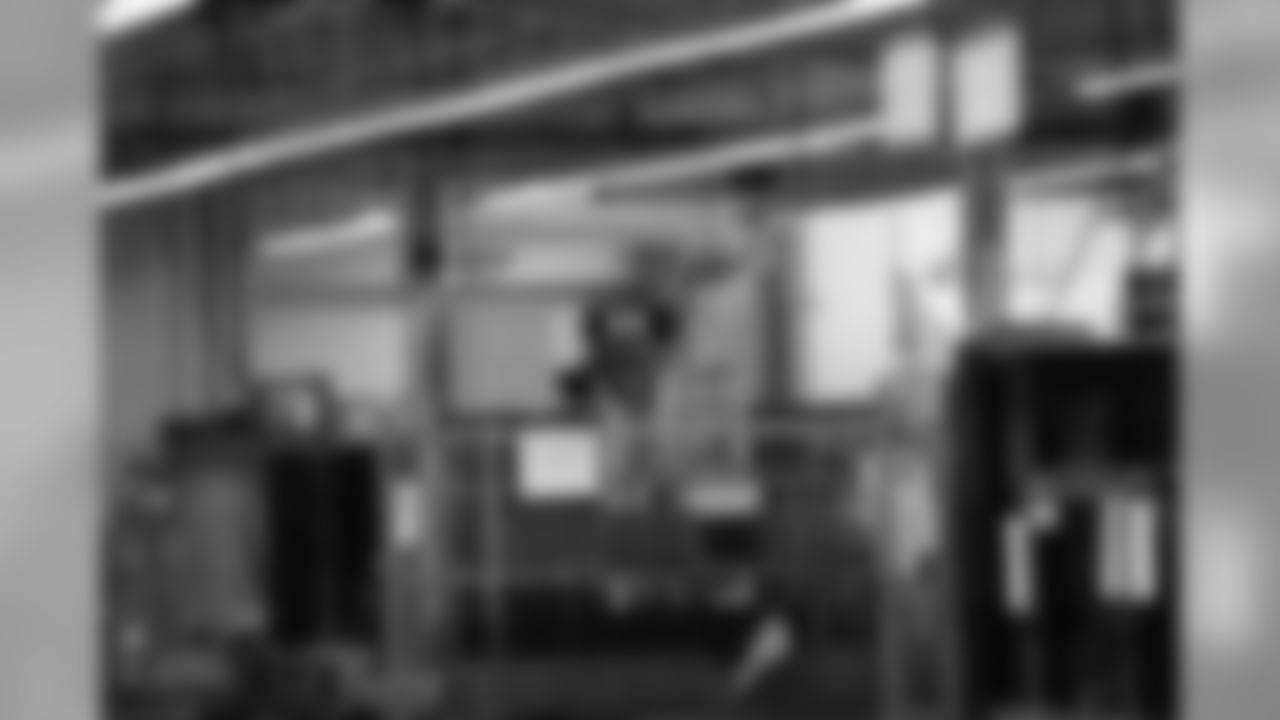
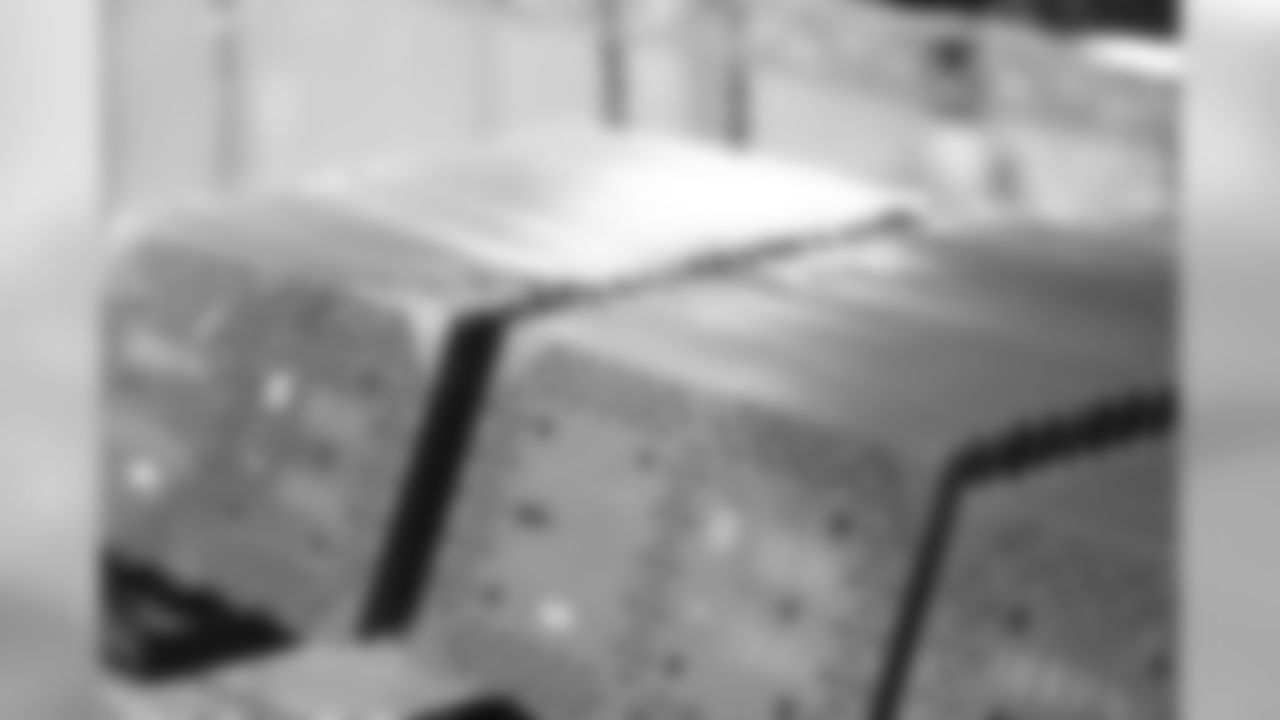
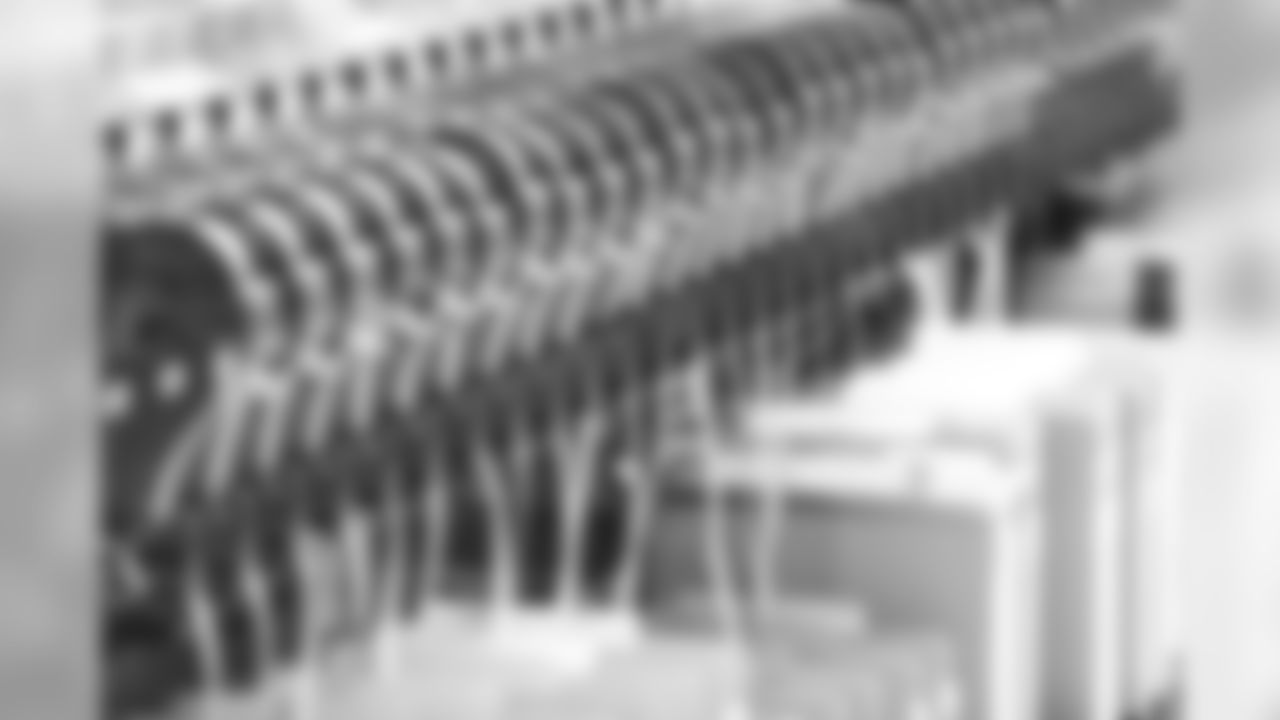
One 13-mm pixel is one red, one green and one blue combined, assembled into programmable units. Components — 80,000 parts an hour that are 1 mm x 3 mm — are placed within 1 mm of accuracy by a Ferrari of a machine. Eventually the units are covered with a gel that will shield the electronic components from water or harsh elements.
"We ship these all over the world, so the conditions change dramatically, from very dry, hot conditions to cold and wet conditions," Quackenbush said.
They are sent through ovens that help with finalizing the soldering and covered with a louvered plastic that's received a special black paint job. Having a uniform black paint on that plastic is critical for color consistency.
"That contrast is really important to the performance of the display," Quackenbush said. "Black is a difficult color to get right, so all of these louvers are done at the same time with the same process to assure quality."
Red LEDs seem to be most difficult to keep consistent, but purple can be a little tricky too.
"You can put the color purple up there, but it's got to be Vikings Purple," Ohm said. "If you don't get black right, nothing else will be right."
Each of those units is then built into panels that are approximately 9-feet, 7-inches tall by 6 feet wide for shipment. Prior to hitting the road, however, the 9-by-6ers go through "burn-in," where they are hooked up to a computer for diagnostic tests as they flash red, green, blue, and white, a glow created from the combination of all three at once.
Once delivered to the construction site, the panels will be united with a special frame system tucked behind the video layer to allow seamless application so an image can be experienced larger than life.
Bubba Waterfield, team lead for final assembly production who has worked at the Redwood Falls location for eight years, said working on this project is "an honor, a privilege."
"It's our team, it's nice to know they chose us, they wanted us to be a part of this and the fact that they trusted us enough to make this because this is huge," Waterfield said. "It's been exciting ever since we found out. We're building it one piece at a time, like the old Johnny Cash song."
A considerable amount of teamwork has gone into each 9-by-6er by the time it reaches the area where Waterfield works, including planning before the LEDs are pulled from boxes and placed on the assembly line. Waterfield said he enjoys his role when the boards near the goal line and is appreciative of co-workers who got them there.
"We want our work to be quality because if something has a blemish on it, it comes back on us, so we try to make sure everything is quality as we can get it," Waterfield said. "We're representing Daktronics, we're representing Minnesota, we're representing the Vikings. It's amazing the quality displays we can make."
It was apparent that working on the U.S. Bank Stadium scoreboards is a point of pride for the 200 employees who will be the only ones in the industry to say that the boards used by an NFL team were made in their home state.
A Vikings car flag was attached to an I-beam above a woodworker who wore a purple Vikings hardhat as he ripped lumber to be used for shipping crates. On the production line, another worker opted for a more comical hat complete with horns. There were also jerseys and other Vikings shirts beneath smocks worn to reduce static electricity.
"The sense of pride that was shown not only in the factory but in the community when we were awarded the job right in our backyard was tremendous," said Quackenbush, who has risen through the ranks in his eight years.
"Every week since then, people pass me all the time and ask, 'Are you working on it? When are you going to get it done? When is it shipping?' " he explained. "People (in the community) are so thrilled and proud to be part of that, even though they're not working for us."
Daktronics was founded in 1968 by Dr. Aelred Kurtenbach and Dr. Duane Sander, professors of electrical engineering at South Dakota State University. It has grown into a multinational company since its first product, an electronic vote tallying system for state legislatures. Daktronics introduced its first sports scoreboard in 1971 when it launched the Matside® device that could be placed on the mats during wrestling matches. The choice placement enabled fans to keep track of the score without taking their eyes off the action.
The location of U.S. Bank Stadium's main and secondary video boards behind the respective east and west end zones is lower than many stadiums and closer to more seating sections. The decision will enable fans to see replays by moving their eyes instead of tilting their heads. That proximity is expected to be among the closest in the NFL.
"When a fan first walks in there and sees the stadium and everything lit up, I want them to say 'Wow,' " Matt Kurtenbach said.
It's a continually expanding threshold to reach, even if lessons learned help productivity and further innovations.
"As consumers' appetite for bigger and better images has expanded, viewers expect an HD image, so we're putting pixels closer and closer together," Kurtenbach said. "The processing behind the signals that we're sending out to the LEDs to provide that is more complex in order to provide that HD image.
"On the flip side, as we've been designing and building these displays for between 15 and 20 years, we've really refined the manufacturing," he added. "It's simpler than it used to be because we've just figured out better ways to design and produce the product. What we're producing though, the electronic architecture has become much more complex as HD has come into the fold."
Daktronics switched from incandescent bulbs to LEDs between the mid-1990s and early 2000s, but another leap has occurred in the past five years.
"We've seen first-hand changes in size and all of the resolution of the video displays," Kurtenbach said. "We would be doing the scoring sections and partnered with, like Sony, which probably has the most famous brand name [JumboTron] in the industry to install their technology for video replay. Over the years, the LED technology progressed, and we were able to offer those products ourselves. Companies like Sony are still involved but they don't manufacture them anymore."
Although the incandescent light bulbs have become a thing of the past, Daktronics still values bright ideas.
Quackenbush said the company challenges employees to come up with new ideas each month. Proposals are written, and the amount of ideas is tracked. This past October set a record, which ironically isn't measured by technology but by three plastic tubes taped together near a job board. Each idea results in a neon pink, green or orange ping pong ball randomly placed one on another until the "scoreboard" is cleared for another month.
"My job is change champion," Quackenbush said. "Change is hard, so getting buy-in to those changes is a part of it. If I believe in the process we're going to go through to change one to the other, my job is to make sure everyone understands why we're doing something. This is a very fluid industry, so to be on top as long as Daktronics has been on top, you don't do that by sitting still."